CVD (Chemical Vapor Deposition) and sputter coating (a type of PVD, Physical Vapor Deposition) are both widely used thin-film deposition techniques, but they differ significantly in their principles, processes, and applications. CVD involves chemical reactions between gaseous precursors to form a thin film on a substrate, while sputter coating relies on physical processes like atomic collisions to deposit material onto a surface. CVD is a non-line-of-sight process, allowing it to coat complex geometries, and it typically operates at higher temperatures, resulting in superior adhesion and denser coatings. Sputter coating, on the other hand, is a line-of-sight process, limiting its ability to coat hidden areas, but it can deposit a broader range of materials and operates at lower temperatures. Understanding these differences is crucial for selecting the appropriate method based on the application requirements.
Key Points Explained:
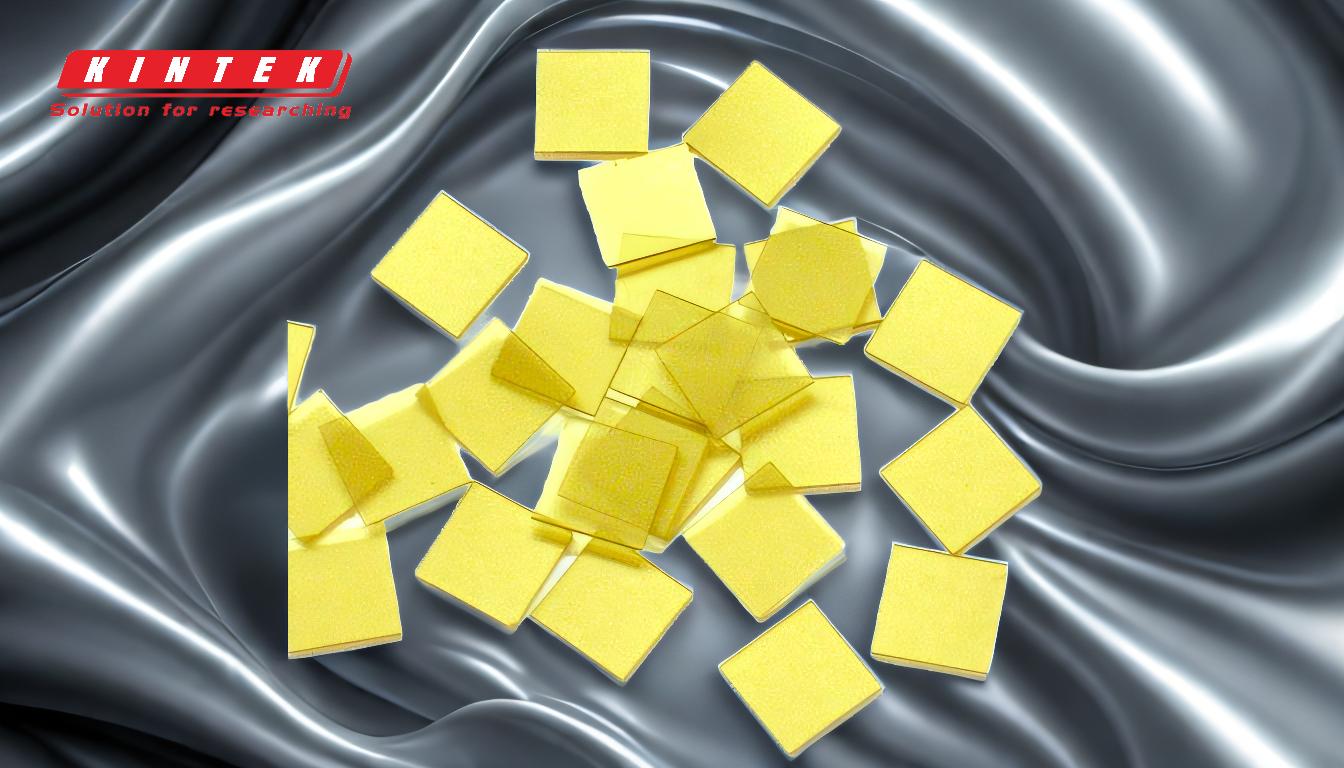
-
Principle of Operation:
-
CVD: Involves chemical reactions between gaseous precursors to form a thin film on the substrate. The process is driven by high temperatures and often occurs under vacuum conditions.
