Graphite furnaces are versatile high-temperature tools used across various industries and research fields. They are primarily employed for processes requiring controlled heating environments, such as melting, sintering, annealing, and graphitizing. These furnaces operate in vacuum or protective atmospheres to prevent oxidation and contamination, making them ideal for material processing, alloy production, and advanced material research. Their applications span from industrial manufacturing to scientific investigations, including reaction kinetics studies and solid electrolyte heating. The unique properties of graphite, such as high thermal conductivity and resistance to extreme temperatures, make these furnaces indispensable for high-temperature applications.
Key Points Explained:
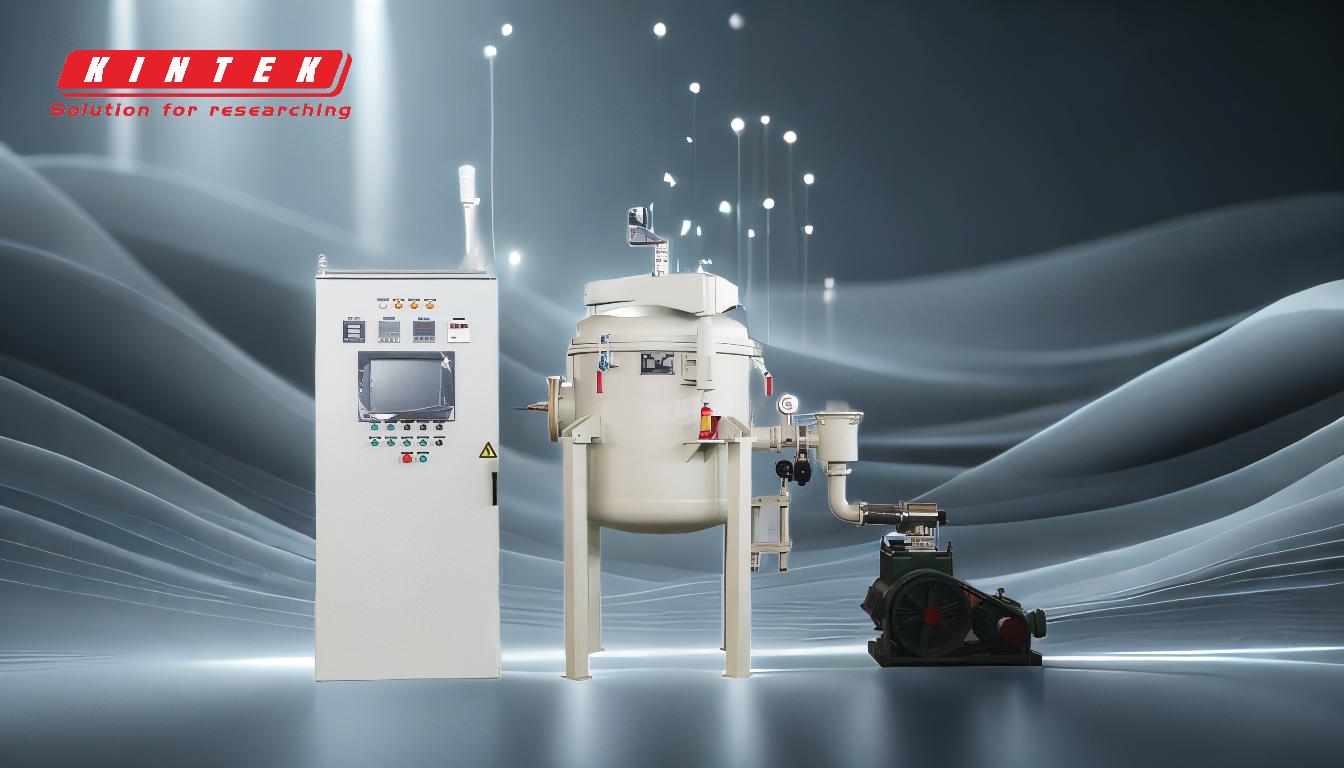
-
Melting and Alloy Production
- Graphite furnaces are widely used for melting metals and creating alloys.
- The controlled environment prevents oxidation, ensuring high-purity results.
- Applications include the production of specialized alloys for aerospace, automotive, and electronics industries.
-
Sintering and Heat Treatment
- Sintering involves compacting and forming solid materials using heat and pressure.
- Graphite furnaces are ideal for sintering metals, ceramics, and composites.
- Heat treatment processes like annealing and brazing are also performed to enhance material properties.
-
Graphitization and Carbonization
- Graphite furnaces are essential for converting carbon-based materials into graphite.
- Used in the production of graphite electrodes, carbon fibers, and other carbon-based products.
- The high-temperature environment ensures uniform graphitization.
-
Ceramic Firing and Degassing
- Ceramic materials are fired in graphite furnaces to achieve desired hardness and durability.
- Degassing removes impurities and trapped gases from materials, improving their quality.
- Applications include the production of advanced ceramics for electronics and industrial components.
-
Research and Development
- Graphite furnaces are used in laboratories for studying reaction kinetics at high temperatures and pressures.
- They are also employed in heating solid electrolytes for battery and fuel cell research.
- These applications support advancements in energy storage and material science.
-
Vacuum and Protective Atmosphere Processing
- Graphite furnaces operate in vacuum or inert gas environments to prevent contamination.
- This is critical for processing sensitive materials like semiconductors and high-purity metals.
- Applications include the production of optical fibers and advanced electronic components.
-
Industrial and Specialized Applications
- Graphite furnaces are used in foaming processes to create lightweight materials.
- They are also employed in test facilities for simulating extreme conditions.
- Industries such as aerospace, automotive, and renewable energy rely on these furnaces for specialized material processing.
In summary, graphite furnaces are indispensable tools for high-temperature material processing, offering precise control and versatility. Their applications range from industrial manufacturing to cutting-edge research, making them a cornerstone of modern material science and engineering.
Summary Table:
Application | Key Benefits |
---|---|
Melting and Alloy Production | High-purity results, oxidation prevention, specialized alloy creation. |
Sintering and Heat Treatment | Enhanced material properties, ideal for metals, ceramics, and composites. |
Graphitization and Carbonization | Uniform graphitization, production of graphite electrodes and carbon fibers. |
Ceramic Firing and Degassing | Improved hardness, durability, and material quality. |
Research and Development | Supports reaction kinetics, energy storage, and material science advancements. |
Vacuum and Protective Atmosphere | Prevents contamination, ideal for semiconductors and high-purity metals. |
Industrial and Specialized Uses | Lightweight material creation, extreme condition simulation, and more. |
Unlock the potential of graphite furnaces for your applications—contact us today to learn more!