The primary difference between e-beam evaporation and thermal evaporation lies in the method used to vaporize the material. E-beam evaporation employs a high-energy electron beam to directly heat and vaporize the target material, making it suitable for high-melting-point materials like oxides. In contrast, thermal evaporation uses electric resistance to heat a crucible, which then melts and evaporates the source material, making it ideal for materials with lower melting temperatures. E-beam evaporation offers advantages such as denser thin film coatings, higher deposition rates, and lower impurity risks compared to thermal evaporation.
Key Points Explained:
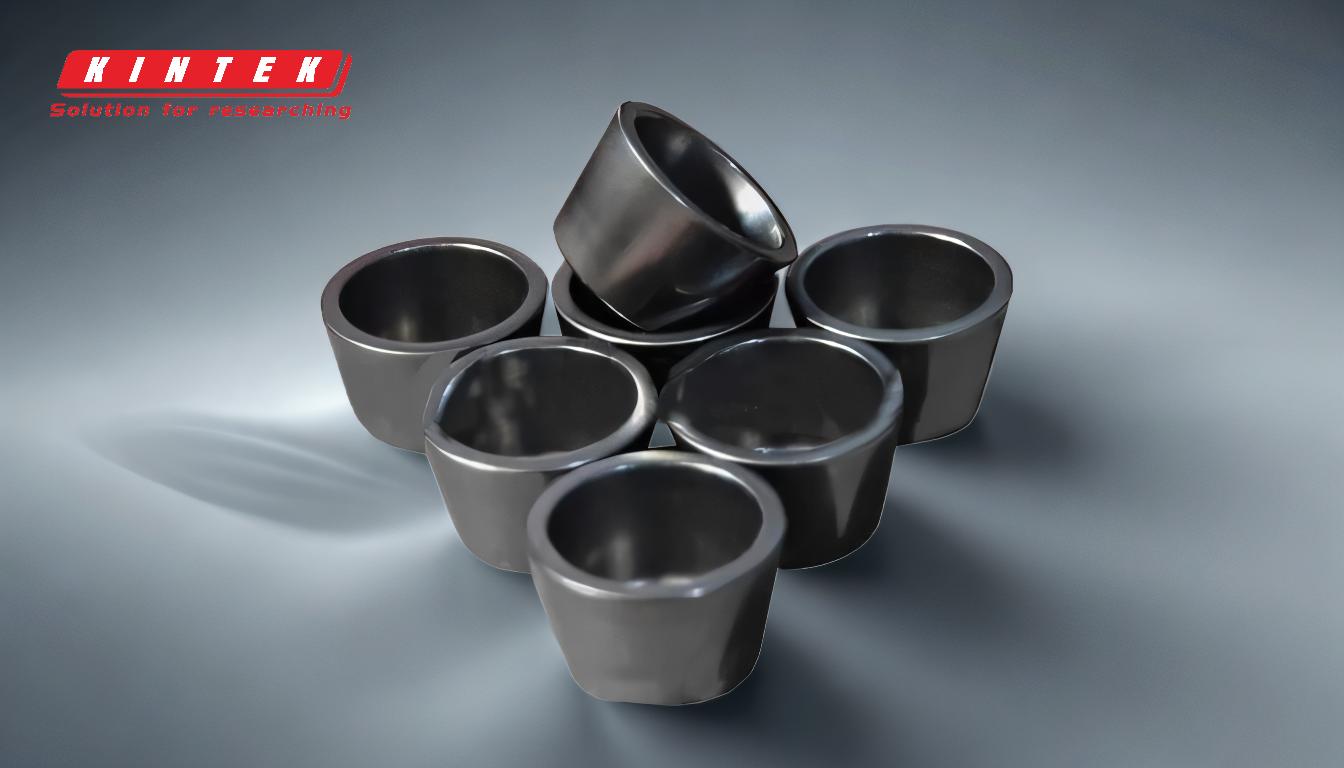
-
Vaporization Method:
- E-beam Evaporation: Uses a high-energy electron beam to directly heat and vaporize the target material. This method transfers kinetic energy to the material, causing it to evaporate.
- Thermal Evaporation: Relies on electric resistance to heat a crucible, which then melts and evaporates the source material. The heat is applied indirectly through the crucible.
-
Material Compatibility:
- E-beam Evaporation: Suitable for high-melting-point materials, such as oxides, that do not sublimate easily during thermal evaporation.
- Thermal Evaporation: Best suited for materials with lower melting temperatures, as it cannot efficiently vaporize high-melting-point materials.
-
Coating Quality:
- E-beam Evaporation: Produces denser thin film coatings due to the high-energy process, resulting in better adhesion and uniformity.
- Thermal Evaporation: Tends to produce less dense coatings, which may require additional steps to achieve comparable quality.
-
Deposition Rate:
- E-beam Evaporation: Offers a higher deposition rate, making it more efficient for large-scale or high-throughput applications.
- Thermal Evaporation: Has a slower deposition rate, which may limit its use in time-sensitive processes.
-
Impurity Risks:
- E-beam Evaporation: Lower risk of impurities because the electron beam directly targets the material, minimizing contamination from the crucible.
- Thermal Evaporation: Higher risk of impurities due to potential reactions between the material and the crucible during heating.
-
Application Suitability:
- E-beam Evaporation: Ideal for advanced applications requiring high-purity, high-melting-point materials, such as in semiconductor manufacturing or optical coatings.
- Thermal Evaporation: More suitable for simpler applications involving low-melting-point materials, such as in basic thin film deposition or decorative coatings.
By understanding these key differences, equipment and consumable purchasers can make informed decisions based on the specific requirements of their applications, such as material type, desired coating quality, and production efficiency.
Summary Table:
Aspect | E-beam Evaporation | Thermal Evaporation |
---|---|---|
Vaporization Method | High-energy electron beam directly heats and vaporizes the material. | Electric resistance heats a crucible, which melts and evaporates the material. |
Material Compatibility | Suitable for high-melting-point materials like oxides. | Best for materials with lower melting temperatures. |
Coating Quality | Produces denser, more uniform coatings with better adhesion. | Less dense coatings; may require additional steps for quality. |
Deposition Rate | Higher deposition rate, ideal for large-scale or high-throughput applications. | Slower deposition rate, less efficient for time-sensitive processes. |
Impurity Risks | Lower risk of impurities due to direct material targeting. | Higher risk of impurities from crucible reactions. |
Application Suitability | Advanced applications like semiconductors and optical coatings. | Simpler applications like basic thin film deposition or decorative coatings. |
Need help choosing the right evaporation method for your application? Contact our experts today!