PVD (Physical Vapor Deposition) and DLC (Diamond-Like Carbon) coatings are both advanced surface treatment technologies, but they differ significantly in their processes, materials, and applications. PVD is a broad category of coating techniques that involve vaporizing a solid material in a vacuum and depositing it onto a substrate, resulting in thin, durable, and high-performance coatings. DLC, on the other hand, is a specific type of coating that consists of amorphous carbon with properties similar to diamond, offering exceptional hardness, low friction, and wear resistance. While DLC can be applied using PVD methods, it is distinct in its composition and characteristics. This explanation will explore the key differences between PVD and DLC coatings, focusing on their processes, properties, and applications.
Key Points Explained:
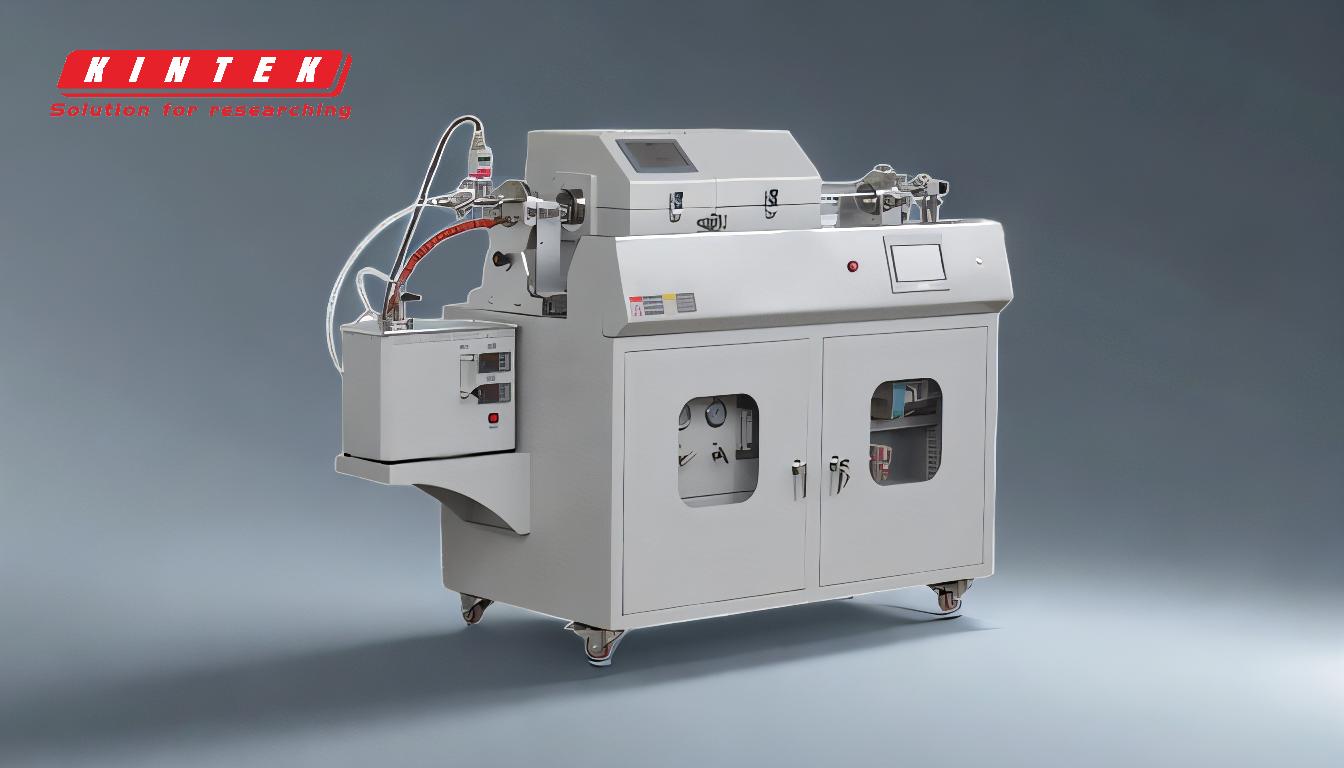
-
Process and Methodology:
- PVD: PVD involves the physical vaporization of a target material in a vacuum chamber, followed by its deposition onto a substrate. Common PVD methods include sputtering, evaporation, and arc deposition. The process occurs at relatively low temperatures, making it suitable for a wide range of substrates, including metals, alloys, and ceramics.
