Microwave pyrolysis and conventional pyrolysis are two distinct methods of thermal decomposition used to break down materials, particularly plastics, into smaller molecules. The primary difference lies in the mechanism of heat transfer and the resulting efficiency, environmental impact, and product quality. Microwave pyrolysis uses electromagnetic waves to generate heat internally within the material, leading to faster and more uniform heating. In contrast, conventional pyrolysis relies on external heat sources, which can result in uneven heating and slower reaction times. Additionally, microwave pyrolysis tends to produce fewer harmful byproducts, making it a more environmentally friendly option.
Key Points Explained:
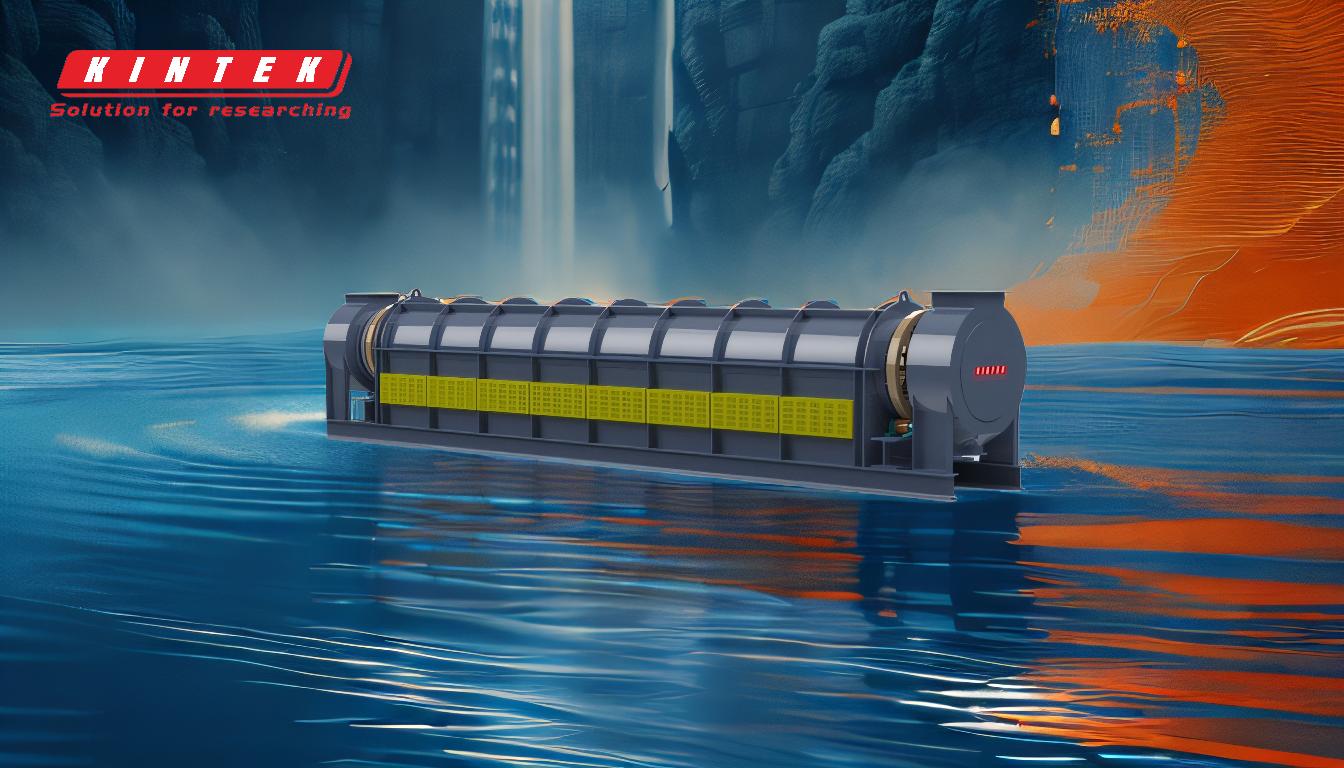
-
Mechanism of Heat Transfer:
- Microwave Pyrolysis: Utilizes microwave radiation to directly excite the molecules within the material, causing them to vibrate and generate heat internally. This leads to rapid and uniform heating throughout the material.
- Conventional Pyrolysis: Relies on external heat sources, such as burners or electric heaters, to transfer heat from the outside to the inside of the material. This can result in uneven heating, with the outer layers heating faster than the inner layers.
-
Heating Efficiency:
- Microwave Pyrolysis: Offers higher heating efficiency due to the direct interaction of microwaves with the material. This results in faster reaction times and lower energy consumption.
- Conventional Pyrolysis: Typically less efficient because heat must travel through the material from the outside, which can lead to energy losses and longer processing times.
-
Environmental Impact:
- Microwave Pyrolysis: Generally produces fewer harmful byproducts, such as nitrogen oxides and sulfur dioxide, because the process is more controlled and occurs at lower temperatures. This makes it a more environmentally friendly option.
- Conventional Pyrolysis: Often emits more toxic gases due to the higher temperatures and less controlled conditions, which can lead to the formation of pollutants.
-
Product Quality:
- Microwave Pyrolysis: Tends to yield higher-quality products with more consistent properties due to the uniform heating and controlled conditions.
- Conventional Pyrolysis: May result in products with varying quality due to uneven heating and less controlled reaction conditions.
-
Applications:
- Microwave Pyrolysis: Suitable for applications requiring rapid and uniform heating, such as in the processing of plastics and biomass. It is also preferred in situations where environmental impact is a concern.
- Conventional Pyrolysis: Commonly used in industrial settings where large-scale processing is required, and the environmental impact is less of a concern.
In summary, microwave pyrolysis offers several advantages over conventional pyrolysis, including higher heating efficiency, better environmental performance, and superior product quality. However, the choice between the two methods depends on the specific requirements of the application, such as the scale of processing and the importance of environmental considerations.
Summary Table:
Aspect | Microwave Pyrolysis | Conventional Pyrolysis |
---|---|---|
Heat Transfer | Internal heating via microwave radiation, ensuring uniform and rapid heating. | External heating via burners or electric heaters, leading to uneven heating. |
Heating Efficiency | Higher efficiency due to direct molecular excitation, faster reactions, and lower energy use. | Less efficient due to heat transfer losses and longer processing times. |
Environmental Impact | Fewer harmful byproducts, more controlled process, and lower pollutant emissions. | More toxic gases emitted due to higher temperatures and less controlled conditions. |
Product Quality | Higher-quality, consistent products due to uniform heating and controlled conditions. | Varying product quality due to uneven heating and less controlled reaction conditions. |
Applications | Ideal for plastics, biomass, and eco-friendly processes requiring rapid heating. | Suitable for large-scale industrial processes where environmental impact is less critical. |
Want to learn more about pyrolysis methods and their applications? Contact our experts today for tailored solutions!