Powder metallurgy and sintering are closely related processes, but they are not the same. Powder metallurgy is a broader manufacturing technique that involves creating metal parts from powdered materials, while sintering is a specific step within the powder metallurgy process. Powder metallurgy includes multiple stages, such as powder blending, compaction, and sintering, to produce complex metal components. Sintering, on the other hand, is the process of heating compacted metal powders to bond the particles together without melting them, enhancing the part's strength and hardness. Understanding the distinction between these two concepts is crucial for selecting the right manufacturing method for specific applications, such as automotive parts or cutting tools.
Key Points Explained:
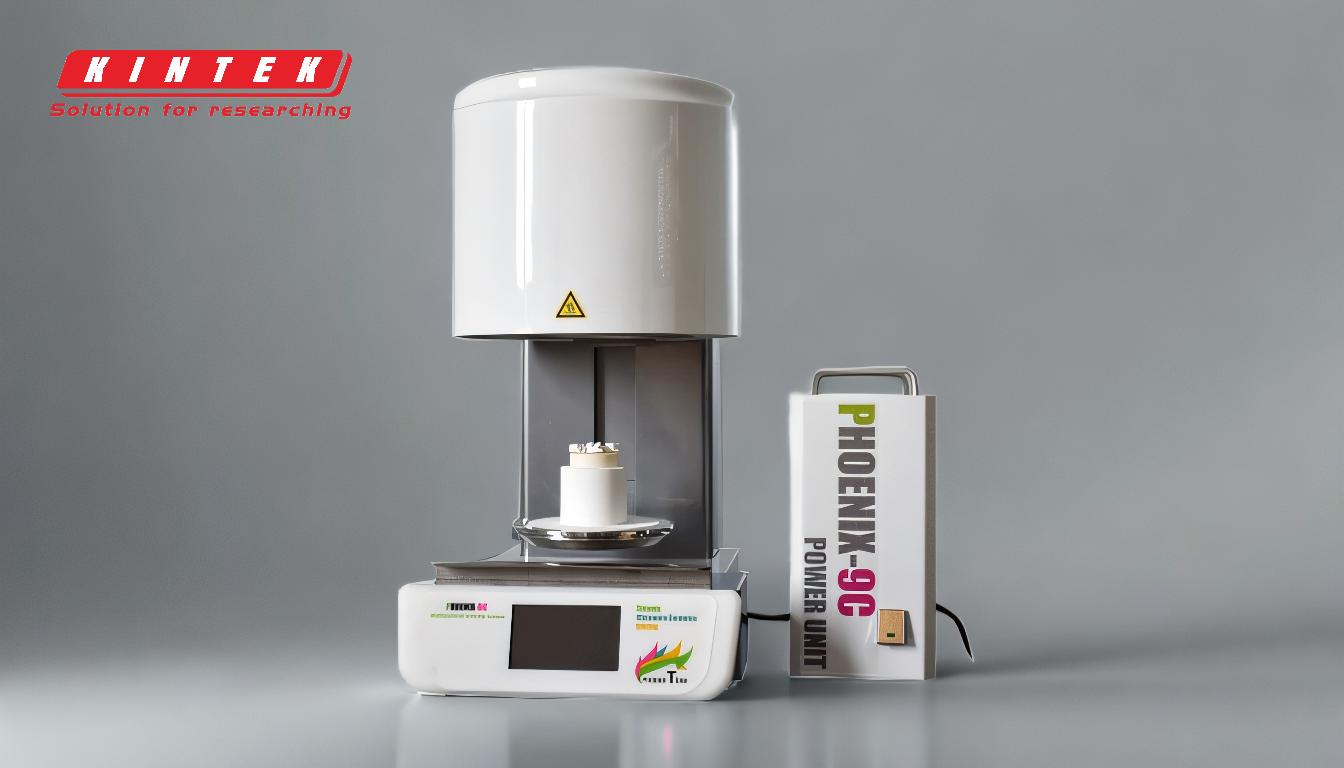
-
Definition of Powder Metallurgy:
- Powder metallurgy is a manufacturing process that involves creating metal parts from powdered materials. It encompasses several steps, including powder blending, compaction, and sintering.
