Ion nitriding and gas nitriding are both surface hardening processes used to improve the wear resistance, fatigue strength, and hardness of metal components. However, they differ significantly in terms of process mechanics, efficiency, cost, and the quality of the nitrided layer. Ion nitriding, also known as glow ion nitriding, is a more advanced and modern technique that offers faster processing times, lower operating costs, and superior nitrided layer quality compared to gas nitriding. It utilizes a high-pressure electric field to accelerate nitrogen diffusion, resulting in a controlled and high-quality surface layer. Gas nitriding, on the other hand, relies on a chemical reaction between ammonia gas and the metal surface, which is slower and less efficient. While ion nitriding requires a higher initial investment, its operational advantages and superior results make it a preferred choice for many applications.
Key Points Explained:
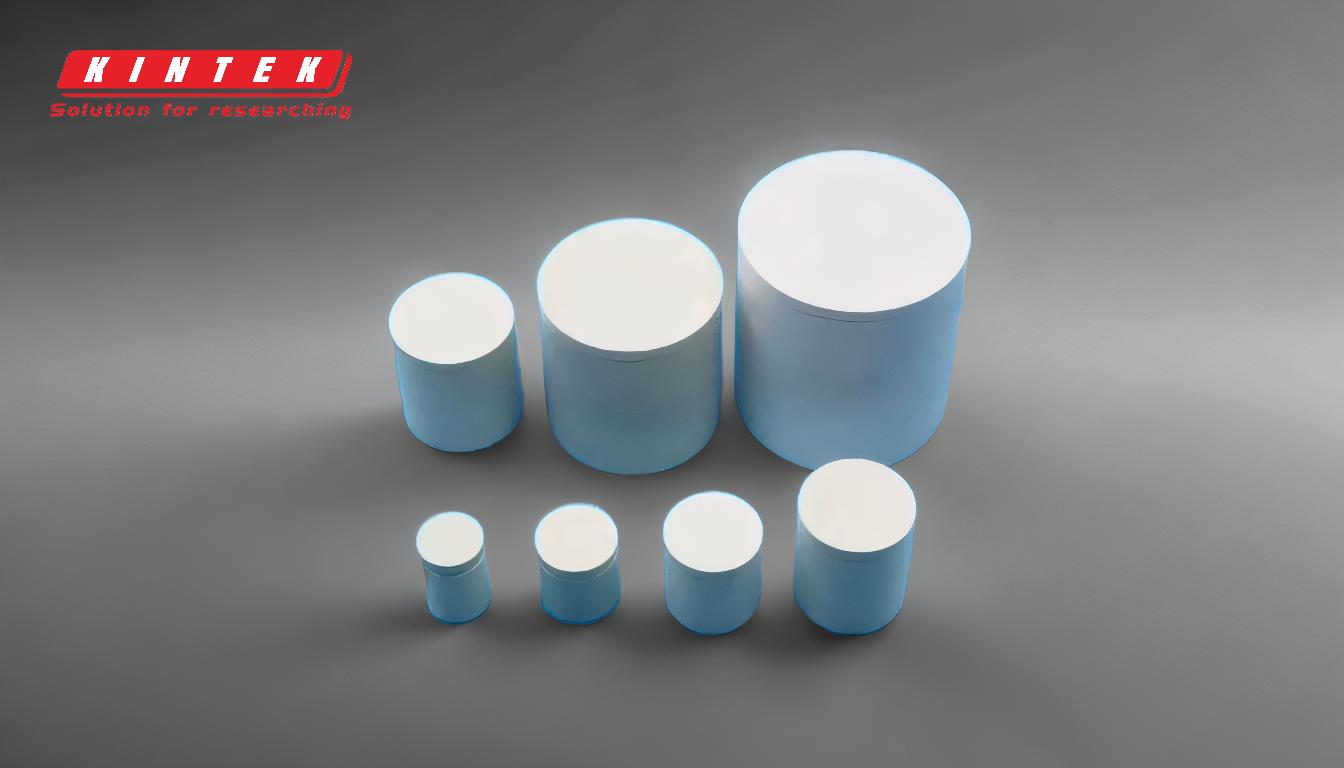
-
Process Mechanics:
- Ion Nitriding: This process involves placing the metal parts in a vacuum chamber where a high-voltage electric field creates a plasma of ionized nitrogen gas. The nitrogen ions are accelerated toward the metal surface, where they diffuse into the material, forming a hard nitride layer. This method allows for precise control over the nitriding process and the properties of the resulting layer.
