The size of the grinding balls in a ball mill significantly influences milling performance, affecting both efficiency and product quality. Smaller balls are more effective for grinding fine particles due to their higher surface area-to-volume ratio, which enhances the frequency of collisions and grinding action. Conversely, larger balls are better suited for grinding coarse particles because they deliver greater impact energy, breaking down larger materials more effectively. The choice of ball size should align with the desired particle size distribution and the nature of the material being processed, as improper sizing can lead to inefficient grinding, excessive energy consumption, or inconsistent product quality.
Key Points Explained:
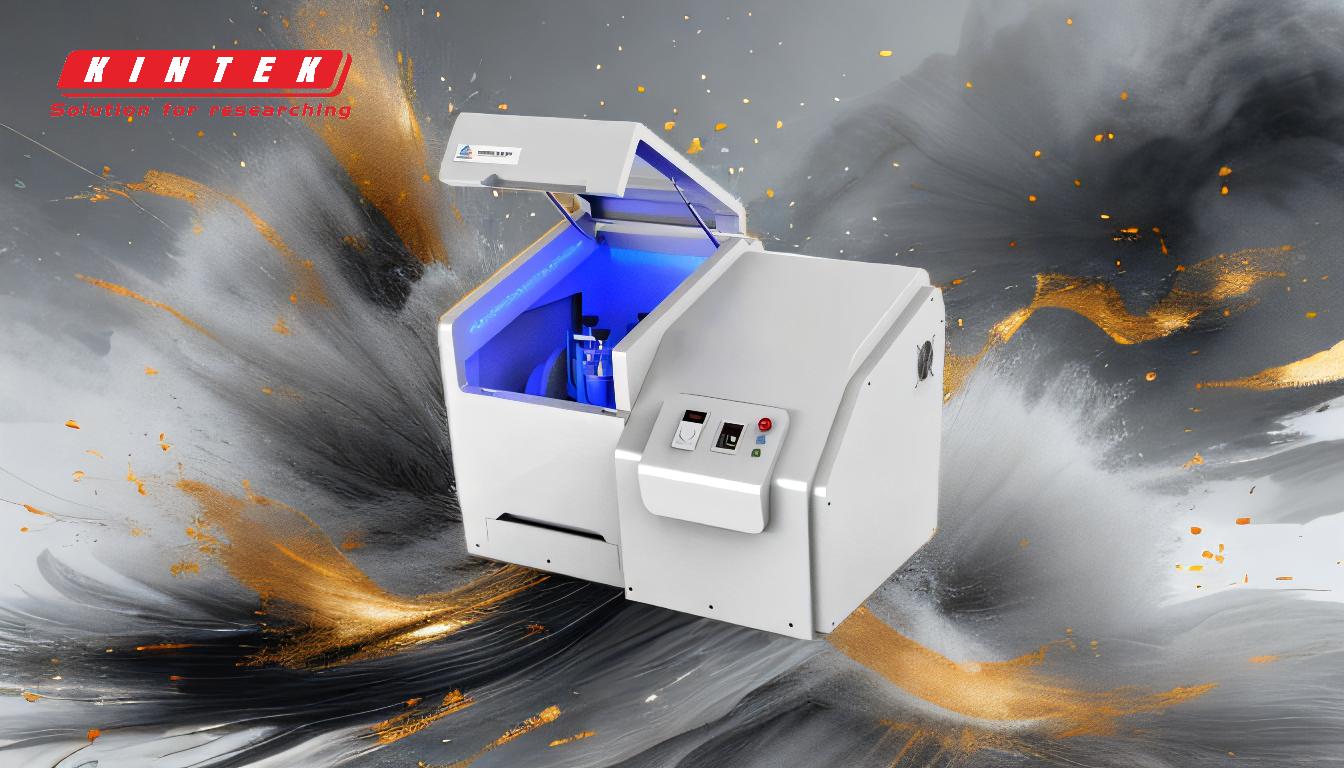
-
Impact on Grinding Efficiency:
-
Smaller Balls:
- Higher surface area-to-volume ratio increases the frequency of collisions, making them ideal for fine grinding.
- Better suited for materials requiring a narrow particle size distribution.
-
Larger Balls:
- Deliver greater impact energy, making them effective for breaking down coarse particles.
- Suitable for materials with larger initial particle sizes or those requiring less precision in final particle size.
-
Smaller Balls:
-
Effect on Product Quality:
-
Smaller Balls:
- Produce finer and more uniform particles, which is critical in industries like pharmaceuticals or cosmetics.
- May reduce the risk of over-grinding or contamination due to gentler grinding action.
-
Larger Balls:
- Can lead to a broader particle size distribution, which may be acceptable in industries like mining or cement production.
- Risk of producing overly coarse particles or uneven grinding if not matched to the material.
-
Smaller Balls:
-
Energy Consumption:
-
Smaller Balls:
- Generally require more energy for fine grinding due to the increased number of collisions needed to achieve the desired particle size.
-
Larger Balls:
- May reduce energy consumption for coarse grinding by delivering more energy per collision, but inefficient sizing can lead to wasted energy.
-
Smaller Balls:
-
Material Properties:
- The hardness, brittleness, and initial particle size of the material being ground play a critical role in determining the optimal ball size.
- Softer materials may benefit from smaller balls to avoid excessive fragmentation, while harder materials may require larger balls to achieve effective grinding.
-
Operational Considerations:
- The mill's rotational speed and filling ratio must be adjusted based on ball size to optimize performance.
- Mixing different ball sizes (e.g., a combination of small and large balls) can sometimes improve grinding efficiency and product quality by balancing impact energy and collision frequency.
-
Industry-Specific Applications:
- Pharmaceuticals and Fine Chemicals: Prefer smaller balls for precise control over particle size.
- Mining and Cement: Often use larger balls to handle coarse materials and high throughput requirements.
By carefully selecting the appropriate ball size based on the material properties and desired outcomes, milling performance can be optimized, leading to improved efficiency, reduced energy consumption, and higher-quality products.
Summary Table:
Aspect | Smaller Balls | Larger Balls |
---|---|---|
Grinding Efficiency | Higher collision frequency, ideal for fine particles | Greater impact energy, better for coarse particles |
Product Quality | Finer, uniform particles; suitable for pharmaceuticals and cosmetics | Broader particle size distribution; used in mining and cement |
Energy Consumption | Higher energy for fine grinding | Lower energy for coarse grinding |
Material Suitability | Best for softer materials or fine grinding needs | Best for harder materials or coarse grinding needs |
Applications | Pharmaceuticals, fine chemicals | Mining, cement |
Need help selecting the right grinding balls for your ball mill? Contact our experts today for tailored advice!