PVD (Physical Vapor Deposition) and DLC (Diamond-Like Carbon) are both advanced coating technologies used to enhance the surface properties of materials, but they differ significantly in their processes, properties, and applications. PVD is a broad category of coating techniques that involve the physical transfer of material from a source to a substrate, often resulting in coatings with high purity, uniformity, and excellent adhesion. DLC, on the other hand, is a specific type of coating that mimics some properties of diamond, such as hardness and wear resistance, but is typically applied using PVD or CVD (Chemical Vapor Deposition) methods. The choice between PVD and DLC depends on the specific requirements of the application, including factors like wear resistance, temperature tolerance, and substrate compatibility.
Key Points Explained:
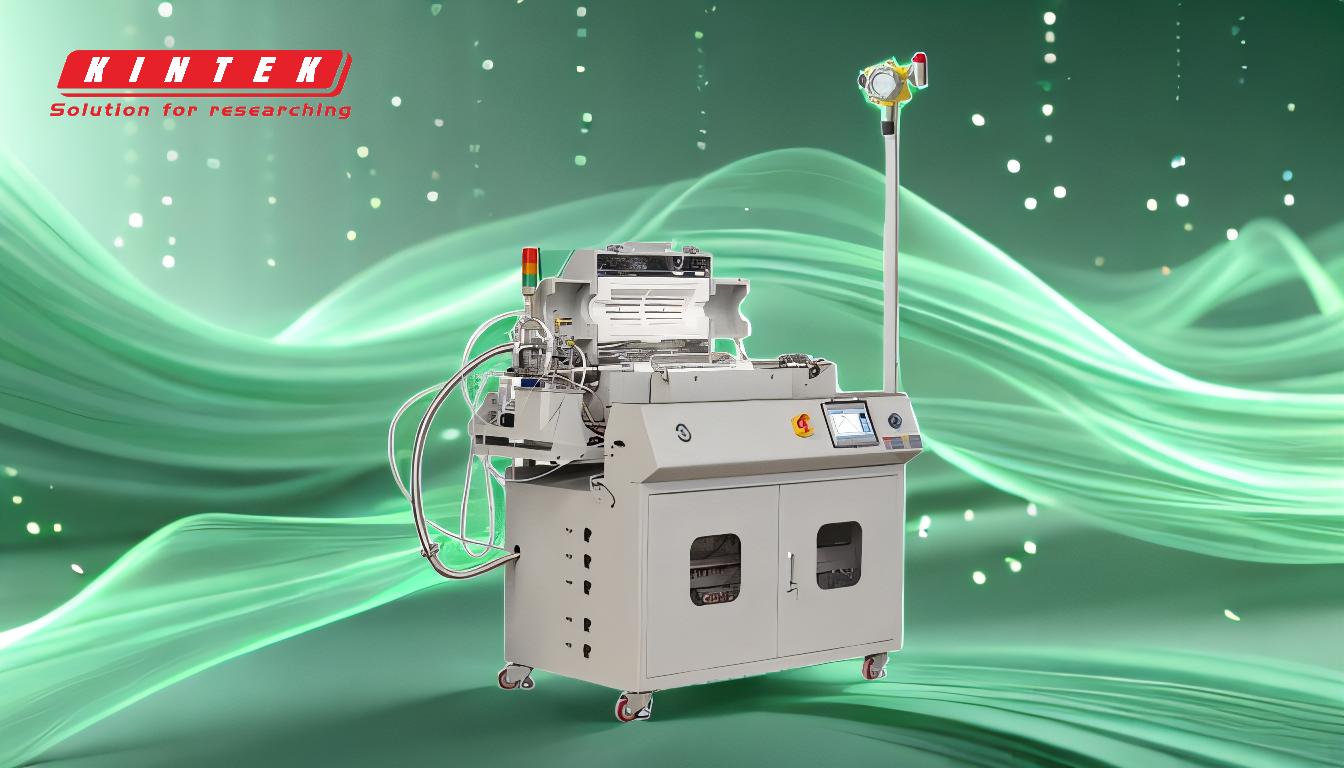
-
Process Differences:
- PVD: Involves physical processes such as sputtering or evaporation to deposit materials onto a substrate. It occurs in a vacuum at relatively low temperatures, making it suitable for temperature-sensitive substrates.
