Biomass can be converted into energy through various processes, with gasification and combustion being two prominent thermochemical methods. Combustion involves burning biomass in an oxygen-rich environment to produce heat, which is then used to generate electricity or for direct heating. Gasification, on the other hand, occurs in an oxygen-lean environment and produces syngas (a mixture of hydrogen, carbon monoxide, and methane) as the primary output, which can be used for electricity generation, fuel production, or chemical synthesis. The key differences lie in the oxygen levels, temperature, byproducts, and applications. Gasification is more efficient, environmentally friendly, and versatile, producing fewer pollutants and multiple valuable outputs compared to combustion.
Key Points Explained:
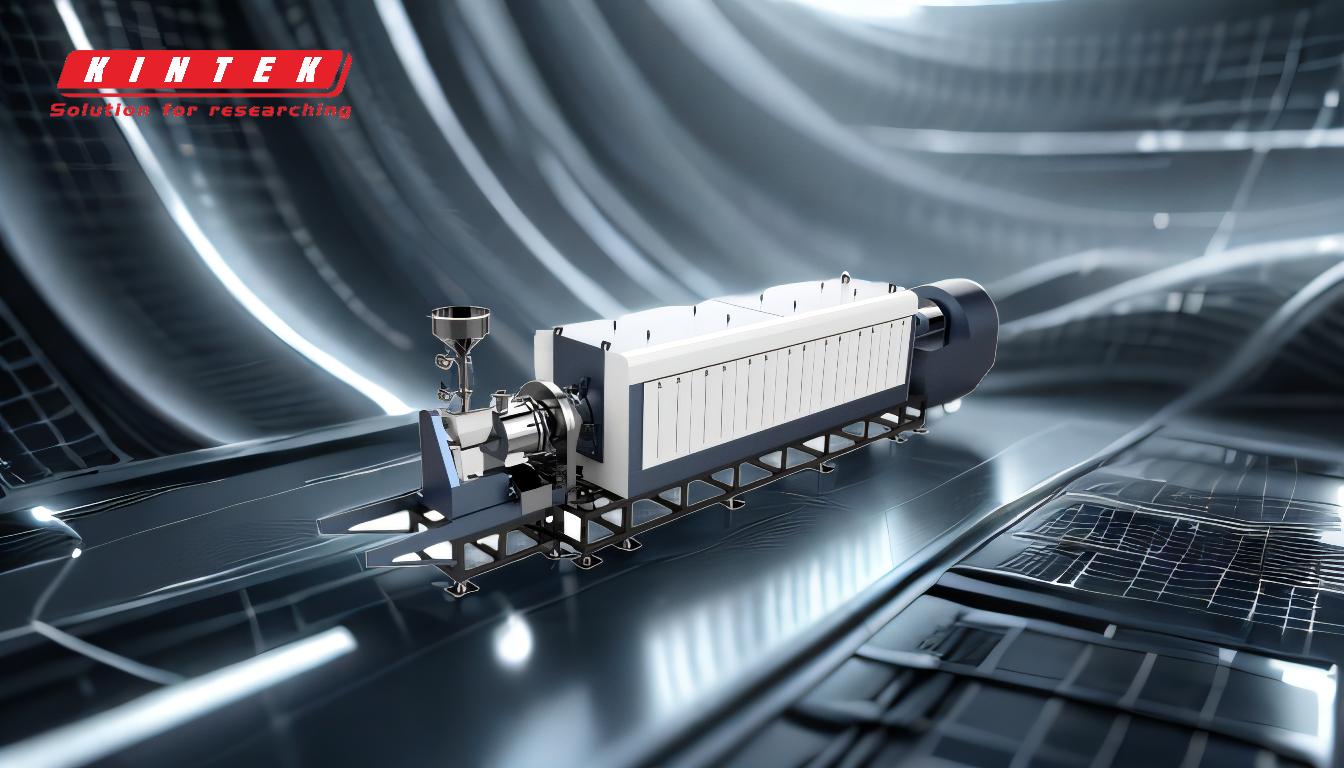
-
Definition and Process:
- Combustion: Biomass is burned in an oxygen-rich atmosphere at high temperatures (typically above 800°C). The primary goal is to release heat, which can be used directly for heating or to generate steam for electricity production.
