Thermal Chemical Vapor Deposition (CVD) and Plasma-Enhanced Chemical Vapor Deposition (PECVD) are both techniques used to deposit thin films onto substrates, but they differ significantly in their mechanisms, operating conditions, and applications. Thermal CVD relies on high temperatures to drive chemical reactions for film deposition, while PECVD uses plasma to provide the activation energy needed for the reactions, enabling lower-temperature processing. This distinction makes PECVD more suitable for temperature-sensitive substrates and applications requiring precise control over film properties. Below, we explore the key differences between these two methods in detail.
Key Points Explained:
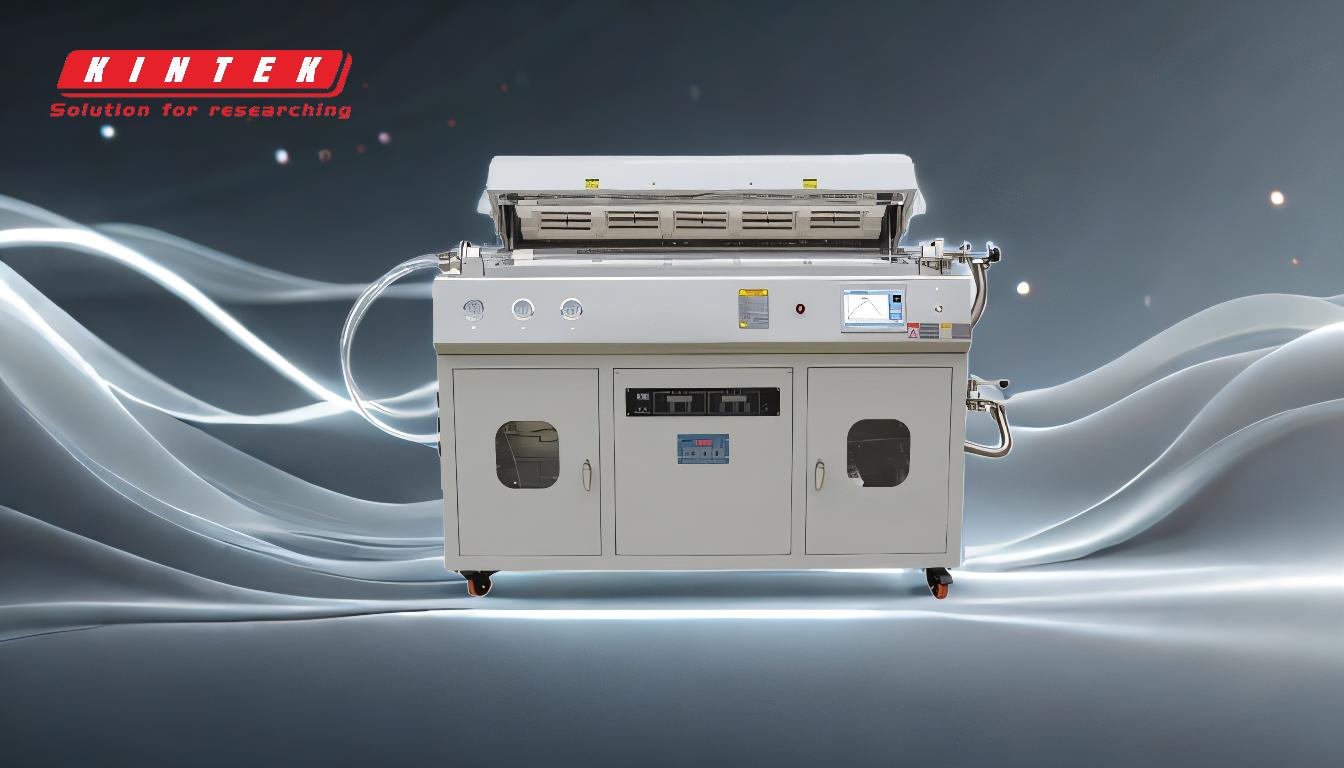
-
Mechanism of Deposition:
- Thermal CVD: This method relies on heat to activate the chemical reactions between gaseous precursors and the substrate. The high temperatures (typically 450°C to 1050°C) provide the energy needed for the reactions to occur, leading to the formation of a solid film on the substrate.