- Example: A gas like methane (CH₄) decomposes at high temperatures to deposit carbon on a substrate.
-
Sputter Coating: Relies on physical processes, where a target material is bombarded with high-energy ions, causing atoms to be ejected and deposited onto the substrate.
- Example: Argon ions collide with a metal target, sputtering metal atoms onto a substrate.
-
CVD: Involves chemical reactions between gaseous precursors to form a thin film on the substrate. The process is driven by high temperatures and often occurs under vacuum conditions.
-
Temperature Requirements:
- CVD: Typically operates at high temperatures (800–1000 °C), which can limit the types of base materials that can be coated due to thermal degradation or reactivity issues.
- Sputter Coating: Operates at lower temperatures (around 500 °C), making it suitable for heat-sensitive materials.
-
Line-of-Sight vs. Non-Line-of-Sight:
- CVD: Non-line-of-sight process, meaning the coating gas can reach and coat all areas of a part, including complex geometries like threads, blind holes, and interior surfaces.
- Sputter Coating: Line-of-sight process, limiting its ability to coat hidden or recessed areas uniformly.
-
Coating Adhesion and Density:
- CVD: Produces coatings with superior adhesion due to chemical bonding during the reaction. The coatings are also denser and more uniform.
- Sputter Coating: Adhesion is typically weaker compared to CVD, and the coatings are less dense and less uniform.
-
Material Compatibility:
- CVD: Primarily used for ceramics and polymers. Limited by the need for compatible chemical precursors and high temperatures.
- Sputter Coating: Can deposit a broader range of materials, including metals, alloys, and ceramics, due to its physical nature.
-
Processing Time:
- CVD: Generally slower due to the chemical reaction process and high-temperature requirements.
- Sputter Coating: Faster deposition rates, making it more efficient for certain applications.
-
Applications:
- CVD: Widely used in industries requiring high-performance coatings, such as semiconductor manufacturing, tool coatings, and protective layers on metals.
- Sputter Coating: Commonly used for optical coatings, decorative finishes, and thin-film electronics.
-
Coating Thickness:
- CVD: Typically produces thicker coatings (10–20 μm) but is limited by coating stress.
- Sputter Coating: Produces thinner coatings (3–5 μm), which are suitable for applications requiring precise thickness control.
By understanding these key differences, equipment and consumable purchasers can make informed decisions about which coating method is best suited for their specific needs, whether it involves high-temperature resistance, complex geometries, or material versatility.
Summary Table:
Aspect | CVD | Sputter Coating |
---|---|---|
Principle | Chemical reactions between gaseous precursors. | Physical process involving atomic collisions. |
Temperature | High (800–1000 °C). | Lower (around 500 °C). |
Coating Process | Non-line-of-sight, ideal for complex geometries. | Line-of-sight, limited to exposed surfaces. |
Adhesion & Density | Superior adhesion and denser coatings. | Weaker adhesion, less dense coatings. |
Material Compatibility | Primarily ceramics and polymers. | Broad range, including metals, alloys, and ceramics. |
Processing Time | Slower due to chemical reactions. | Faster deposition rates. |
Applications | Semiconductor manufacturing, tool coatings, protective layers. | Optical coatings, decorative finishes, thin-film electronics. |
Coating Thickness | Thicker coatings (10–20 μm). | Thinner coatings (3–5 μm). |
Need help selecting the right thin-film deposition method? Contact our experts today to discuss your specific requirements!