- This method is widely used to produce intricate parts with complex shapes, especially in industries like automotive manufacturing, where components such as gears, camshafts, and valve seats are commonly made using this technique.
-
Definition of Sintering:
- Sintering is a specific step within the powder metallurgy process. It involves heating compacted metal powders to a temperature just below their melting point. This heating causes the metal particles to bond together, enhancing the part's strength and hardness.
- Sintering is performed under controlled atmospheric conditions to prevent oxidation and ensure the desired material properties are achieved.
-
Steps in Powder Metallurgy:
- Powder Blending: The first step involves selecting and mixing metal powders, which may include metals like iron, nickel, molybdenum, or copper, along with lubricants to facilitate the compaction process.
- Compaction: The blended powder is then pressed into a specific shape using a die press. This step is typically performed at room temperature and results in a "green" part with initial strength.
- Sintering: The compacted powder is heated in a furnace to bond the particles together, forming a solid piece. This step is crucial for achieving the final strength and hardness of the part.
- Post-Treatment: After sintering, additional processes such as machining, heat treatment, or surface finishing may be applied to achieve the desired properties and dimensions.
-
Steps in Sintering:
- Heating: The compacted metal powder is heated to a temperature just below its melting point. This causes the particles to bond together through diffusion, resulting in a denser and stronger material.
- Controlled Atmosphere: Sintering is often performed in a controlled atmosphere, such as a vacuum or inert gas, to prevent oxidation and ensure the desired material properties are achieved.
- Cooling: After sintering, the part is cooled gradually to room temperature to prevent cracking or warping.
-
Applications of Powder Metallurgy and Sintering:
- Automotive Industry: Powder metallurgy is commonly used to produce components like gears, camshafts, and valve seats due to its ability to create complex shapes with high precision.
- Cutting Tools: Sintered materials are often used in the manufacturing of cutting tools because of their high strength and wear resistance.
- Sintered Filters: Sintering is also used to produce porous metal filters, which are used in various industrial applications.
-
Advantages of Powder Metallurgy and Sintering:
- Complex Shapes: Powder metallurgy allows for the production of parts with complex geometries that would be difficult or impossible to achieve with traditional manufacturing methods.
- Material Efficiency: The process is highly material-efficient, as it minimizes waste by using only the amount of powder needed to create the part.
- Cost-Effective: Powder metallurgy can be more cost-effective than other manufacturing methods, especially for high-volume production runs.
-
Key Differences:
- Scope: Powder metallurgy is a broader manufacturing process that includes multiple steps, while sintering is a specific step within that process.
- Purpose: The purpose of powder metallurgy is to create metal parts from powdered materials, whereas the purpose of sintering is to bond the metal particles together to enhance the part's strength and hardness.
- Process: Powder metallurgy involves steps like powder blending, compaction, and sintering, while sintering focuses solely on the heating and bonding of the compacted powder.
In summary, while sintering is an essential part of the powder metallurgy process, powder metallurgy itself encompasses a wider range of techniques and steps to produce metal components. Understanding the distinction between these two concepts is important for selecting the appropriate manufacturing method for specific applications.
Summary Table:
Aspect | Powder Metallurgy | Sintering |
---|---|---|
Definition | A manufacturing process creating metal parts from powdered materials. | A specific step in powder metallurgy where compacted powders are heated to bond particles. |
Scope | Broader process including powder blending, compaction, sintering, and post-treatment. | Focused solely on heating and bonding compacted powders. |
Purpose | To create metal parts from powdered materials. | To bond metal particles for enhanced strength and hardness. |
Applications | Automotive parts (gears, camshafts), cutting tools, and sintered filters. | Used within powder metallurgy to strengthen parts. |
Advantages | Produces complex shapes, material-efficient, and cost-effective for high volumes. | Enhances part strength and hardness without melting. |
Need help choosing the right manufacturing process for your application? Contact our experts today!