Biochar is a carbon-rich material produced through the pyrolysis of biomass, a process that involves heating organic materials in the absence of oxygen. The feedstock used for biochar production plays a critical role in determining the quality, properties, and applications of the final product. Common feedstocks include wood (such as pine wood), agricultural residues (e.g., wheat straw, sugarcane bagasse, rice straw), green waste, dried algae, and even municipal waste. These materials are chosen for their availability, carbon content, and suitability for pyrolysis. The selection of feedstock depends on factors such as regional availability, cost, and the intended use of the biochar.
Key Points Explained:
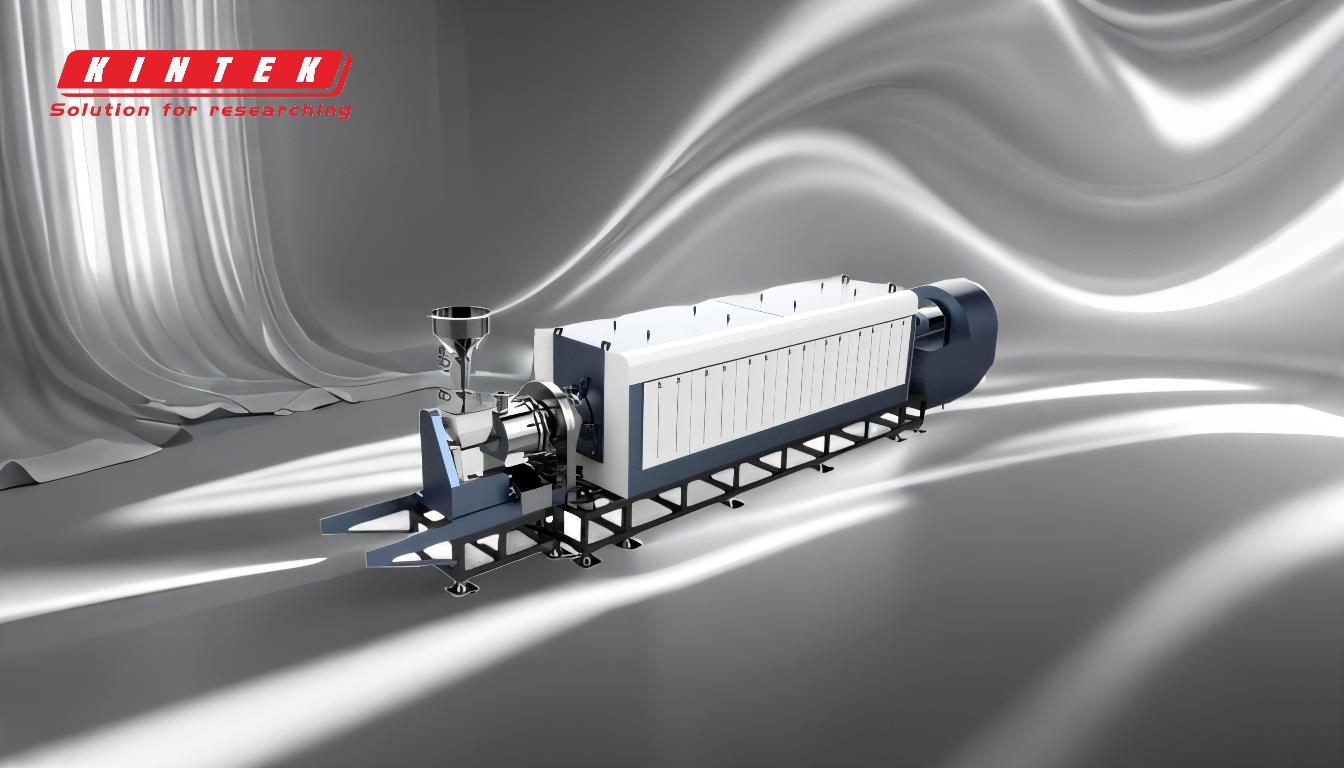
-
Wood as a Primary Feedstock:
- Types of Wood: Pine wood, forest trees, and branches are commonly used due to their high carbon content and widespread availability.
- Advantages: Wood is a reliable and consistent feedstock, producing biochar with stable properties suitable for soil amendment, carbon sequestration, and other applications.
- Applications: Biochar from wood is often used in agriculture to improve soil fertility and water retention.
-
Agricultural Residues:
- Examples: Wheat straw, sugarcane bagasse, rice straw, and cotton stalks are common agricultural residues used as feedstock.
- Benefits: These residues are often byproducts of farming, making them cost-effective and sustainable feedstocks.
- Challenges: Agricultural residues may have varying compositions, which can affect the consistency of the biochar produced.
-
Green Waste:
- Definition: Green waste includes yard trimmings, garden waste, and other plant-based materials.
- Sustainability: Using green waste for biochar production helps reduce landfill waste and promotes recycling.
- Applications: Biochar from green waste is often used in landscaping and urban agriculture.
-
Dried Algae:
- Unique Properties: Algae are rich in nutrients and have a high growth rate, making them an efficient feedstock.
- Applications: Biochar from algae is particularly useful in nutrient-rich soil amendments and wastewater treatment due to its high mineral content.
-
Municipal and Industrial Waste:
- Types: Sewage sludge and certain types of municipal waste can be converted into biochar.
- Environmental Benefits: This approach helps manage waste and reduces environmental pollution.
- Considerations: The feedstock must be carefully selected to avoid contaminants that could affect the quality of the biochar.
-
Energy Crops and Waste Wood:
- Energy Crops: Crops like switchgrass and miscanthus are grown specifically for energy production and can also serve as biochar feedstocks.
- Waste Wood: This includes wood scraps, sawdust, and other wood byproducts from industrial processes.
- Advantages: These feedstocks are renewable and help utilize waste materials effectively.
-
Factors Influencing Feedstock Selection:
- Availability: The choice of feedstock often depends on what is locally available to minimize transportation costs.
- Cost: Feedstock cost is a significant factor, especially for large-scale biochar production.
- End-Use Requirements: The intended application of the biochar (e.g., soil amendment, water filtration) influences the type of feedstock used.
By understanding the diverse feedstocks available for biochar production, purchasers and producers can make informed decisions that align with their sustainability goals and application needs. Each feedstock offers unique benefits and challenges, making it essential to evaluate them based on specific project requirements.
Summary Table:
Feedstock Type | Examples | Advantages | Applications |
---|---|---|---|
Wood | Pine wood, forest trees, branches | High carbon content, consistent properties | Soil amendment, carbon sequestration |
Agricultural Residues | Wheat straw, sugarcane bagasse, rice straw | Cost-effective, sustainable | Soil fertility, water retention |
Green Waste | Yard trimmings, garden waste | Reduces landfill waste, promotes recycling | Landscaping, urban agriculture |
Dried Algae | Nutrient-rich algae | High mineral content, rapid growth | Nutrient-rich soil amendments, wastewater treatment |
Municipal/Industrial Waste | Sewage sludge, municipal waste | Manages waste, reduces pollution | Waste management, environmental cleanup |
Energy Crops/Waste Wood | Switchgrass, miscanthus, sawdust | Renewable, utilizes waste materials | Energy production, soil improvement |
Ready to choose the right feedstock for your biochar production? Contact our experts today to get started!