PVD (Physical Vapor Deposition) and CVD (Chemical Vapor Deposition) are two widely used techniques for depositing thin films onto substrates, but they differ significantly in their processes, operating conditions, and resulting coating properties. PVD involves the physical vaporization of solid materials, typically in a vacuum, and deposits them onto a substrate at lower temperatures (250°C~500°C). In contrast, CVD relies on chemical reactions between gaseous precursors and the substrate at higher temperatures (450°C~1050°C). These differences lead to variations in coating thickness, uniformity, stress, and application suitability. PVD is often preferred for its ability to deposit a broader range of materials, including metals and ceramics, while CVD excels in producing denser, more uniform coatings, particularly for ceramics and polymers. The choice between PVD and CVD depends on factors such as the desired coating properties, substrate material, and application requirements.
Key Points Explained:
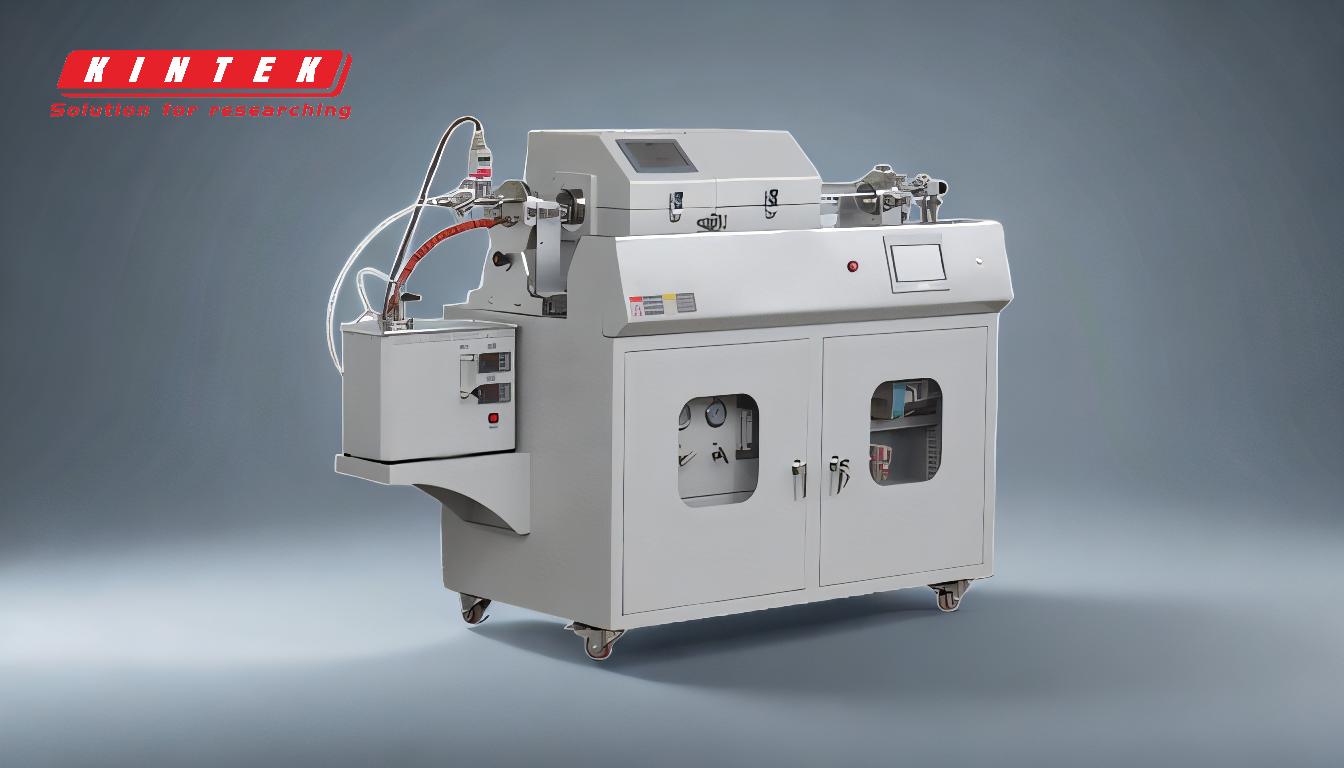
-
Deposition Mechanism:
- PVD: Involves the physical vaporization of solid materials (e.g., metals, alloys, or ceramics) through processes like sputtering or evaporation. The vaporized atoms then deposit onto the substrate in a line-of-sight manner.
