PVD (Physical Vapor Deposition) coatings are known for their high hardness, which typically ranges between 1500 HV (Vickers Hardness) and 4500 HV, depending on the type of coating, substrate material, and PVD method used. For comparison, carbon steels have a hardness of around 250 HV, while nitrided or nickel/chrome-plated steels range between 600 HV and 1000 HV. PVD coatings, such as TiN (Titanium Nitride), are particularly valued for their ability to enhance wear resistance, corrosion resistance, and durability. In some cases, specialized coatings like DLC (Diamond-Like Carbon) can achieve hardness values as high as 9000 HV. The hardness of PVD coatings is a critical factor in their performance, making them suitable for demanding applications in industries like automotive, aerospace, and medical.
Key Points Explained:
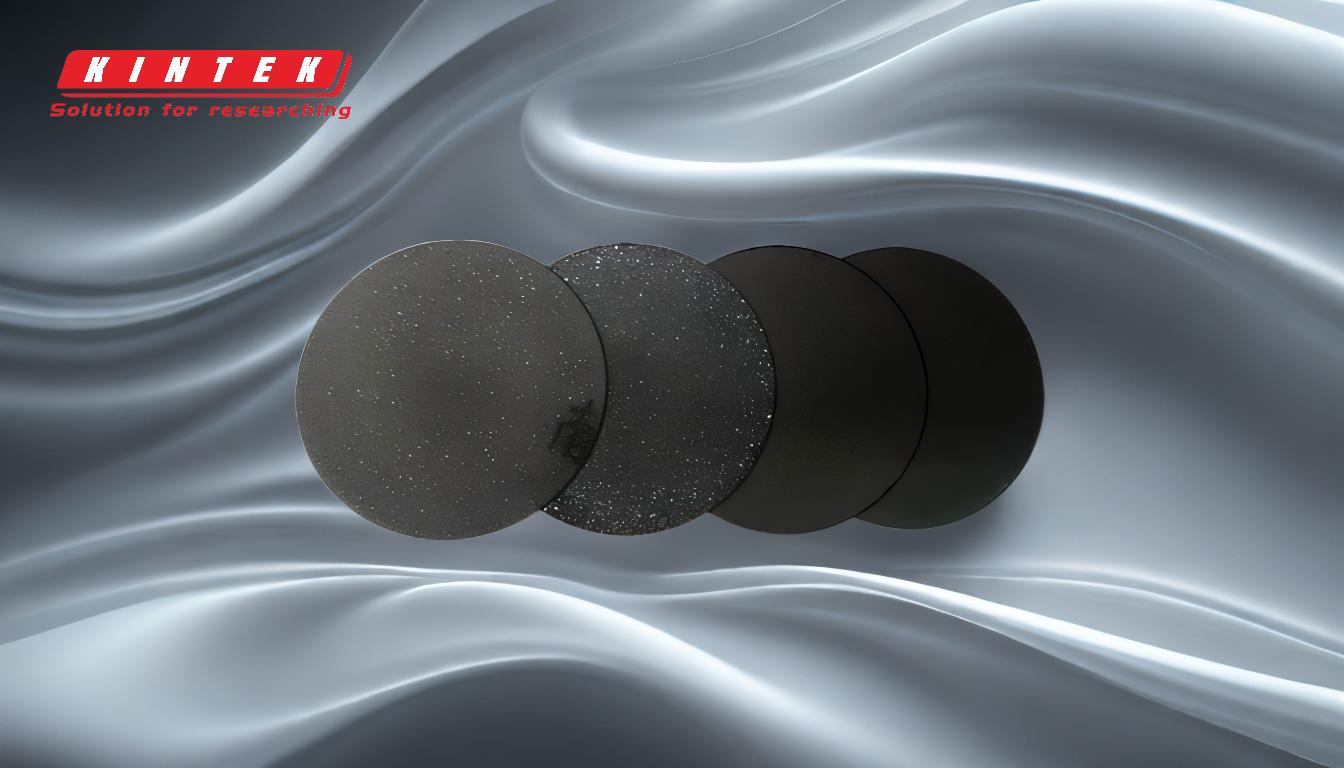
-
Hardness Range of PVD Coatings:
- PVD coatings typically have a hardness range of 1500 HV to 4500 HV, depending on the specific coating material and process.
