CVD (Chemical Vapor Deposition) and PVD (Physical Vapor Deposition) are two widely used coating techniques for inserts, each with distinct processes, properties, and applications. CVD involves chemical reactions at high temperatures (800–1000 °C) to deposit thicker coatings (10–20 μm), while PVD uses physical vaporization at lower temperatures (250–500 °C) to create thinner, ultra-hard films (3–5 μm). CVD coatings are denser and more uniform but can introduce tensile stress and fine cracks due to high processing temperatures. PVD coatings, on the other hand, form compressive stress and are ideal for precision applications requiring smooth, durable surfaces. The choice between CVD and PVD depends on factors such as coating thickness, operating temperature, and the specific application requirements.
Key Points Explained:
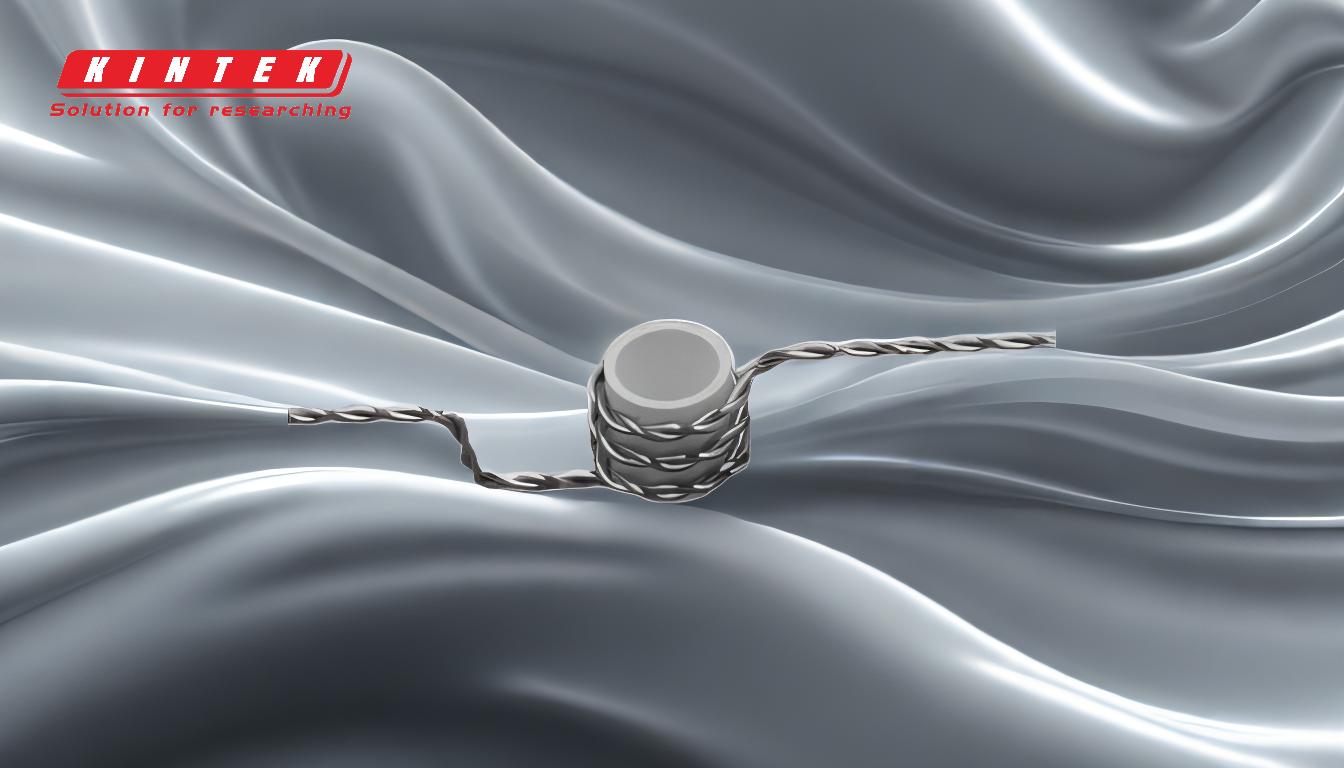
-
Deposition Mechanism:
- CVD: Involves chemical reactions between gaseous precursors and the substrate at high temperatures (800–1000 °C). This results in a multidirectional deposition, where the coating forms uniformly on all surfaces, including complex geometries.
- PVD: Uses a physical process, such as sputtering or evaporation, to deposit material directly onto the substrate in a line-of-sight manner. This limits coverage to exposed surfaces but allows for precise control over film properties.
-
Operating Temperature:
- CVD: Requires high temperatures (800–1000 °C), which can affect the substrate's mechanical properties and lead to tensile stress or fine cracks in the coating.
- PVD: Operates at lower temperatures (250–500 °C), making it suitable for heat-sensitive materials and reducing the risk of substrate deformation.
-
Coating Thickness and Uniformity:
- CVD: Produces thicker coatings (10–20 μm) with excellent uniformity, making it ideal for applications requiring high wear resistance and durability.
- PVD: Forms thinner coatings (3–5 μm) with superior smoothness and precision, suitable for applications demanding fine surface finishes and minimal dimensional changes.
-
Stress and Adhesion:
- CVD: High processing temperatures can lead to tensile stress in the coating, which may cause micro-cracks and reduced adhesion in some cases.
- PVD: Generates compressive stress during cooling, enhancing coating adhesion and durability, especially in high-precision applications.
-
Material Compatibility:
- CVD: Primarily used for ceramics and polymers, offering excellent chemical resistance and thermal stability.
- PVD: Can deposit a broader range of materials, including metals, alloys, and ceramics, providing greater versatility for various applications.
-
Applications:
- CVD: Commonly used in industries requiring thick, wear-resistant coatings, such as cutting tools, aerospace components, and semiconductor manufacturing.
- PVD: Preferred for applications needing thin, smooth, and precise coatings, such as medical devices, optical components, and decorative finishes.
-
Cost and Processing Time:
- CVD: Generally more expensive and time-consuming due to the high temperatures and complex chemical processes involved.
- PVD: Offers faster processing times and lower costs, making it more economical for high-volume production.
In summary, the choice between CVD and PVD coating inserts depends on the specific requirements of the application, including coating thickness, operating temperature, material compatibility, and desired surface properties. CVD is ideal for thick, uniform coatings in high-temperature environments, while PVD excels in precision applications requiring smooth, durable surfaces at lower temperatures.
Summary Table:
Aspect | CVD | PVD |
---|---|---|
Deposition Mechanism | Chemical reactions at high temps (800–1000 °C), multidirectional | Physical vaporization at lower temps (250–500 °C), line-of-sight |
Coating Thickness | Thicker (10–20 μm), uniform | Thinner (3–5 μm), ultra-hard and smooth |
Operating Temperature | High (800–1000 °C), may cause tensile stress | Low (250–500 °C), reduces substrate deformation |
Stress and Adhesion | Tensile stress, potential micro-cracks | Compressive stress, enhanced adhesion |
Material Compatibility | Ceramics, polymers, high chemical resistance | Metals, alloys, ceramics, versatile |
Applications | Cutting tools, aerospace, semiconductors | Medical devices, optics, decorative finishes |
Cost and Processing | Expensive, time-consuming | Cost-effective, faster processing |
Need help choosing between CVD and PVD for your application? Contact our experts today for tailored advice!