- DLC: DLC coatings are typically applied using PVD or CVD (Chemical Vapor Deposition) techniques. However, DLC specifically refers to the deposition of carbon atoms in an amorphous structure, which can include sp2 (graphite-like) and sp3 (diamond-like) bonds. The process often involves plasma-enhanced chemical vapor deposition (PECVD) or other specialized methods to achieve the desired diamond-like properties.
-
Material Composition:
- PVD: PVD coatings can be made from a wide variety of materials, including metals (e.g., titanium, chromium), alloys, and ceramics (e.g., titanium nitride, chromium nitride). The choice of material depends on the desired properties, such as hardness, corrosion resistance, or aesthetic appeal.
- DLC: DLC coatings are composed primarily of carbon, with varying proportions of sp2 and sp3 bonds. The sp3 content gives DLC its diamond-like hardness, while the sp2 content contributes to its low friction and lubricity. DLC can also be doped with elements like hydrogen, silicon, or metals to tailor its properties for specific applications.
-
Properties and Performance:
- PVD: PVD coatings are known for their high purity, uniformity, and excellent adhesion to substrates. They offer superior hardness, corrosion resistance, and durability compared to traditional coatings like electroplating. PVD coatings are also highly resistant to wear, abrasion, and high temperatures, making them ideal for demanding applications in aerospace, automotive, and medical industries.
- DLC: DLC coatings are characterized by their exceptional hardness (up to 90 GPa), low coefficient of friction, and excellent wear resistance. They are also biocompatible, making them suitable for medical implants and devices. DLC coatings provide superior protection against sliding friction, galling, and adhesive wear, which are common in high-stress applications.
-
Applications:
- PVD: PVD coatings are used in a wide range of industries, including thin film coatings for photovoltaics, semiconductor devices, optical components, and decorative finishes. They are also employed in high-performance applications such as cutting tools, automotive components, and aerospace parts.
- DLC: DLC coatings are particularly valuable in applications requiring extreme hardness and low friction, such as engine components, cutting tools, and medical devices. They are also used in consumer products like watch components and smartphone cases for their scratch resistance and aesthetic appeal.
-
Environmental and Economic Considerations:
- PVD: PVD is considered an environmentally friendly coating process because it produces no toxic waste or gases. It is also cost-effective for high-volume production due to its relatively fast deposition rates and ability to coat complex geometries.
- DLC: While DLC coatings can be more expensive to produce due to the specialized equipment and processes required, their long-lasting performance and ability to reduce wear and friction often result in lower lifecycle costs. DLC is also environmentally friendly, as it does not involve hazardous chemicals or byproducts.
-
Advantages and Limitations:
-
PVD:
- Advantages: Versatility in material selection, excellent adhesion, high hardness, and corrosion resistance. Suitable for a wide range of substrates and applications.
- Limitations: Limited coating thickness (typically 0.5 to 5 microns), potential for poor coating uniformity on complex geometries, and higher equipment costs.
-
DLC:
- Advantages: Exceptional hardness, low friction, wear resistance, and biocompatibility. Ideal for high-stress and precision applications.
- Limitations: Higher production costs, limited to carbon-based materials, and potential challenges in achieving uniform coatings on large or complex surfaces.
-
PVD:
In summary, while PVD and DLC coatings share some similarities in their deposition processes, they differ significantly in material composition, properties, and applications. PVD is a versatile and environmentally friendly coating method suitable for a wide range of materials and industries, while DLC offers unique diamond-like properties that make it ideal for high-performance and precision applications. Understanding these differences is crucial for selecting the appropriate coating technology for specific needs.
Summary Table:
Aspect | PVD Coatings | DLC Coatings |
---|---|---|
Process | Vaporization of target material in a vacuum chamber (e.g., sputtering, evaporation). | Deposition of carbon atoms in an amorphous structure (e.g., PECVD, PVD). |
Material Composition | Metals, alloys, ceramics (e.g., titanium nitride, chromium nitride). | Primarily carbon with sp2/sp3 bonds, often doped with hydrogen, silicon, or metals. |
Properties | High purity, uniformity, hardness, corrosion resistance, wear resistance. | Exceptional hardness (up to 90 GPa), low friction, wear resistance, biocompatibility. |
Applications | Aerospace, automotive, medical, thin films, decorative finishes. | Engine components, cutting tools, medical devices, consumer products. |
Advantages | Versatile, environmentally friendly, cost-effective for high-volume production. | Extreme hardness, low friction, long-lasting performance, biocompatibility. |
Limitations | Limited thickness, higher equipment costs, potential uniformity issues. | Higher production costs, limited to carbon-based materials, coating challenges. |
Need help choosing the right coating for your application? Contact our experts today!