HIP (Hot Isostatic Pressing) and CIP (Cold Isostatic Pressing) are both advanced manufacturing techniques used to densify materials, but they differ significantly in their processes, applications, and outcomes. HIP involves applying high temperature and pressure simultaneously to eliminate porosity and improve material properties, making it ideal for high-performance applications like aerospace and medical implants. CIP, on the other hand, uses only high pressure at room temperature, making it suitable for shaping and compacting materials like ceramics and metals before further processing. While HIP achieves near-theoretical density and enhances mechanical properties, CIP is primarily used for initial compaction and shaping.
Key Points Explained:
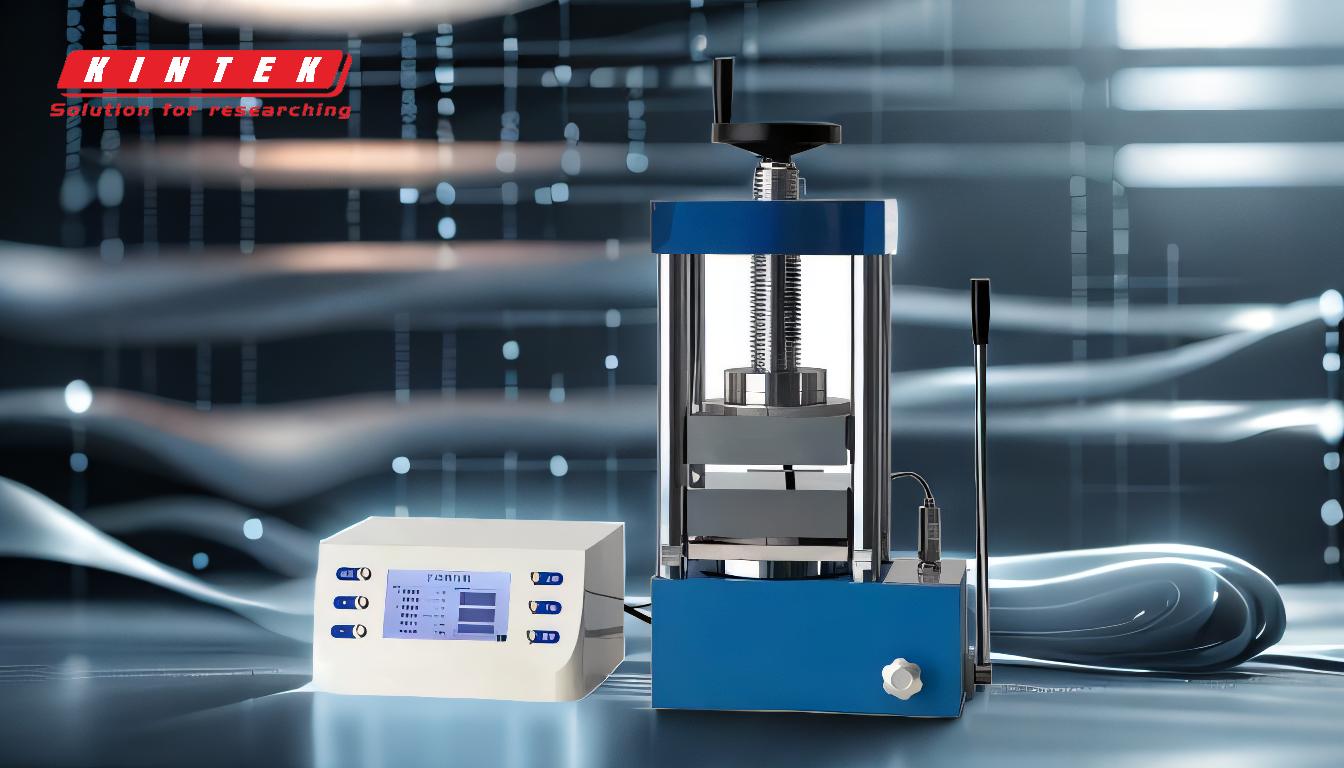
-
Process Differences:
- HIP: Combines high temperature (up to 2000°C) and high pressure (up to 200 MPa) in an inert gas environment to densify materials. This dual action eliminates internal voids and improves material properties.
- CIP: Uses high pressure (up to 600 MPa) at room temperature to compact materials uniformly. It does not involve heating, making it a simpler and more cost-effective process.
-
Applications:
- HIP: Commonly used in industries requiring high-performance materials, such as aerospace (turbine blades), medical (implants), and automotive (engine components). It is ideal for materials that need superior mechanical properties and near-theoretical density.
- CIP: Often used for shaping and compacting powders into near-net shapes, particularly in ceramics, metals, and composites. It is a precursor to sintering or other high-temperature processes.
-
Material Outcomes:
- HIP: Produces materials with enhanced mechanical properties, such as increased strength, fatigue resistance, and fracture toughness. It achieves near-theoretical density, making it suitable for critical applications.
- CIP: Results in uniformly compacted materials with good green strength, but further processing (e.g., sintering) is required to achieve full density and mechanical properties.
-
Equipment and Cost:
- HIP: Requires specialized equipment capable of withstanding extreme temperatures and pressures, making it more expensive and complex.
- CIP: Uses simpler equipment that operates at room temperature, resulting in lower costs and easier maintenance.
-
Advantages and Limitations:
- HIP: Offers superior material properties but is limited by higher costs and longer processing times. It is not suitable for all materials, especially those sensitive to high temperatures.
- CIP: Provides cost-effective and uniform compaction but cannot achieve the same level of densification or mechanical improvements as HIP.
By understanding these key differences, purchasers can choose the appropriate method based on their material requirements, application needs, and budget constraints.
Summary Table:
Aspect | HIP (Hot Isostatic Pressing) | CIP (Cold Isostatic Pressing) |
---|---|---|
Process | High temperature (up to 2000°C) and pressure (up to 200 MPa) in an inert gas environment. | High pressure (up to 600 MPa) at room temperature, no heating involved. |
Applications | Aerospace, medical implants, automotive (high-performance materials). | Shaping and compacting ceramics, metals, and composites before further processing. |
Material Outcomes | Near-theoretical density, enhanced mechanical properties (strength, fatigue resistance). | Uniform compaction, good green strength; requires sintering for full density. |
Equipment and Cost | Specialized, expensive equipment for extreme conditions. | Simpler, cost-effective equipment operating at room temperature. |
Advantages | Superior material properties, ideal for critical applications. | Cost-effective, uniform compaction, suitable for initial shaping. |
Limitations | Higher costs, longer processing times, not suitable for heat-sensitive materials. | Cannot achieve the same densification or mechanical improvements as HIP. |
Need help choosing between HIP and CIP? Contact our experts today for tailored advice!