Chemical vapor deposition (CVD) and physical vapor deposition (PVD) are two widely used techniques for applying tool coatings, each with distinct processes, advantages, and limitations. CVD involves chemical reactions at relatively lower temperatures, producing dense, uniform coatings suitable for complex geometries. PVD, on the other hand, operates in a vacuum at high temperatures, using physical processes to deposit a broader range of materials, including metals, alloys, and ceramics. While PVD coatings are less dense and faster to apply, CVD coatings are denser, more uniform, and better suited for intricate shapes. Both methods require sophisticated equipment and cleanroom facilities, but their applications differ based on the desired coating properties and tool requirements.
Key Points Explained:
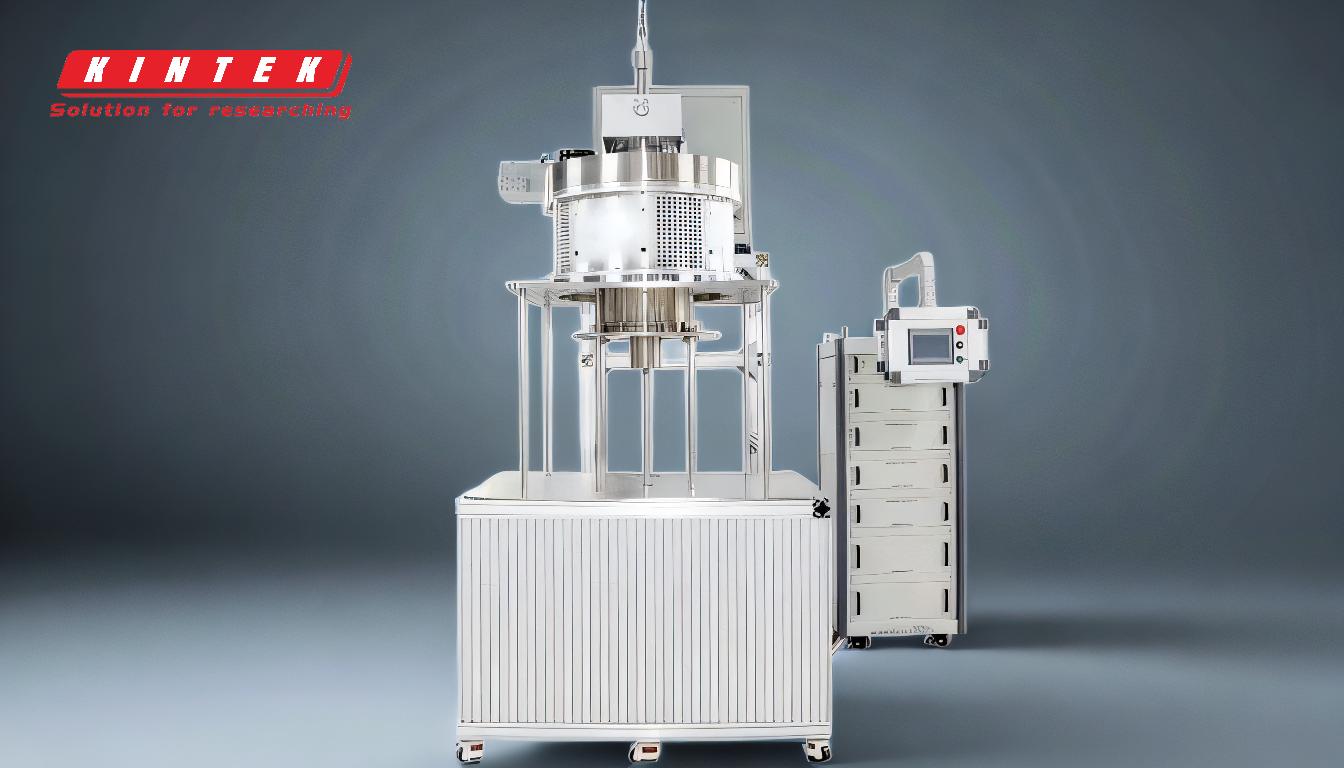
-
Material Range and Applicability:
- PVD: Can deposit a wide variety of materials, including metals, alloys, and ceramics. This versatility makes it suitable for applications requiring diverse material properties.
- CVD: Primarily limited to ceramics and polymers. Its chemical nature restricts the range of materials but allows for high-purity films and complex material synthesis.
-
Process Conditions:
- PVD: Conducted in a vacuum at high temperatures, involving physical processes like evaporation or sputtering. This requires specialized equipment, vacuum conditions, and skilled operators.
- CVD: Operates at lower temperatures compared to PVD, relying on chemical reactions to deposit coatings. It does not require ultra-high vacuum conditions, making it more economical in some cases.
-
Coating Properties:
- PVD: Produces less dense and less uniform coatings but is faster to apply. The line-of-sight impingement process limits its ability to coat complex geometries uniformly.
- CVD: Creates denser, more uniform coatings with excellent throwing power, allowing it to coat holes, deep recesses, and intricate shapes effectively.
-
Deposition Rates and Thickness:
- PVD: Generally has lower deposition rates, but techniques like electron beam PVD (EBPVD) can achieve high rates (0.1 to 100 μm/min) with high material utilization efficiency.
- CVD: Offers higher deposition rates and can produce thicker coatings, ranging from nanometers to less than 20 microns, compared to conventional methods.
-
Temperature and Environmental Considerations:
- PVD: Requires high temperatures and vacuum conditions, which can limit its use for heat-sensitive substrates. It also necessitates cooling systems for heat dissipation.
- CVD: Operates at lower temperatures (500°–1100°C) and does not produce corrosive byproducts, making it more environmentally friendly and suitable for a broader range of substrates.
-
Application Suitability:
- PVD: Ideal for applications requiring fast coating processes and a wide range of materials, such as wear-resistant and anti-corrosion coatings.
- CVD: Better suited for applications needing high-purity, uniform coatings on complex shapes, such as semiconductor devices and advanced tooling.
-
Economic and Operational Factors:
- PVD: Requires significant investment in vacuum systems and skilled labor, but its faster application time can offset costs in high-volume production.
- CVD: Often more economical due to higher deposition rates and the ability to coat complex geometries without ultra-high vacuum requirements.
In summary, the choice between CVD and PVD for tool coating depends on the specific requirements of the application, including material properties, coating uniformity, deposition rates, and geometric complexity. Both methods have their unique advantages and limitations, making them complementary rather than competing technologies in the field of surface engineering.
Summary Table:
Aspect | CVD | PVD |
---|---|---|
Material Range | Primarily ceramics and polymers | Metals, alloys, and ceramics |
Process Conditions | Lower temperatures, chemical reactions, no ultra-high vacuum required | High temperatures, vacuum, physical processes like evaporation/sputtering |
Coating Properties | Denser, more uniform, excellent for complex shapes | Less dense, faster application, limited by line-of-sight impingement |
Deposition Rates | Higher rates, thicker coatings (nanometers to <20 microns) | Lower rates, but EBPVD can achieve high rates (0.1 to 100 μm/min) |
Temperature & Environment | Lower temperatures (500°–1100°C), environmentally friendly | High temperatures, vacuum, requires cooling systems |
Application Suitability | High-purity, uniform coatings for complex shapes (e.g., semiconductors) | Fast coating, diverse materials (e.g., wear-resistant, anti-corrosion) |
Economic Factors | Economical for complex geometries, higher deposition rates | High initial investment, but faster application offsets costs |
Need help choosing between CVD and PVD for your tool coating needs? Contact our experts today for tailored solutions!