PVD (Physical Vapor Deposition) and PECVD (Plasma-Enhanced Chemical Vapor Deposition) are two distinct thin-film deposition techniques used in various industries, including semiconductor manufacturing, optics, and coatings. PVD relies on physical processes such as sputtering or evaporation to deposit materials, while PECVD uses plasma to enhance chemical reactions at lower temperatures compared to traditional CVD. The key differences lie in their deposition mechanisms, temperature requirements, and the state of the deposited material (solid in PVD vs. gaseous in PECVD). PVD is generally safer and avoids toxic chemicals, whereas PECVD offers advantages like low-temperature deposition and energy efficiency.
Key Points Explained:
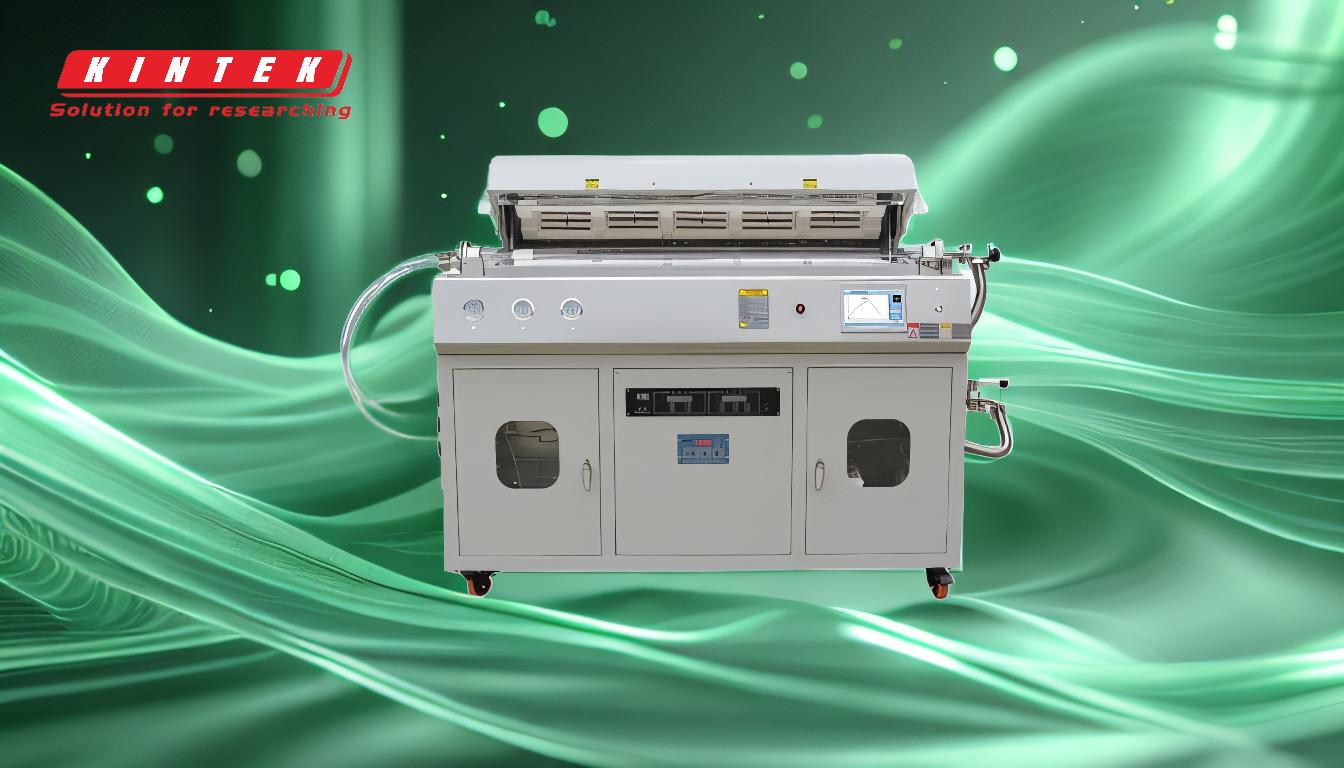
-
Deposition Mechanism:
- PVD: In PVD, the material to be deposited starts in a solid state. It is then transformed into a vapor through physical processes like sputtering or thermal evaporation. The vapor condenses onto the substrate to form a thin film. Common PVD methods include sputtering, vacuum evaporation, and electron-beam evaporation. For example, in sputtering, a high-voltage plasma is used to dislodge atoms from a target material, which then deposit onto the substrate.
- PECVD: PECVD involves chemical reactions in the gas phase, enhanced by plasma. The plasma provides the activation energy needed for the chemical reactions, allowing deposition at lower temperatures compared to traditional CVD. This makes PECVD suitable for temperature-sensitive substrates.
-
Material State:
- PVD: The deposited material in PVD is initially in a solid state. For instance, in thermal evaporation, the material is heated until it evaporates and then condenses onto the substrate.
- PECVD: In PECVD, the material is introduced in a gaseous form. The plasma facilitates chemical reactions that result in the deposition of a solid film on the substrate.
-
Temperature Requirements:
- PVD: PVD processes typically do not require heating the substrate itself, which can be advantageous for materials sensitive to high temperatures.
- PECVD: PECVD is known for its low-temperature deposition capability. The plasma's high-energy electrons provide the necessary activation energy, enabling deposition at temperatures much lower than those required for conventional CVD.
-
Safety and Environmental Impact:
- PVD: PVD processes are generally safer as they do not involve toxic chemicals. The absence of chemical reactions reduces the risk of hazardous by-products.
- PECVD: While PECVD is efficient and allows for low-temperature processing, it may involve the use of reactive gases, which can pose safety and environmental concerns.
-
Applications and Advantages:
- PVD: PVD is widely used for depositing metals and alloys in applications requiring high purity and adhesion. It is also favored for its simplicity and safety.
- PECVD: PECVD is advantageous for depositing dielectric films, such as silicon nitride and silicon dioxide, at low temperatures. It is particularly useful in the semiconductor industry for creating thin films on temperature-sensitive substrates.
-
Process Complexity:
- PVD: PVD processes are relatively straightforward, involving fewer steps and simpler equipment. For example, vacuum evaporation involves heating the material in a vacuum chamber until it evaporates and then condenses onto the substrate.
- PECVD: PECVD processes are more complex due to the need for plasma generation and control. The plasma must be carefully managed to ensure uniform deposition and avoid damage to the substrate.
In summary, PVD and PECVD differ fundamentally in their deposition mechanisms, material states, temperature requirements, and safety considerations. PVD is characterized by its physical processes and solid-state material deposition, while PECVD leverages plasma-enhanced chemical reactions for low-temperature deposition of gaseous materials. Each method has its unique advantages and is chosen based on the specific requirements of the application.
Summary Table:
Aspect | PVD | PECVD |
---|---|---|
Deposition Mechanism | Physical processes (e.g., sputtering, evaporation) | Plasma-enhanced chemical reactions |
Material State | Starts as solid, deposited as vapor | Introduced as gas, deposited as solid film |
Temperature | No substrate heating required | Low-temperature deposition enabled by plasma |
Safety | Safer, avoids toxic chemicals | May involve reactive gases, posing safety concerns |
Applications | Metals, alloys, high-purity coatings | Dielectric films, semiconductor industry |
Process Complexity | Simpler, fewer steps | More complex, requires plasma generation and control |
Need help choosing between PVD and PECVD for your application? Contact our experts today for tailored advice!