Gold-plated and gold PVD (Physical Vapor Deposition) are two distinct methods of applying a gold layer to a base material, each with unique processes, advantages, and limitations. Gold plating involves using an electrolyte solution and electrical current to deposit a thin layer of gold onto a substrate, offering better coating uniformity and flexibility in thickness. In contrast, PVD is a high-temperature process that transitions gold from a vapor phase to a solid film, providing superior durability, corrosion resistance, and compatibility with materials like titanium and stainless steel. While gold plating is more cost-effective and versatile, PVD coatings are more durable and long-lasting, making them suitable for high-wear applications.
Key Points Explained:
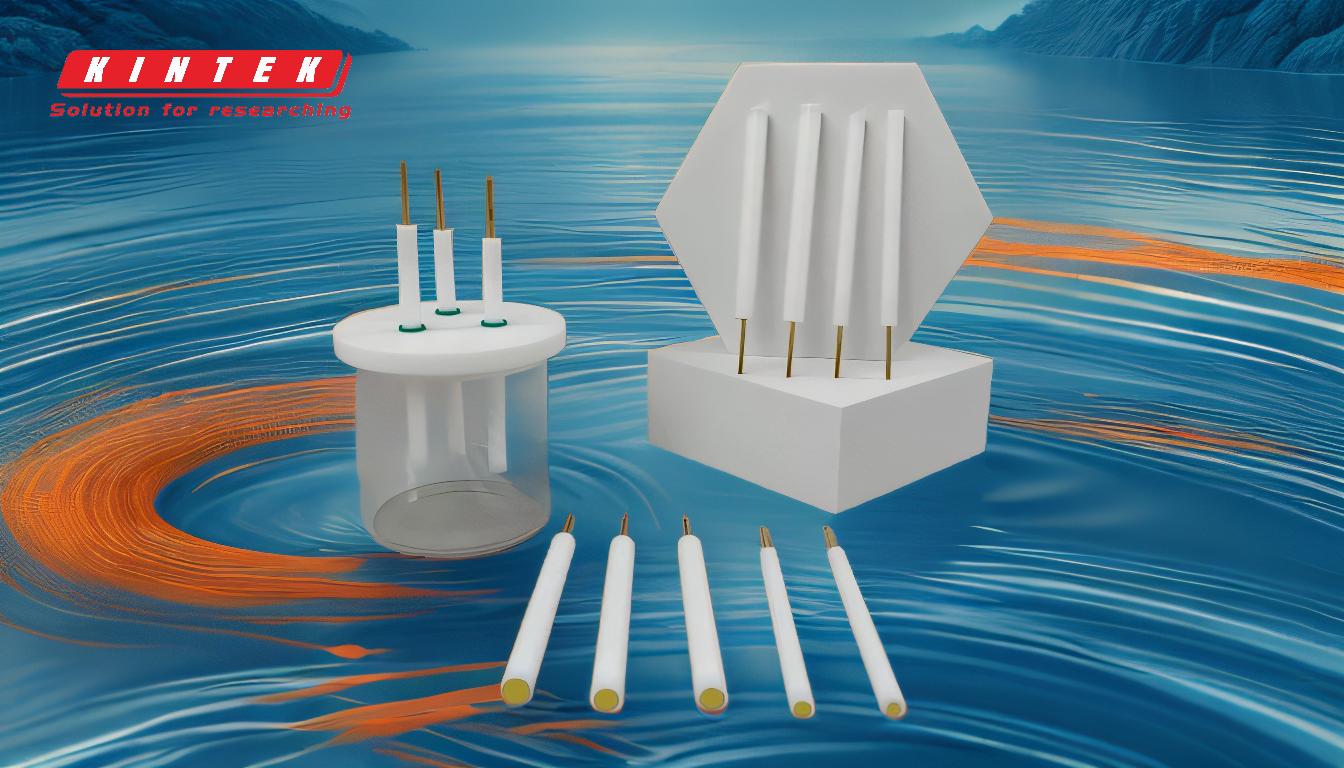
-
Process Differences:
-
Gold Plating:
- Uses an electrolyte solution and electrical current to deposit gold onto a substrate.