- Gasification: Biomass is heated in an oxygen-lean or controlled oxygen environment at high temperatures (700–1000°C). The process produces syngas, a mixture of hydrogen, carbon monoxide, and methane, which can be used for electricity, fuel, or chemical synthesis.
-
Oxygen Levels:
- Combustion: Requires an oxygen-rich environment to ensure complete oxidation of biomass, resulting in the release of heat, carbon dioxide, and water vapor.
- Gasification: Operates in an oxygen-lean or controlled oxygen environment. Partial oxidation occurs, producing syngas instead of complete combustion products.
-
Temperature:
- Combustion: Typically occurs at very high temperatures (above 800°C) to ensure efficient burning and heat release.
- Gasification: Operates at slightly lower temperatures (700–1000°C) compared to combustion, as the goal is to break down biomass into syngas rather than completely oxidizing it.
-
Byproducts:
- Combustion: Produces heat, carbon dioxide, water vapor, and ash as primary byproducts. It is less efficient in terms of energy recovery and generates more pollutants.
- Gasification: Produces syngas (hydrogen, carbon monoxide, and methane), along with small amounts of tar, char, and ash. Syngas can be further processed for various applications, making gasification more versatile.
-
Environmental Impact:
- Combustion: Generates higher levels of pollutants, including particulate matter, nitrogen oxides, and sulfur oxides, due to the high-temperature burning process.
- Gasification: Produces fewer pollutants and is considered more environmentally friendly. The syngas can be cleaned and used efficiently, reducing emissions compared to direct combustion.
-
Applications:
- Combustion: Primarily used for direct heat generation or electricity production through steam turbines. It is commonly employed in large-scale power plants and industrial heating systems.
- Gasification: Syngas can be used for electricity generation, fuel production (e.g., synthetic natural gas, biofuels), and chemical synthesis (e.g., methanol, ammonia). It is more versatile and economically beneficial due to the multiple valuable outputs.
-
Efficiency and Economic Benefits:
- Combustion: Less efficient in terms of energy recovery, as a significant portion of energy is lost as heat. It is also less economically beneficial due to limited byproduct utilization.
- Gasification: More efficient and economically viable, as it produces multiple valuable products (syngas, biochar, and tar) that can be used in various industries. It also operates at lower temperatures, reducing energy consumption.
-
Technological Complexity:
- Combustion: Relatively simple and well-established technology, widely used for large-scale energy production.
- Gasification: More complex and requires advanced technology to control oxygen levels, temperature, and syngas composition. It is a refined application compared to combustion.
In summary, while both gasification and combustion are methods of converting biomass into energy, they differ significantly in terms of process conditions, byproducts, environmental impact, and applications. Gasification offers greater efficiency, versatility, and environmental benefits, making it a more advanced and sustainable option compared to traditional combustion.
Summary Table:
Aspect | Combustion | Gasification |
---|---|---|
Oxygen Levels | Oxygen-rich environment | Oxygen-lean or controlled oxygen environment |
Temperature | Above 800°C | 700–1000°C |
Byproducts | Heat, CO₂, water vapor, ash | Syngas (H₂, CO, CH₄), tar, char, ash |
Environmental Impact | Higher pollutants (particulate matter, NOₓ, SOₓ) | Fewer pollutants, cleaner process |
Applications | Direct heat, electricity via steam turbines | Electricity, fuel production, chemical synthesis |
Efficiency | Less efficient, significant energy loss as heat | More efficient, multiple valuable outputs |
Complexity | Simple and well-established | Advanced technology, requires precise control |
Discover how biomass gasification can transform your energy systems—contact us today!