- DLC: A specific type of coating that can be applied using PVD or CVD methods. DLC coatings are characterized by their diamond-like properties, including high hardness and wear resistance.
-
Coating Properties:
- PVD: Known for high purity, uniformity, and excellent adhesion. PVD coatings are often harder and more corrosion-resistant than those applied by electroplating. They also offer high temperature and impact strength, excellent abrasion resistance, and durability.
- DLC: Offers exceptional hardness, low friction, and wear resistance, making it ideal for applications requiring reduced friction and increased durability. DLC coatings can also provide good chemical resistance and biocompatibility.
-
Application and Performance:
- PVD: Suitable for a wide range of materials, including metals, alloys, and ceramics. PVD coatings are less dense and less uniform compared to CVD coatings but are faster to apply. They are often used in applications requiring high wear resistance and durability.
- DLC: Typically used in applications where low friction and high wear resistance are critical, such as in automotive components, cutting tools, and medical devices. DLC coatings can be applied using PVD or CVD, with each method offering different advantages in terms of coating properties and application suitability.
-
Temperature Sensitivity:
- PVD: Operates at lower temperatures, making it suitable for substrates that cannot withstand high temperatures. This is a significant advantage over CVD, which requires higher processing temperatures.
- DLC: The application temperature for DLC coatings depends on the method used (PVD or CVD). PVD-applied DLC coatings benefit from lower processing temperatures, similar to other PVD coatings.
-
Coating Uniformity and Density:
- PVD: Coatings are less dense and less uniform compared to CVD coatings. However, PVD coatings are faster to apply and can be more versatile in terms of the materials that can be deposited.
- DLC: When applied using CVD, DLC coatings can be denser and more uniform, but this comes at the cost of higher processing temperatures and longer application times.
-
Optical Properties:
- PVD: Can be deposited with various optical properties, including transparency, reflectivity, and color. This makes PVD suitable for applications requiring specific aesthetic or functional optical characteristics.
- DLC: Typically not transparent, which limits its use in applications where optical clarity is required.
-
Durability and Wear Resistance:
- PVD: Generally offers better durability and wear resistance compared to CVD coatings. This makes PVD coatings ideal for applications where long-term performance and resistance to wear are critical.
- DLC: Known for its exceptional wear resistance and low friction, DLC coatings are often used in high-stress applications where these properties are essential.
In summary, while both PVD and DLC coatings offer significant advantages in terms of surface enhancement, they are suited to different applications based on their specific properties and processing requirements. PVD is a versatile and widely applicable coating technology, while DLC is a specialized coating known for its diamond-like properties, particularly in terms of hardness and wear resistance.
Summary Table:
Aspect | PVD | DLC |
---|---|---|
Process | Physical transfer of material (sputtering/evaporation) in a vacuum | Applied via PVD or CVD; mimics diamond-like properties |
Properties | High purity, uniformity, adhesion; hard, corrosion-resistant | Exceptional hardness, low friction, wear resistance |
Applications | Metals, alloys, ceramics; high wear resistance, durability | Automotive, cutting tools, medical devices; low friction, high stress |
Temperature | Low processing temperature; suitable for sensitive substrates | Depends on method (PVD/CVD); PVD benefits from lower temperatures |
Uniformity/Density | Less dense, less uniform; faster application | CVD-applied DLC is denser, more uniform; higher temperatures required |
Optical Properties | Customizable (transparency, reflectivity, color) | Typically not transparent; limited optical clarity |
Durability | Better durability, wear resistance compared to CVD | Exceptional wear resistance, low friction |
Need help deciding between PVD and DLC coatings? Contact our experts today for tailored solutions!