The flash evaporation method for thin film deposition is a specialized technique within the broader category of physical vapor deposition (PVD). It involves rapidly heating a small amount of material to its vaporization point in a vacuum environment, causing it to evaporate almost instantaneously. This vapor is then deposited onto a substrate to form a thin film. The method is particularly useful for depositing materials with high melting points or those that decompose at high temperatures. Flash evaporation ensures uniform deposition and is often used in applications requiring precise control over film thickness and composition.
Key Points Explained:
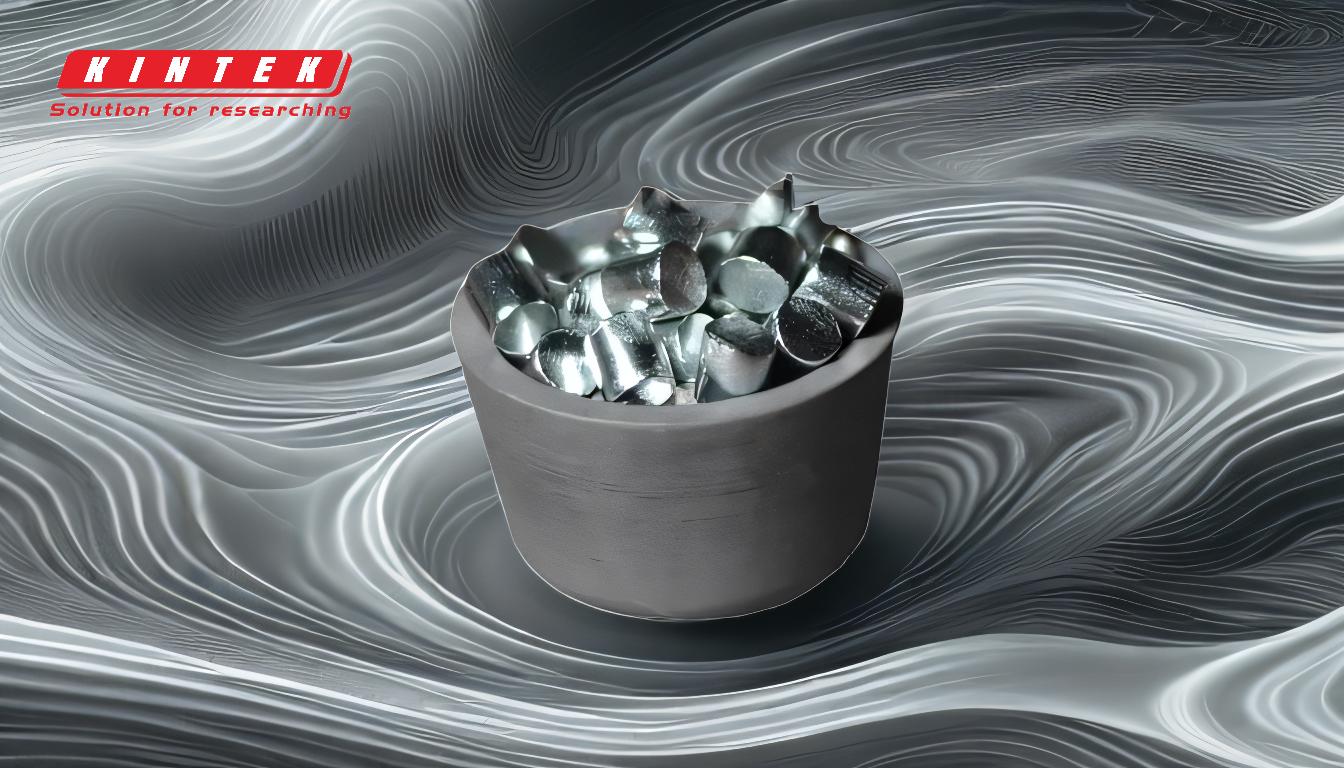
-
Definition and Process of Flash Evaporation:
- Flash evaporation is a PVD technique where a small quantity of material is heated rapidly to its vaporization point in a vacuum.
- The material evaporates almost instantaneously, and the resulting vapor is deposited onto a substrate to form a thin film.
- This method is particularly effective for materials that have high melting points or are prone to decomposition at elevated temperatures.
-
Advantages of Flash Evaporation:
- Uniform Deposition: The rapid evaporation and deposition process ensures a uniform thin film, which is crucial for applications requiring precise thickness control.
- High Purity: Since the process occurs in a vacuum, it minimizes contamination, resulting in high-purity films.
- Versatility: Flash evaporation can be used to deposit a wide range of materials, including metals, alloys, and compounds.
-
Applications of Flash Evaporation:
- Electronics: Used in the fabrication of semiconductor devices, where precise control over film thickness and composition is essential.
- Optics: Employed in the production of optical coatings, such as anti-reflective coatings and mirrors.
- Research and Development: Utilized in laboratories for developing new materials and studying their properties.
-
Comparison with Other PVD Techniques:
- Thermal Evaporation: Unlike traditional thermal evaporation, which heats the material slowly, flash evaporation heats the material rapidly, reducing the risk of decomposition.
- Sputtering: While sputtering involves bombarding a target material with ions to eject atoms for deposition, flash evaporation relies on rapid heating to achieve vaporization.
- Electron Beam Evaporation: Both methods involve heating the material to its vaporization point, but flash evaporation is typically faster and more suitable for materials that decompose at high temperatures.
-
Challenges and Considerations:
- Material Compatibility: Not all materials are suitable for flash evaporation, particularly those that do not vaporize cleanly or require very high temperatures.
- Equipment Complexity: The equipment for flash evaporation can be more complex and expensive compared to other PVD methods.
- Control of Deposition Rate: Achieving the desired deposition rate and film thickness requires precise control over the heating process and vacuum conditions.
-
Future Directions:
- Nanotechnology: Flash evaporation is being explored for the deposition of nanomaterials, where precise control over film thickness and composition is critical.
- Advanced Materials: Research is ongoing to adapt flash evaporation for the deposition of advanced materials, such as complex oxides and high-entropy alloys.
In summary, flash evaporation is a versatile and effective method for thin film deposition, particularly suited for materials with high melting points or those prone to decomposition. Its ability to produce uniform, high-purity films makes it invaluable in various high-tech applications, from electronics to optics. However, the method's complexity and material compatibility considerations must be carefully managed to achieve optimal results.
Summary Table:
Aspect | Details |
---|---|
Process | Rapid heating of material in a vacuum, leading to instant vaporization. |
Advantages | Uniform deposition, high purity, and material versatility. |
Applications | Electronics, optics, and R&D. |
Comparison with PVD | Faster than thermal evaporation; avoids decomposition risks. |
Challenges | Material compatibility, equipment complexity, and precise control required. |
Future Directions | Nanotechnology and advanced materials deposition. |
Interested in flash evaporation for your thin film needs? Contact us today to learn more!