CVD (Chemical Vapor Deposition) and PVD (Physical Vapor Deposition) are two widely used techniques for depositing thin films onto substrates, each with distinct processes, advantages, and applications. PVD involves the physical vaporization of solid materials, which are then deposited onto the substrate, typically at lower temperatures (250°C~450°C). In contrast, CVD relies on chemical reactions between gaseous precursors and the substrate, occurring at higher temperatures (450°C to 1050°C). PVD coatings are less dense and faster to apply, while CVD coatings are denser, more uniform, and suitable for more complex geometries. The choice between the two depends on factors such as material compatibility, coating requirements, and the specific application.
Key Points Explained:
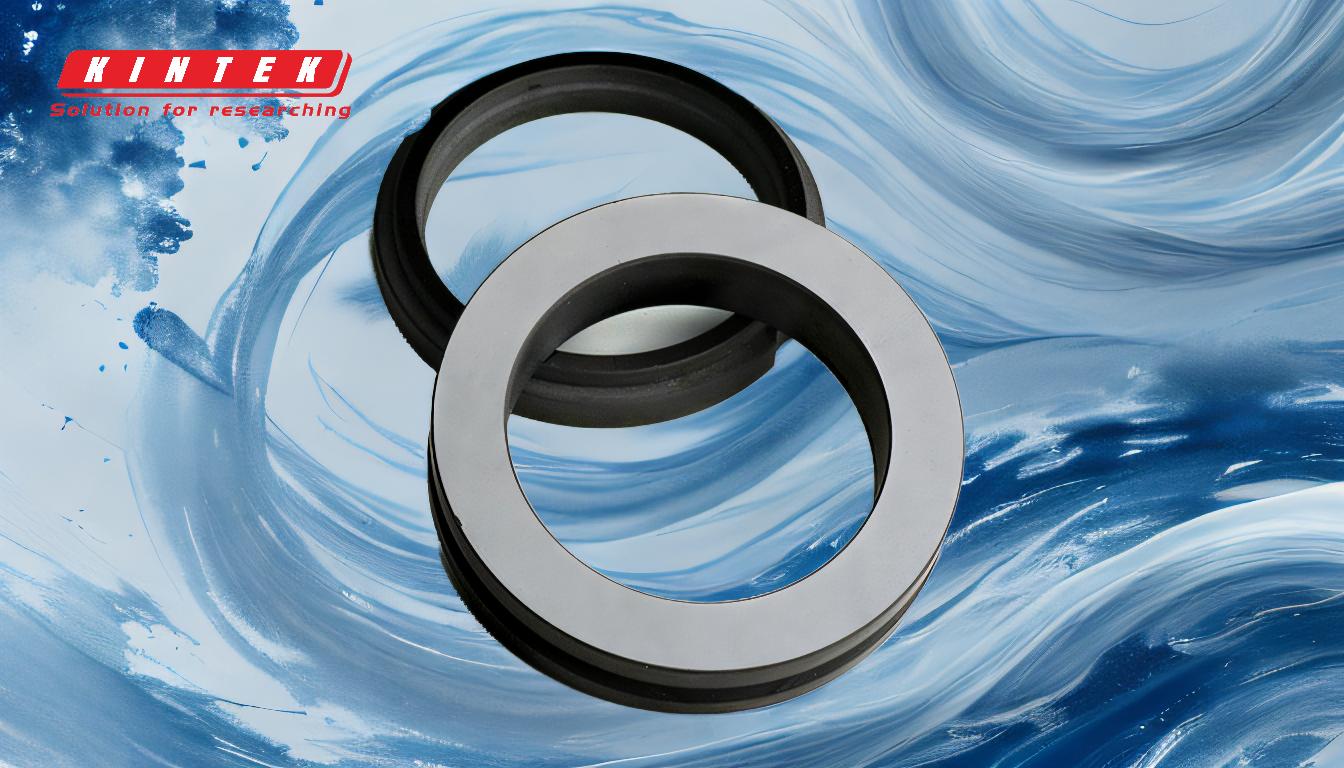
-
Deposition Mechanism:
- PVD: Involves the physical vaporization of solid materials, which are then deposited onto the substrate. This is a line-of-sight process, meaning the material is deposited directly onto the substrate without chemical interaction.
- CVD: Relies on chemical reactions between gaseous precursors and the substrate. The process is multidirectional, allowing for uniform coating on complex geometries.
-
Temperature Requirements:
- PVD: Operates at relatively lower temperatures, typically between 250°C and 450°C. This makes it suitable for substrates that cannot withstand high temperatures.
- CVD: Requires higher temperatures, ranging from 450°C to 1050°C. This high-temperature environment facilitates the chemical reactions necessary for deposition.
-
Coating Materials:
- PVD: Can deposit a broader range of materials, including metals, alloys, and ceramics. This versatility makes PVD suitable for various applications.
- CVD: Typically limited to ceramics and polymers. The process is more specialized and is often used for applications requiring high-purity coatings.
-
Coating Characteristics:
- PVD: Coatings are less dense and less uniform but can be applied more quickly. This makes PVD ideal for applications where speed is a priority.
- CVD: Coatings are denser and more uniform, providing better coverage and adhesion. However, the process takes longer, making it less suitable for high-throughput applications.
-
Applications:
- PVD: Commonly used in applications requiring hard, wear-resistant coatings, such as cutting tools, decorative finishes, and electronic components.
- CVD: Often employed in applications requiring high-purity, uniform coatings, such as semiconductor manufacturing, optical coatings, and protective layers for high-temperature environments.
-
Process Environment:
- PVD: Typically conducted in a vacuum environment, which helps to minimize contamination and improve coating quality.
- CVD: Can be performed in various environments, including vacuum, atmospheric pressure, and low-pressure conditions, depending on the specific requirements of the application.
-
Cost and Complexity:
- PVD: Generally less expensive and less complex than CVD, making it a more cost-effective option for many applications.
- CVD: More complex and costly due to the need for high temperatures and specialized equipment. However, the superior coating quality often justifies the higher cost.
By understanding these key differences, purchasers can make informed decisions about which coating technique best suits their specific needs, whether they prioritize speed, cost, coating quality, or material compatibility.
Summary Table:
Aspect | PVD | CVD |
---|---|---|
Deposition Mechanism | Physical vaporization of solid materials, line-of-sight process | Chemical reactions between gaseous precursors, multidirectional process |
Temperature Range | 250°C ~ 450°C | 450°C ~ 1050°C |
Coating Materials | Metals, alloys, ceramics | Ceramics, polymers |
Coating Characteristics | Less dense, less uniform, faster application | Denser, more uniform, slower application |
Applications | Cutting tools, decorative finishes, electronic components | Semiconductor manufacturing, optical coatings, high-temperature layers |
Process Environment | Vacuum | Vacuum, atmospheric pressure, low-pressure |
Cost & Complexity | Less expensive, less complex | More expensive, more complex |
Need help choosing between CVD and PVD inserts? Contact our experts today for tailored advice!