The electron beam method of deposition, also known as electron-beam physical vapor deposition (EBPVD) or electron-beam evaporation, is a technique used to deposit thin films of material onto a substrate. This process involves bombarding a target material with a focused electron beam under high vacuum conditions, causing the material to evaporate or sublimate. The vaporized material then travels through the vacuum chamber and condenses onto the substrate, forming a thin, uniform coating. This method is particularly useful for depositing metals and ceramics with high melting points, and it is widely used in industries such as optics, electronics, and aerospace due to its ability to produce high-purity, dense coatings with precise thickness control.
Key Points Explained:
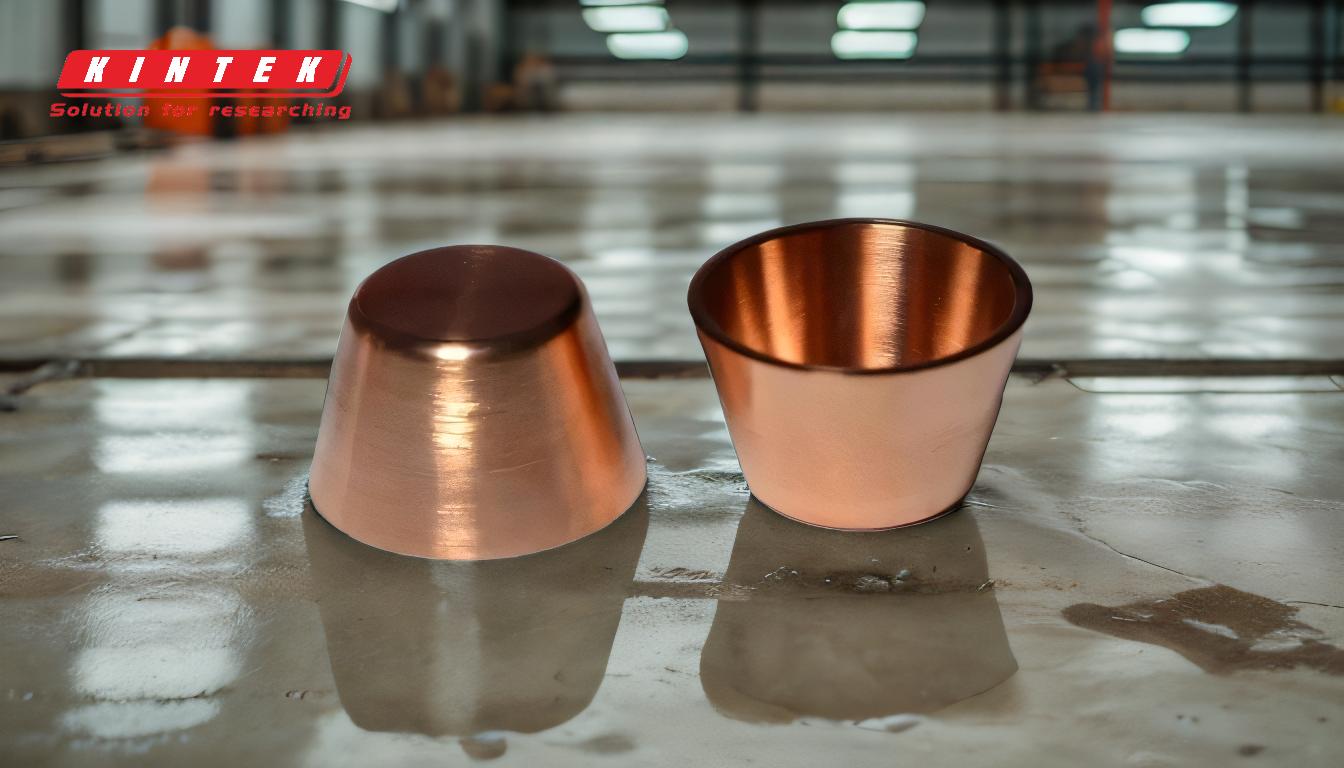
-
Mechanism of Electron Beam Deposition:
- Electron Beam Generation: The process begins with the generation of an electron beam, typically using thermionic emission (heating a tungsten filament) or field emission (using a high electric field). The electrons are then accelerated and focused into a beam using electric and magnetic fields.
- Material Evaporation: The focused electron beam is directed onto a target material, usually in the form of small pellets or granules, placed inside a crucible. The energy from the electron beam heats the material to high temperatures, causing it to evaporate or sublimate.
- Vapor Deposition: The vaporized material travels through the vacuum chamber and condenses onto the substrate, forming a thin film. The high vacuum environment ensures a long mean free path for the vapor, allowing most of the material to reach the substrate without significant loss.
-
High Vacuum Environment:
- Vacuum Levels: The process is carried out under high vacuum conditions, typically in the range of 10^-7 mbar or lower. This minimizes contamination from background gases and allows for high vapor pressures at relatively low temperatures.
- Advantages of Vacuum: The vacuum environment reduces the likelihood of chemical reactions between the vaporized material and residual gases, resulting in high-purity coatings. It also ensures that the vaporized material travels in a straight line (line-of-sight deposition), which is beneficial for precise coating applications.
-
Materials Suitable for EBPVD:
- Metals: Metals such as aluminum, gold, and titanium are commonly deposited using EBPVD. These materials typically melt before evaporating, allowing for controlled deposition.
- Ceramics: Ceramics and other materials with high melting points can be deposited through sublimation, where the material transitions directly from a solid to a gaseous state without passing through a liquid phase.
-
Advantages of Electron Beam Deposition:
- High Purity: The high vacuum environment and precise control over the electron beam result in coatings with minimal impurities.
- High Melting Point Materials: EBPVD is capable of depositing materials with very high melting points, which are difficult to process using other methods.
- Precision Control: The process allows for precise control over film thickness, uniformity, and composition, making it suitable for applications requiring high precision, such as optical coatings and semiconductor devices.
-
Applications of Electron Beam Deposition:
- Optical Coatings: EBPVD is widely used to deposit thin films on optical components, such as lenses and mirrors, to enhance their performance by reducing reflection or increasing transmission.
- Electronics: In the electronics industry, EBPVD is used to deposit thin films of conductive materials, such as aluminum and gold, onto semiconductor devices.
- Aerospace: The aerospace industry utilizes EBPVD for depositing protective coatings on turbine blades and other components to improve their resistance to high temperatures and corrosion.
-
Enhancements to the Process:
- Ion Beam Assistance: The use of an ion beam in conjunction with EBPVD can enhance the adhesion energy of the deposited film, resulting in denser and more robust coatings with reduced stress.
- Computer Control: Modern EBPVD systems often incorporate computer-controlled parameters, such as heating, vacuum levels, substrate positioning, and rotation, to achieve conformal coatings with pre-specified thicknesses and properties.
In summary, electron beam deposition is a versatile and precise method for depositing thin films of various materials onto substrates. Its ability to operate under high vacuum conditions and deposit high-purity, high-melting-point materials makes it an essential technique in industries requiring advanced material coatings.
Summary Table:
Aspect | Details |
---|---|
Process | Bombard target material with an electron beam under high vacuum conditions. |
Key Materials | Metals (e.g., aluminum, gold) and ceramics with high melting points. |
Advantages | High purity, precise thickness control, and ability to deposit high-melting-point materials. |
Applications | Optical coatings, electronics, aerospace components. |
Enhancements | Ion beam assistance and computer-controlled parameters for better results. |
Discover how electron beam deposition can elevate your projects—contact us today for expert guidance!