The moisture content of biomass feedstock plays a significant role in the pyrolysis process, influencing the efficiency, product yield, and quality of the end products. Ideally, the moisture content should be around 10% to optimize the process. Higher moisture levels lead to the production of excessive water, reducing the energy efficiency and yield of valuable products like bio-oil. Conversely, lower moisture levels can result in the production of dust instead of oil, compromising the quality of the output. High moisture waste streams, such as sludge and meat processing wastes, require pre-drying to achieve the optimal moisture content before undergoing pyrolysis.
Key Points Explained:
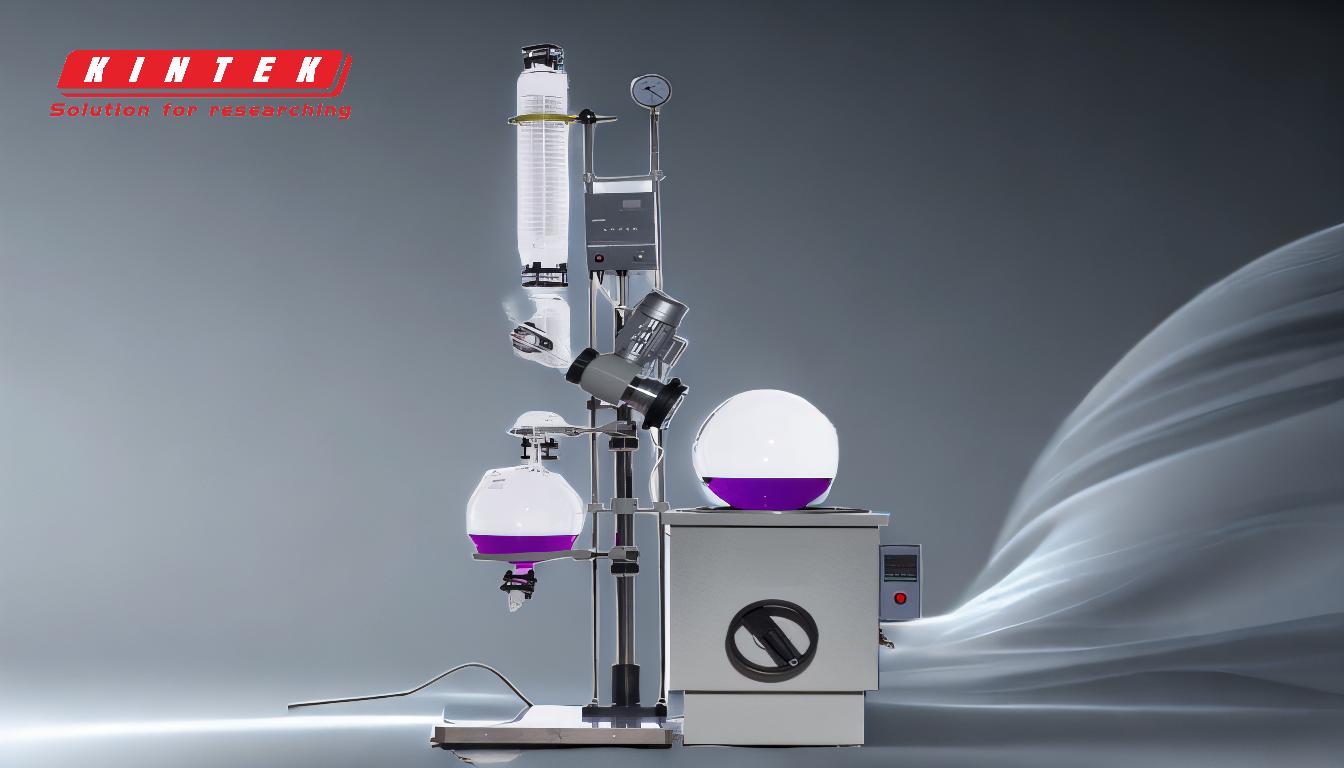
-
Optimal Moisture Content (10%):
- The ideal moisture content for biomass pyrolysis is approximately 10%. This level ensures a balance between energy efficiency and product yield.
- At this moisture level, the biomass can undergo pyrolysis effectively, producing a good yield of bio-oil, biochar, and syngas without excessive energy loss.
-
Impact of High Moisture Content:
- Excessive Water Production: Higher moisture levels lead to the production of large amounts of water during pyrolysis. This not only reduces the energy efficiency of the process but also dilutes the bio-oil, making it less valuable.
- Energy Consumption: Drying high moisture biomass requires additional energy, increasing the overall cost and complexity of the pyrolysis process.
- Process Efficiency: High moisture content can lead to incomplete pyrolysis, resulting in lower yields of desired products and higher amounts of unwanted by-products.
-
Impact of Low Moisture Content:
- Dust Production: Biomass with very low moisture content can produce dust instead of oil during pyrolysis. This dust is less valuable and can complicate the handling and storage of the end products.
- Combustion Risk: Extremely dry biomass can be more prone to combustion, posing safety risks during the pyrolysis process.
-
Pre-Treatment for High Moisture Waste Streams:
- Drying Requirement: High moisture waste streams, such as sludge and meat processing wastes, need to be dried before pyrolysis to achieve the optimal moisture content.
- Drying Methods: Various drying methods, such as thermal drying or mechanical dewatering, can be employed to reduce the moisture content to the desired level. The choice of drying method depends on the specific characteristics of the biomass and the available resources.
-
Overall Process Optimization:
- Control of Moisture Content: Proper control of moisture content is crucial for optimizing the pyrolysis process. It affects not only the yield and quality of the end products but also the energy efficiency and safety of the process.
- Integration with Other Factors: Moisture content should be considered alongside other factors such as temperature, residence time, and pressure to achieve optimal performance and desired end products.
In summary, maintaining the moisture content of biomass feedstock at around 10% is essential for efficient and effective pyrolysis. Both high and low moisture levels can negatively impact the process, leading to reduced yields, lower quality products, and increased costs. Pre-treatment steps, such as drying, are necessary for high moisture waste streams to ensure they meet the optimal moisture content before undergoing pyrolysis.
Summary Table:
Aspect | Impact |
---|---|
Optimal Moisture (10%) | Ensures balance between energy efficiency and product yield. |
High Moisture Content | Reduces energy efficiency, dilutes bio-oil, and increases drying costs. |
Low Moisture Content | Produces dust instead of oil, increases combustion risk. |
Pre-Treatment for High Moisture | Drying required for sludge and meat wastes to achieve 10% moisture. |
Optimize your biomass pyrolysis process—contact our experts today for tailored solutions!