- For reference, 900 HV corresponds to 67 HRC (Rockwell C), which is significantly harder than many common materials like carbon steel (250 HV) or nitrided steels (600–1000 HV).
- Specialized coatings, such as DLC (Diamond-Like Carbon), can achieve even higher hardness values, reaching up to 9000 HV.
-
Factors Influencing Hardness:
- The hardness of PVD coatings depends on several factors:
- Coating Material: Different materials (e.g., TiN, TiCN, CrN, DLC) have varying hardness levels.
- Substrate Material: The underlying material can influence the coating's properties. For example, TiN coatings on Ti-6Al-4V alloy improve fatigue limits and endurance.
- PVD Method: The specific PVD process (e.g., sputtering, arc evaporation) and operator skills can affect the coating's hardness.
- Thickness: PVD coatings are very thin (0.5–5 microns), but their hardness is optimized for performance.
- The hardness of PVD coatings depends on several factors:
-
Comparison with Other Materials:
- Carbon Steels: Typically have a hardness of around 250 HV (25 HRC).
- Nitrided or Nickel/Chrome-Plated Steels: Range between 600 HV and 1000 HV.
- PVD Coatings: At 1500–4500 HV, PVD coatings are significantly harder, making them ideal for applications requiring high wear resistance and durability.
-
Applications and Benefits:
- PVD coatings are widely used in industries such as automotive, aerospace, and medical due to their high hardness, wear resistance, and corrosion resistance.
- They also provide low friction and enhanced aesthetic appearance, making them suitable for both functional and decorative purposes.
-
Hardness and Wear Resistance:
- While high hardness generally correlates with improved wear resistance, there is no direct relationship between the two. Hardness values above the optimum threshold can indicate decarburization, which may reduce performance.
- PVD coatings strike a balance between hardness and other properties like toughness and adhesion to ensure long-term durability.
-
Specialized Coatings:
- DLC Coatings: These are among the hardest PVD coatings, with hardness values reaching up to 9000 HV. They are particularly valued for their low friction and excellent wear resistance.
- TiN Coatings: Commonly used for their gold-like appearance and high hardness, they are ideal for cutting tools, molds, and decorative applications.
-
Hardness Measurement:
- Hardness is typically measured using the Vickers Hardness (HV) scale, which is suitable for thin coatings. For comparison, Rockwell C (HRC) is also used, with 900 HV equivalent to 67 HRC.
-
Optimum Hardness and Corrosion Resistance:
- PVD coatings achieve an optimum hardness level that enhances their corrosion resistance. Excessive hardness can lead to the formation of hard phases, which may compromise performance.
In summary, the hardness of PVD coatings is a key property that makes them highly durable and suitable for demanding applications. Their hardness ranges from 1500 HV to 4500 HV, with specialized coatings like DLC reaching up to 9000 HV. This exceptional hardness, combined with wear resistance, corrosion resistance, and low friction, makes PVD coatings invaluable across various industries.
Summary Table:
Aspect | Details |
---|---|
Hardness Range | 1500–4500 HV (up to 9000 HV for DLC coatings) |
Comparison Materials | Carbon steel: 250 HV; Nitrided steels: 600–1000 HV |
Key Benefits | High wear resistance, corrosion resistance, low friction, and durability |
Applications | Automotive, aerospace, medical, and decorative uses |
Specialized Coatings | TiN (Titanium Nitride), DLC (Diamond-Like Carbon) |
Measurement | Vickers Hardness (HV); 900 HV = 67 HRC |
Learn how PVD coatings can enhance your materials' performance—contact our experts today!