- The process is electrochemical, allowing for precise control over coating thickness and uniformity.
- Suitable for covering recessed areas and complex geometries due to its ability to flow into tight spaces.
-
Gold PVD:
- Involves blasting gold onto a base metal at high temperatures, transitioning from a vapor phase to a solid film.
- A high-temperature, vacuum-based process that creates a thin, durable layer of gold.
- Compatible with materials like titanium and stainless steel, which are often challenging to plate.
-
Gold Plating:
-
Durability and Longevity:
-
Gold Plating:
- Typically lasts about 1 year with everyday wear.
- Less resistant to scratches and corrosion, which can expose the base material over time.
-
Gold PVD:
- Can last 3 years or more with regular use.
- Offers superior scratch and corrosion resistance due to the denser and more adherent nature of the PVD coating.
-
Gold Plating:
-
Coating Uniformity and Flexibility:
-
Gold Plating:
- Provides better coating uniformity, especially in recessed or intricate areas.
- Allows for varied thicknesses, making it suitable for applications requiring specific aesthetic or functional properties.
-
Gold PVD:
- While less uniform in complex geometries, it provides a consistent and durable coating on flat or simple surfaces.
- Limited flexibility in achieving varied thicknesses compared to gold plating.
-
Gold Plating:
-
Energy Consumption and Cost:
-
Gold Plating:
- Lower energy consumption compared to PVD, as it does not require high temperatures.
- Generally more cost-effective, making it a popular choice for decorative and low-wear applications.
-
Gold PVD:
- Requires high temperatures and specialized equipment, leading to higher energy consumption and costs.
- More expensive due to the advanced technology and materials involved, but justified by its durability and performance.
-
Gold Plating:
-
Material Compatibility:
-
Gold Plating:
- Works well with a wide range of materials, including metals like brass, copper, and nickel.
- Limited compatibility with materials like titanium and stainless steel, which are harder to plate.
-
Gold PVD:
- Ideal for materials like titanium and stainless steel, which are often used in high-performance or industrial applications.
- Less versatile in terms of material compatibility compared to gold plating.
-
Gold Plating:
-
Applications and Use Cases:
-
Gold Plating:
- Commonly used in jewelry, decorative items, and electronics where cost and aesthetics are prioritized over durability.
- Suitable for applications requiring intricate designs or selective plating.
-
Gold PVD:
- Preferred for high-wear applications such as watch components, medical devices, and industrial tools where durability and resistance to wear are critical.
- Ideal for products exposed to harsh environments or requiring long-term performance.
-
Gold Plating:
By understanding these key differences, purchasers can make informed decisions based on the specific requirements of their application, balancing factors like cost, durability, and material compatibility.
Summary Table:
Aspect | Gold Plating | Gold PVD |
---|---|---|
Process | Electrochemical deposition using an electrolyte solution and electrical current. | High-temperature, vacuum-based process transitioning gold from vapor to solid. |
Durability | Lasts ~1 year with everyday wear; less resistant to scratches and corrosion. | Lasts 3+ years; superior scratch and corrosion resistance. |
Coating Uniformity | Better for recessed or intricate areas; allows varied thicknesses. | Less uniform in complex geometries; consistent on flat surfaces. |
Cost & Energy Use | Lower cost and energy consumption; ideal for decorative applications. | Higher cost and energy use; justified by durability and performance. |
Material Compatibility | Works with brass, copper, nickel; limited for titanium and stainless steel. | Ideal for titanium and stainless steel; less versatile for other materials. |
Applications | Jewelry, decorative items, electronics; suitable for intricate designs. | High-wear applications like watches, medical devices, and industrial tools. |
Still unsure which coating method is right for you? Contact our experts today for personalized advice!