- Gas Nitriding: In this process, the metal parts are heated in an atmosphere of ammonia gas. The ammonia decomposes at the metal surface, releasing nitrogen atoms that diffuse into the material. This method is slower and less controllable compared to ion nitriding.
-
Processing Time:
- Ion Nitriding: The nitriding process is significantly faster, typically taking 3-10 hours. This is due to the rapid diffusion of nitrogen atoms under the influence of the high-pressure electric field.
- Gas Nitriding: The process is slower, often requiring longer times to achieve a comparable nitrided layer.
-
Operating Costs:
- Ion Nitriding: Operating costs are about 60% of those for gas nitriding. This is due to the faster processing times and lower energy consumption.
- Gas Nitriding: Higher operating costs are associated with longer processing times and higher energy consumption.
-
Quality of Nitrided Layer:
- Ion Nitriding: Produces a nitrided layer with high toughness, fatigue resistance, and wear resistance. The brittle white cement phase (Fe2N) is controlled within 0-0.2 mm, eliminating the need for grinding. Surface hardness can reach HV900 (HRC64), and the nitrided layer depth can be controlled between 0.09-0.87 mm.
- Gas Nitriding: While it can produce a hard surface layer, the quality is generally inferior to that achieved with ion nitriding. The process is less controllable, leading to variations in layer thickness and properties.
-
Part Deformation:
- Ion Nitriding: Reduces part deformation due to rapid surface heating and cooling, which keeps the rest of the part at a low temperature (100°C). This minimizes thermal stress and distortion.
- Gas Nitriding: Higher risk of part deformation due to slower heating and cooling rates, which can lead to greater thermal stress and distortion.
-
Initial Investment:
- Ion Nitriding: Requires a higher initial investment. For example, a 400 kg capacity ion nitriding furnace costs around 900,000 yuan.
- Gas Nitriding: Lower initial investment, with a similar capacity furnace costing approximately 40,000 yuan.
-
Environmental and Energy Efficiency:
- Ion Nitriding: More environmentally friendly and energy-efficient due to shorter processing times and lower energy consumption.
- Gas Nitriding: Less energy-efficient and can produce more waste gases, making it less environmentally friendly.
In summary, while ion nitriding involves a higher initial investment, its advantages in terms of processing speed, operating costs, and the quality of the nitrided layer make it a superior choice for many applications. Gas nitriding, while less expensive initially, is slower, less efficient, and produces a lower-quality nitrided layer.
Summary Table:
Aspect | Ion Nitriding | Gas Nitriding |
---|---|---|
Process Mechanics | Uses a high-voltage electric field to create plasma for nitrogen diffusion. | Relies on ammonia gas decomposition for nitrogen diffusion. |
Processing Time | 3-10 hours (faster due to rapid diffusion). | Slower, often requiring longer times for comparable results. |
Operating Costs | ~60% of gas nitriding costs (lower energy consumption, faster processing). | Higher due to longer processing times and energy use. |
Nitrided Layer Quality | High toughness, fatigue resistance, and wear resistance. Controlled layer depth. | Inferior quality with less control over layer thickness and properties. |
Part Deformation | Minimal due to rapid surface heating and cooling. | Higher risk due to slower heating/cooling rates. |
Initial Investment | Higher (e.g., 900,000 yuan for a 400 kg furnace). | Lower (e.g., 40,000 yuan for a similar capacity furnace). |
Environmental Impact | More energy-efficient and environmentally friendly. | Less efficient, produces more waste gases. |
Want to enhance your metal components' performance? Contact us today to learn more about ion nitriding!