The grinding mechanism of a ball mill involves the use of impact, extrusion, and friction generated by grinding balls within the mill to reduce the size of materials. The mill operates by rotating on its axis, causing the balls to collide with the material and each other, breaking down the particles into finer sizes. Critical speed is essential for effective grinding, ensuring the balls rotate along the inner walls and apply sufficient force. Planetary ball mills further enhance this process by using centrifugal and Coriolis forces to accelerate grinding balls, resulting in more efficient and rapid particle size reduction.
Key Points Explained:
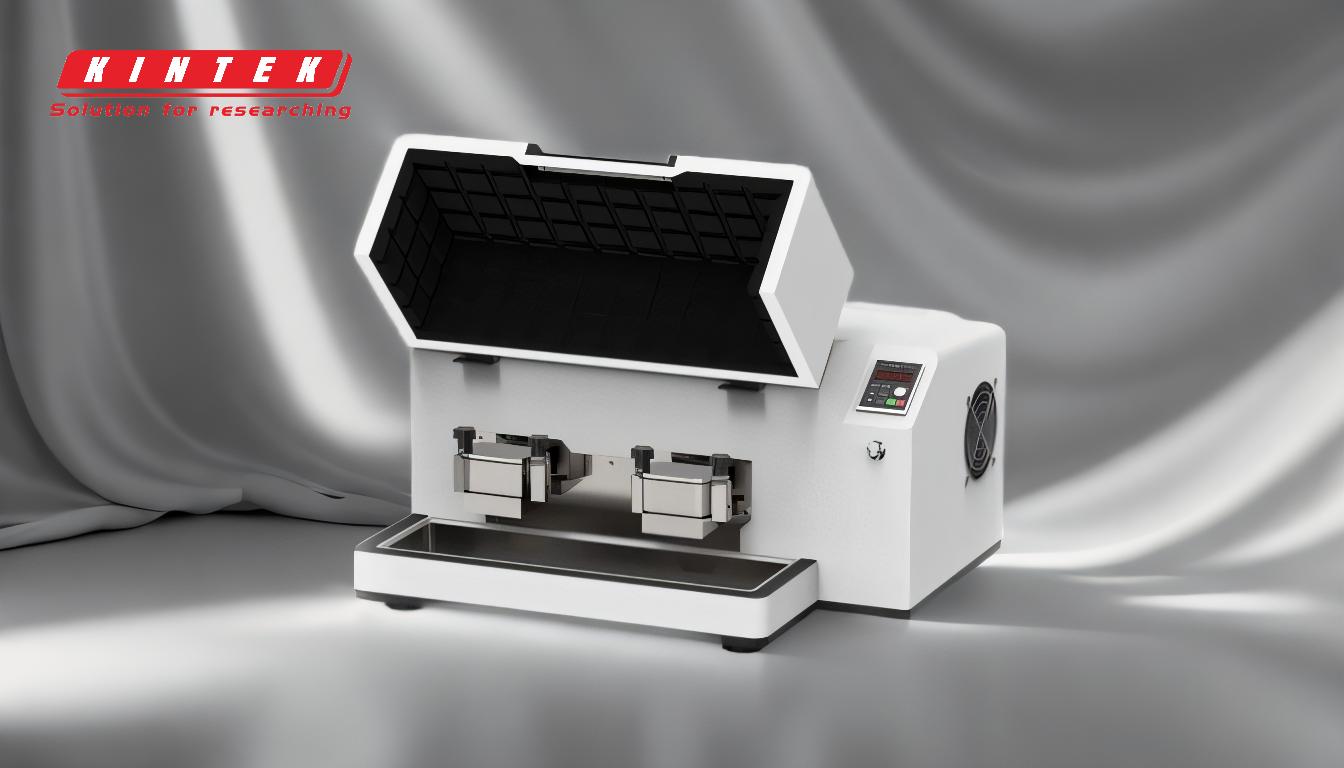
-
Principles of Grinding in Ball Mills:
- Impact: The grinding balls collide with the material and each other, exerting pressure that breaks down the particles.
- Attrition: Repeated collisions and rubbing between the balls and the material reduce the particle size through friction and wear.
- Extrusion: The material is compressed between the grinding balls and the mill walls, further aiding in size reduction.
-
Role of Rotation and Critical Speed:
- The ball mill rotates on either a vertical or horizontal axis, causing the grinding balls to move and collide with the material.
- Critical Speed: This is the minimum speed required for the balls to rotate along the inner walls of the mill. Achieving this speed ensures that the balls apply sufficient force to grind the material effectively. If the speed is too low, the balls will not lift and fall, reducing grinding efficiency. If too high, centrifugal force may keep the balls pinned to the walls, also reducing grinding effectiveness.
-
Movement of Grinding Elements:
- The grinding balls travel at different velocities within the mill, leading to varying collision forces and directions.
- This movement generates kinetic energy, which is transferred to the material upon impact, breaking it down into smaller particles.
- Frictional wear and rubbing forces also act on the particles, contributing to the grinding process.
-
Planetary Ball Mills:
- These mills use jars and grinding media mounted on a circular platform called a sun wheel.
- As the sun wheel rotates, each jar rotates on its own axis in the opposite direction, creating centrifugal and Coriolis forces.
- These forces accelerate the grinding balls, increasing their impact energy and enhancing the grinding efficiency compared to traditional ball mills.
-
Factors Influencing Grinding Efficiency:
- Ball Size and Density: Larger or denser balls can exert more force, but too large may reduce the number of collisions.
- Mill Speed: Must be optimized to achieve critical speed without causing excessive centrifugal force.
- Material Properties: Hardness, brittleness, and initial particle size of the material affect how easily it can be ground.
- Filling Ratio: The proportion of the mill volume filled with grinding balls and material. An optimal ratio ensures sufficient collisions without overcrowding.
-
Applications and Advantages:
- Ball mills are widely used in industries such as mining, ceramics, and pharmaceuticals for grinding materials into fine powders.
- They are versatile, capable of grinding a wide range of materials, and can operate continuously or in batch mode.
- Planetary ball mills offer higher energy input and finer grinding, making them suitable for advanced material processing and nanotechnology applications.
By understanding these key points, a purchaser can make informed decisions about selecting the appropriate type of ball mill, optimizing operating conditions, and ensuring efficient and effective grinding for their specific needs.
Summary Table:
Key Aspect | Description |
---|---|
Grinding Principles | Impact, attrition, and extrusion break down materials into finer particles. |
Critical Speed | Ensures grinding balls rotate effectively, balancing force and efficiency. |
Planetary Ball Mills | Use centrifugal and Coriolis forces for faster, more efficient grinding. |
Influencing Factors | Ball size, mill speed, material properties, and filling ratio affect grinding. |
Applications | Used in mining, ceramics, pharmaceuticals, and nanotechnology for fine grinding. |
Optimize your grinding process with the right ball mill—contact our experts today for tailored solutions!