- CVD: Relies on chemical reactions between gaseous precursors and the substrate. The gaseous molecules react on the substrate surface, forming a solid coating through a multidirectional deposition process.
-
Operating Temperature:
- PVD: Operates at relatively lower temperatures, typically between 250°C and 500°C. This makes it suitable for temperature-sensitive substrates.
- CVD: Requires higher temperatures, ranging from 450°C to 1050°C, which can limit its use with certain materials but enables the formation of denser coatings.
-
Coating Thickness and Uniformity:
- PVD: Produces thinner coatings (3~5μm) that are less dense and less uniform compared to CVD. The process is faster but may result in compressive stress during cooling.
- CVD: Yields thicker coatings (10~20μm) that are denser and more uniform. However, the high processing temperature can introduce tensile stress and fine cracks.
-
Coating Materials:
- PVD: Can deposit a broader range of materials, including metals, alloys, and ceramics. This versatility makes it suitable for applications requiring diverse material properties.
- CVD: Primarily limited to ceramics and polymers, making it ideal for applications requiring high chemical stability and thermal resistance.
-
Coating Coverage:
- PVD: Line-of-sight deposition means it is less effective for coating complex geometries or hidden surfaces.
- CVD: Multidirectional deposition allows for better coverage of complex shapes and hidden areas, making it more versatile for intricate components.
-
Applications:
- PVD: Commonly used in industries requiring wear-resistant, corrosion-resistant, or decorative coatings, such as cutting tools, medical devices, and consumer electronics.
- CVD: Preferred for applications demanding high-performance coatings, such as semiconductor manufacturing, aerospace components, and high-temperature environments.
-
Advantages and Disadvantages:
-
PVD Advantages:
- Lower operating temperatures.
- Faster deposition rates.
- Ability to deposit a wide range of materials.
-
PVD Disadvantages:
- Less uniform coatings.
- Limited coverage for complex geometries.
-
CVD Advantages:
- Denser and more uniform coatings.
- Better coverage for complex shapes.
-
CVD Disadvantages:
- Higher operating temperatures.
- Longer deposition times.
-
PVD Advantages:
In summary, the choice between PVD and CVD depends on the specific requirements of the application, including the desired coating properties, substrate material, and operating conditions. PVD is ideal for applications requiring versatility and lower temperatures, while CVD is better suited for high-performance coatings on complex geometries.
Summary Table:
Aspect | PVD | CVD |
---|---|---|
Deposition Mechanism | Physical vaporization of solid materials (e.g., sputtering, evaporation). | Chemical reactions between gaseous precursors and the substrate. |
Operating Temperature | 250°C~500°C (lower, suitable for sensitive substrates). | 450°C~1050°C (higher, enables denser coatings). |
Coating Thickness | Thinner (3~5μm), less dense, and less uniform. | Thicker (10~20μm), denser, and more uniform. |
Coating Materials | Metals, alloys, and ceramics (broader range). | Primarily ceramics and polymers (limited range). |
Coating Coverage | Line-of-sight, less effective for complex geometries. | Multidirectional, better coverage for complex shapes. |
Applications | Wear-resistant, corrosion-resistant, decorative coatings. | High-performance coatings (e.g., semiconductors, aerospace). |
Advantages | Lower temperatures, faster deposition, versatile material options. | Denser coatings, uniform coverage, ideal for complex geometries. |
Disadvantages | Less uniform coatings, limited coverage for complex shapes. | Higher temperatures, longer deposition times. |
Need help choosing between PVD and CVD for your application? Contact our experts today!