Evaporation and sputtering are both physical vapor deposition (PVD) techniques used to create thin films on substrates, but they differ fundamentally in their mechanisms, operational conditions, and applications. Evaporation relies on heating a material until it vaporizes, while sputtering uses energetic ions to knock atoms off a target material. These differences lead to variations in deposition rates, film quality, scalability, and suitability for specific applications. Below, we explore these differences in detail.
Key Points Explained:
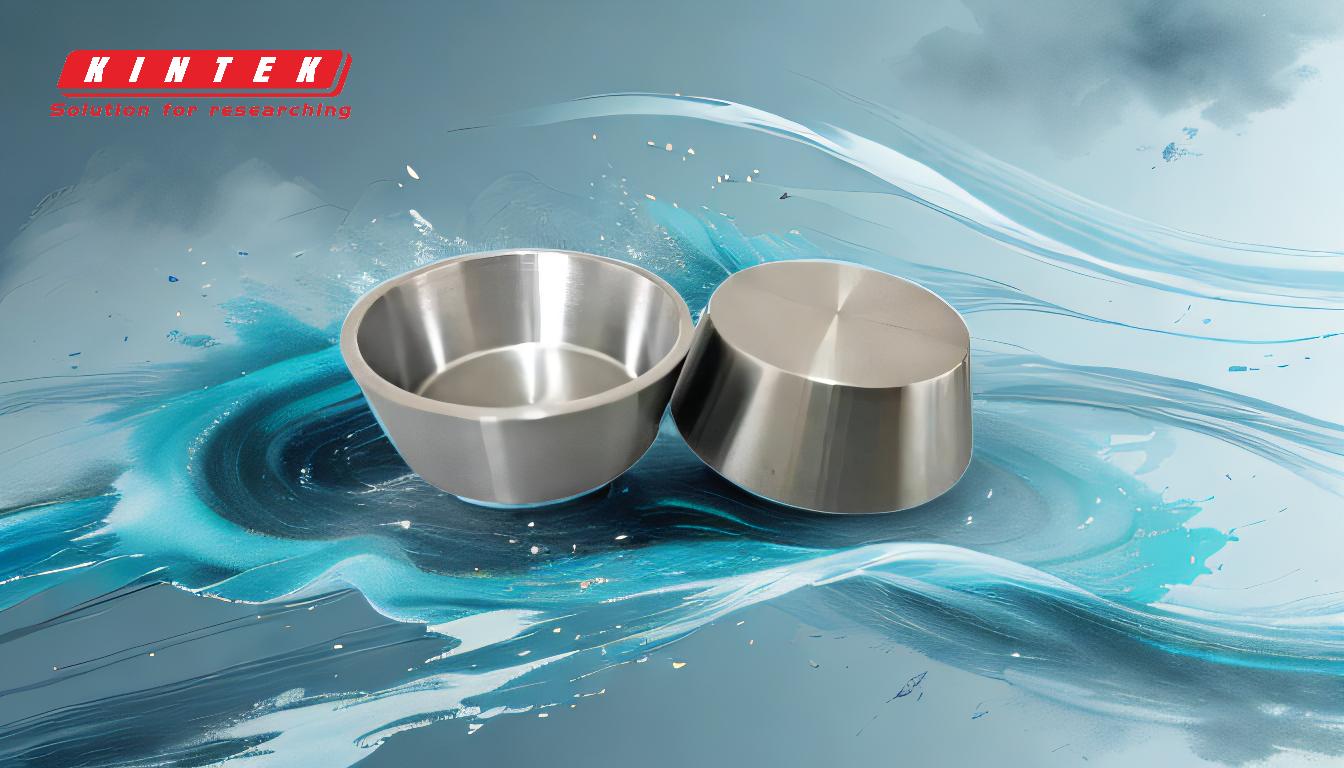
-
Mechanism of Material Vaporization:
-
Evaporation:
- Uses thermal energy (e.g., resistive heating or electron beam) to heat the source material until it reaches its vaporization temperature.
