Flash pyrolysis and fast pyrolysis are both thermochemical processes used to decompose carbonaceous materials, but they differ in their heating rates, residence times, and product distributions. Flash pyrolysis operates at extremely rapid heating rates (100-10,000°C/s) and very short vapor residence times (less than 2 seconds), producing bio-oil and gases as primary products. In contrast, fast pyrolysis involves moderate to high heating rates, slightly longer residence times, and yields a higher proportion of bio-oil (60%) alongside biochar (20%) and syngas (20%). Flash pyrolysis is a subset of fast pyrolysis, optimized for even faster processing and specific product outputs.
Key Points Explained:
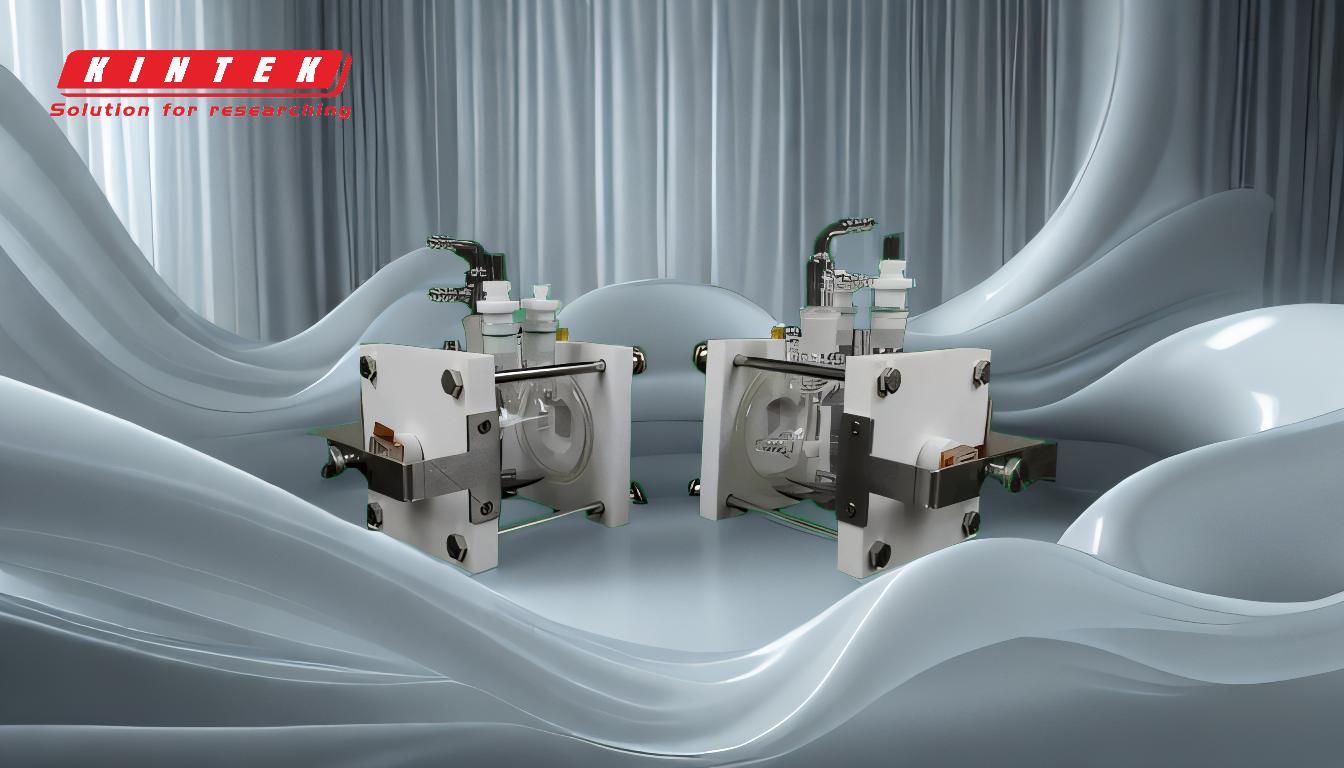
-
Heating Rates:
- Flash Pyrolysis: Operates at extremely rapid heating rates, ranging from 100 to 10,000°C per second. This rapid heating ensures quick decomposition of the feedstock.
- Fast Pyrolysis: Involves moderate to high heating rates, though not as extreme as flash pyrolysis. The heating rates are sufficient to decompose the material quickly but are generally lower than those in flash pyrolysis.
-
Residence Time:
- Flash Pyrolysis: Features very short vapor residence times, typically less than 2 seconds. This short duration minimizes secondary reactions, leading to a different product distribution.
- Fast Pyrolysis: Has slightly longer residence times compared to flash pyrolysis, though still relatively short. This allows for a more balanced production of bio-oil, biochar, and syngas.
-
Temperature Range:
- Flash Pyrolysis: Operates at moderate temperatures, generally between 400 and 600°C (752 and 1112°F). This temperature range is optimal for producing bio-oil and gases.
- Fast Pyrolysis: Also operates within a similar temperature range, typically around 500°C. The controlled temperature ensures efficient thermal decomposition and product formation.
-
Product Distribution:
- Flash Pyrolysis: Produces fewer amounts of gas and tar compared to slow pyrolysis. The primary products are bio-oil and gases, with minimal biochar.
- Fast Pyrolysis: Yields a more balanced product distribution, with approximately 60% bio-oil, 20% biochar, and 20% syngas. This makes fast pyrolysis more versatile in terms of product utilization.
-
Feedstock Preparation:
- Flash Pyrolysis: Requires finely ground feed to ensure rapid and uniform heating. The small particle size facilitates the extremely high heating rates needed.
- Fast Pyrolysis: Also requires finely ground feed, but the particle size and preparation are slightly less critical compared to flash pyrolysis due to the lower heating rates.
-
Cooling Requirements:
- Flash Pyrolysis: Requires rapid cooling of pyrolysis vapors to prevent secondary reactions and stabilize the bio-oil. This is crucial for maintaining the quality of the bio-oil.
- Fast Pyrolysis: Also involves rapid cooling, though the cooling rates may be slightly less stringent compared to flash pyrolysis due to the longer residence times.
-
Applications and Advantages:
- Flash Pyrolysis: Ideal for applications requiring high bio-oil yields and minimal gas and tar production. The process is highly efficient and suitable for large-scale industrial applications.
- Fast Pyrolysis: More versatile, producing a balanced mix of bio-oil, biochar, and syngas. This makes it suitable for a wider range of applications, including energy production and soil amendment.
By understanding these key differences, equipment and consumable purchasers can make informed decisions about which pyrolysis process best suits their needs, whether they prioritize bio-oil production, versatility, or specific product distributions.
Summary Table:
Aspect | Flash Pyrolysis | Fast Pyrolysis |
---|---|---|
Heating Rates | Extremely rapid (100-10,000°C/s) | Moderate to high (lower than flash pyrolysis) |
Residence Time | Very short (< 2 seconds) | Slightly longer than flash pyrolysis |
Temperature Range | 400-600°C (752-1112°F) | ~500°C |
Product Distribution | Bio-oil and gases (minimal biochar) | 60% bio-oil, 20% biochar, 20% syngas |
Feedstock Preparation | Finely ground feed for rapid heating | Finely ground feed, less critical than flash pyrolysis |
Cooling Requirements | Rapid cooling to stabilize bio-oil | Rapid cooling, less stringent than flash pyrolysis |
Applications | High bio-oil yield, minimal gas/tar production, large-scale industrial use | Versatile: energy production, soil amendment, and more |
Need help selecting the right pyrolysis process for your application? Contact our experts today!