Pyrolysis is a thermal decomposition process that converts organic materials into gases, liquids, and solids in the absence of oxygen. The energy efficiency of pyrolysis depends on several factors, including the composition of the feedstock, operating conditions (temperature, pressure, residence time), and the design and maintenance of the pyrolysis furnace. Optimal control of these factors ensures maximum conversion of feedstock into valuable end products, such as biochar, bio-oil, and syngas. The efficiency is also influenced by the type of biomass or waste used, its moisture content, and the ability to recover and utilize the energy produced during the process. Proper operation and maintenance are critical to achieving high energy efficiency and ensuring safety.
Key Points Explained:
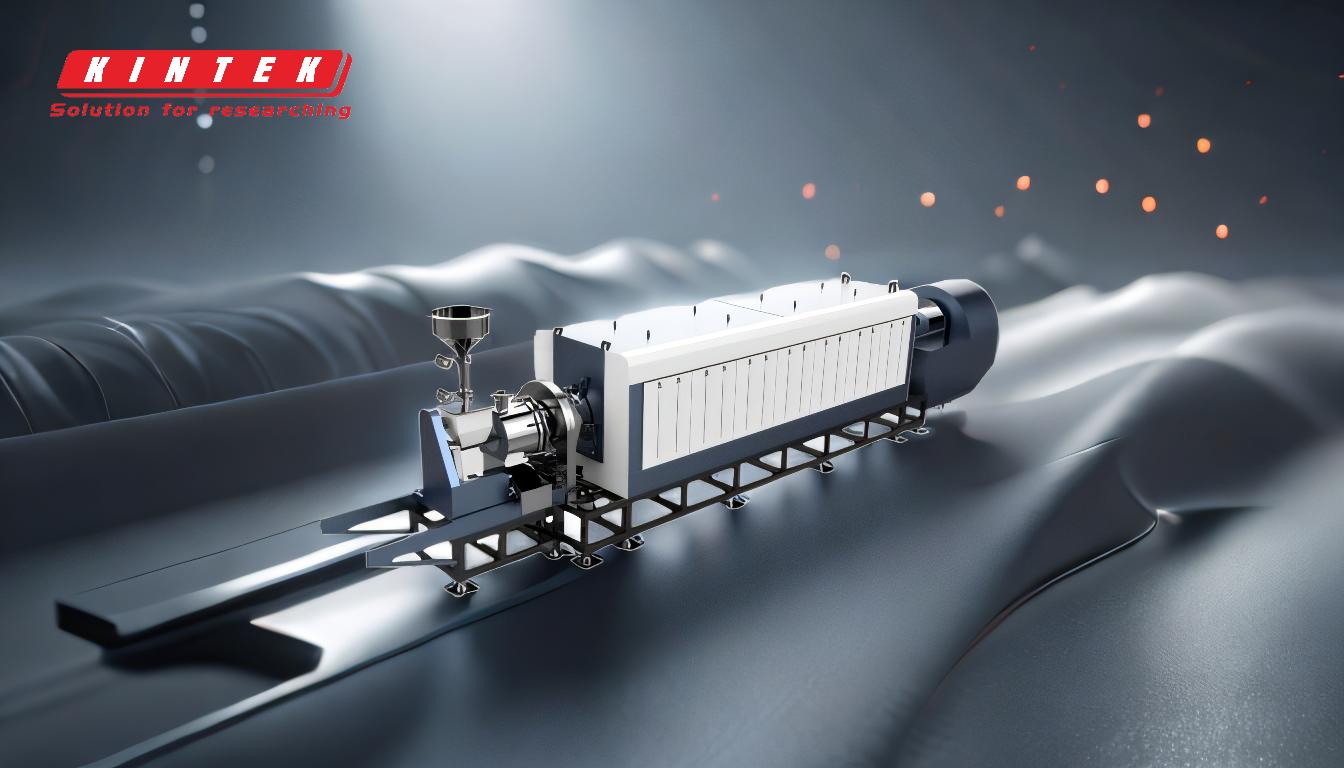
-
Feedstock Composition and Quality:
- The type of feedstock (e.g., biomass, plastic, or municipal waste) significantly impacts pyrolysis efficiency. Biomass with high organic content and low moisture levels is more efficient to process.
- Moisture content in the feedstock affects energy efficiency because excess moisture requires additional energy to evaporate, reducing the overall energy yield.
- The composition of the waste flow determines the extent to which the organic fraction can be degraded and converted into gas, which directly influences the energy output.
-
Operating Conditions:
- Temperature: Pyrolysis efficiency is highly dependent on the furnace temperature. Higher temperatures generally increase the rate of decomposition but must be optimized to avoid excessive energy consumption or unwanted byproducts.
- Residence Time: The duration that the feedstock remains in the pyrolysis furnace affects the completeness of the thermal decomposition. Longer residence times can improve conversion efficiency but may also increase energy consumption.
- Pressure: The pressure inside the furnace influences the chemical reactions and the quality of the end products. Controlled pressure settings are essential for maximizing energy efficiency.
-
Furnace Design and Maintenance:
- Proper furnace design ensures efficient heat transfer and minimizes energy losses. Advanced designs may include features like heat recovery systems to improve overall efficiency.
- Regular maintenance is crucial to prevent inefficiencies caused by equipment wear and tear, such as heat exchanger fouling or reactor blockages.
-
Energy Recovery and Utilization:
- The energy efficiency of pyrolysis is also determined by the ability to recover and utilize the energy produced during the process. For example, syngas generated during pyrolysis can be used to power the furnace or for other energy needs, reducing reliance on external energy sources.
- Byproducts like biochar and bio-oil can be further processed or used as energy sources, enhancing the overall energy efficiency of the system.
-
Environmental and Safety Considerations:
- Proper control of operating conditions not only improves energy efficiency but also ensures safety and minimizes environmental impacts. For example, maintaining optimal temperature and pressure reduces the risk of uncontrolled reactions or emissions.
In summary, the energy efficiency of pyrolysis is a complex interplay of feedstock characteristics, operating conditions, furnace design, and energy recovery strategies. By optimizing these factors, pyrolysis can be a highly efficient method for converting waste and biomass into valuable energy products.
Summary Table:
Factor | Impact on Efficiency |
---|---|
Feedstock Composition | High organic content and low moisture improve efficiency. |
Temperature | Optimal temperature increases decomposition rate without excessive energy consumption. |
Residence Time | Longer times improve conversion but may increase energy use. |
Furnace Design | Advanced designs with heat recovery systems enhance efficiency. |
Energy Recovery | Utilizing syngas and byproducts like biochar reduces external energy reliance. |
Optimize your pyrolysis process for better efficiency—contact our experts today!