- Produces a robust vapor stream, enabling higher deposition rates.
- Operates in a high vacuum environment to minimize gas-phase collisions.
-
Sputtering:
- Involves bombarding a target material with energetic ions (usually argon) in a plasma environment.
- Ejects single atoms or small clusters from the target material.
- Operates at higher gas pressures (5-15 mTorr), where sputtered particles undergo gas-phase collisions before reaching the substrate.
-
Evaporation:
-
Deposition Rate and Efficiency:
-
Evaporation:
- Typically has a higher deposition rate compared to sputtering, especially for high-temperature materials.
- Shorter run times due to the robust vapor stream.
-
Sputtering:
- Generally has a lower deposition rate, except for pure metals.
- Slower process but offers better scalability and automation potential.
-
Evaporation:
-
Film Quality and Properties:
-
Evaporation:
- Produces films with larger grain sizes and less homogeneity.
- Lower adhesion to the substrate due to lower energy of deposited species.
- Less absorbed gas in the film, as it operates in a high vacuum.
-
Sputtering:
- Produces films with smaller grain sizes and higher homogeneity.
- Higher adhesion due to the higher energy of sputtered particles.
- More absorbed gas in the film, as it operates at higher gas pressures.
-
Evaporation:
-
Operational Conditions:
-
Evaporation:
- Requires a high vacuum environment to ensure minimal gas-phase collisions.
- Line-of-sight deposition, meaning the substrate must be directly exposed to the vapor stream.
-
Sputtering:
- Operates at lower vacuum levels (higher gas pressures).
- Deposition is less directional due to gas-phase collisions, allowing for better coverage of complex geometries.
-
Evaporation:
-
Material Versatility:
-
Evaporation:
- Suitable for materials that can withstand high temperatures without decomposing.
- Can create alloys by co-evaporating multiple materials.
-
Sputtering:
- Can deposit a wider range of materials, including those with high melting points or those that decompose upon heating.
- Sequential coatings can be performed depending on the coater's configuration.
-
Evaporation:
-
Applications:
-
Evaporation:
- Ideal for applications requiring high deposition rates and simple geometries, such as optical coatings and some semiconductor applications.
-
Sputtering:
- Better suited for applications requiring high film quality, adhesion, and coverage of complex shapes, such as microelectronics, decorative coatings, and wear-resistant coatings.
-
Evaporation:
-
Scalability and Automation:
-
Evaporation:
- Less scalable due to the need for high vacuum conditions and line-of-sight deposition.
-
Sputtering:
- Highly scalable and can be automated for large-scale production, making it suitable for industrial applications.
-
Evaporation:
In summary, while both evaporation and sputtering are effective PVD techniques, they are suited to different applications based on their mechanisms, operational conditions, and resulting film properties. Evaporation excels in high deposition rates and simplicity, while sputtering offers superior film quality, adhesion, and scalability. Understanding these differences is crucial for selecting the appropriate technique for specific thin-film deposition needs.
Summary Table:
Aspect | Evaporation | Sputtering |
---|---|---|
Mechanism | Thermal energy heats material to vaporize. | Energetic ions knock atoms off a target material. |
Deposition Rate | Higher, especially for high-temperature materials. | Lower, except for pure metals. |
Film Quality | Larger grain sizes, less homogeneity, lower adhesion. | Smaller grain sizes, higher homogeneity, better adhesion. |
Operational Conditions | High vacuum, line-of-sight deposition. | Lower vacuum, less directional deposition. |
Material Versatility | Limited to high-temperature-resistant materials. | Wider range, including high-melting-point materials. |
Applications | Optical coatings, simple geometries. | Microelectronics, complex shapes, wear-resistant coatings. |
Scalability | Less scalable due to high vacuum and line-of-sight requirements. | Highly scalable and automatable for industrial use. |
Need help choosing the right PVD technique for your application? Contact our experts today!