- PECVD: In contrast, PECVD uses plasma (a partially ionized gas) to generate high-energy electrons. These electrons provide the activation energy required for the chemical reactions, allowing deposition to occur at significantly lower temperatures (often below 400°C). This makes PECVD ideal for substrates that cannot withstand high temperatures.
-
Temperature Requirements:
- Thermal CVD: Requires high temperatures, which can limit its use with temperature-sensitive materials such as polymers or certain semiconductors. The high temperatures can also lead to thermal stress and unwanted diffusion in the substrate.
- PECVD: Operates at much lower temperatures, making it compatible with a wider range of materials, including those used in microelectronics and flexible substrates.
-
Film Quality and Properties:
- Thermal CVD: Typically produces high-quality, dense films with excellent uniformity and stoichiometry. However, the high temperatures can sometimes introduce impurities or defects due to thermal decomposition of precursors.
- PECVD: While it can produce high-quality films, the use of plasma can sometimes result in films with lower density and higher defect concentrations. However, PECVD offers better control over film properties, such as stress and composition, due to the ability to tune plasma parameters.
-
Deposition Rate:
- Thermal CVD: Generally has a slower deposition rate compared to PECVD, as the chemical reactions are driven solely by thermal energy.
- PECVD: Offers faster deposition rates due to the high energy provided by the plasma, which accelerates the chemical reactions.
-
Applications:
- Thermal CVD: Commonly used in applications requiring high-temperature stability and high-purity films, such as in the production of silicon carbide coatings, diamond films, and certain semiconductor devices.
- PECVD: Widely used in the semiconductor industry for depositing dielectric layers, passivation layers, and thin-film transistors. Its low-temperature capability also makes it suitable for flexible electronics and biomedical applications.
-
Equipment Complexity:
- Thermal CVD: Requires high-temperature furnaces and precise temperature control systems, which can be complex and expensive.
- PECVD: Involves plasma generation systems, which add complexity to the equipment. However, the ability to operate at lower temperatures can reduce overall energy costs and simplify substrate handling.
-
Environmental and Safety Considerations:
- Thermal CVD: The high temperatures can lead to the formation of corrosive byproducts, requiring robust exhaust and safety systems.
- PECVD: While it operates at lower temperatures, the use of plasma can generate reactive species and require careful handling of toxic precursors. However, the lower temperatures generally reduce the risk of thermal decomposition and associated hazards.
In summary, the choice between thermal CVD and PECVD depends on the specific requirements of the application, including substrate material, desired film properties, and temperature constraints. Thermal CVD is preferred for high-temperature, high-purity applications, while PECVD offers greater flexibility and lower-temperature processing, making it ideal for modern semiconductor and flexible electronics manufacturing.
Summary Table:
Aspect | Thermal CVD | PECVD |
---|---|---|
Mechanism | Relies on heat for chemical reactions. | Uses plasma for activation energy, enabling lower-temperature processing. |
Temperature | High (450°C to 1050°C), unsuitable for temperature-sensitive materials. | Low (often below 400°C), ideal for sensitive substrates. |
Film Quality | High-quality, dense films but may have impurities due to high temperatures. | Good quality with better control over film properties like stress. |
Deposition Rate | Slower due to reliance on thermal energy. | Faster due to plasma acceleration. |
Applications | High-temperature, high-purity films (e.g., silicon carbide, diamond films). | Semiconductor, flexible electronics, and biomedical applications. |
Equipment Complexity | Requires high-temperature furnaces, complex and expensive. | Plasma systems add complexity but reduce energy costs. |
Safety Considerations | High temperatures may produce corrosive byproducts. | Lower temperatures reduce risks, but plasma requires careful handling. |
Need help choosing between thermal CVD and PECVD for your application? Contact our experts today for personalized advice!