Injection molding machines are crucial in modern manufacturing due to their ability to produce highly complex and uniform parts at scale. They enable the creation of millions of virtually identical components, which is essential for industries requiring precision and consistency. The process is highly efficient, cost-effective for large production runs, and versatile in handling a wide range of materials. By optimizing design elements, manufacturers can enhance part quality, reduce waste, and improve production efficiency. Injection molding machines are indispensable for industries like automotive, electronics, medical devices, and consumer goods, where high-volume production and precision are paramount.
Key Points Explained:
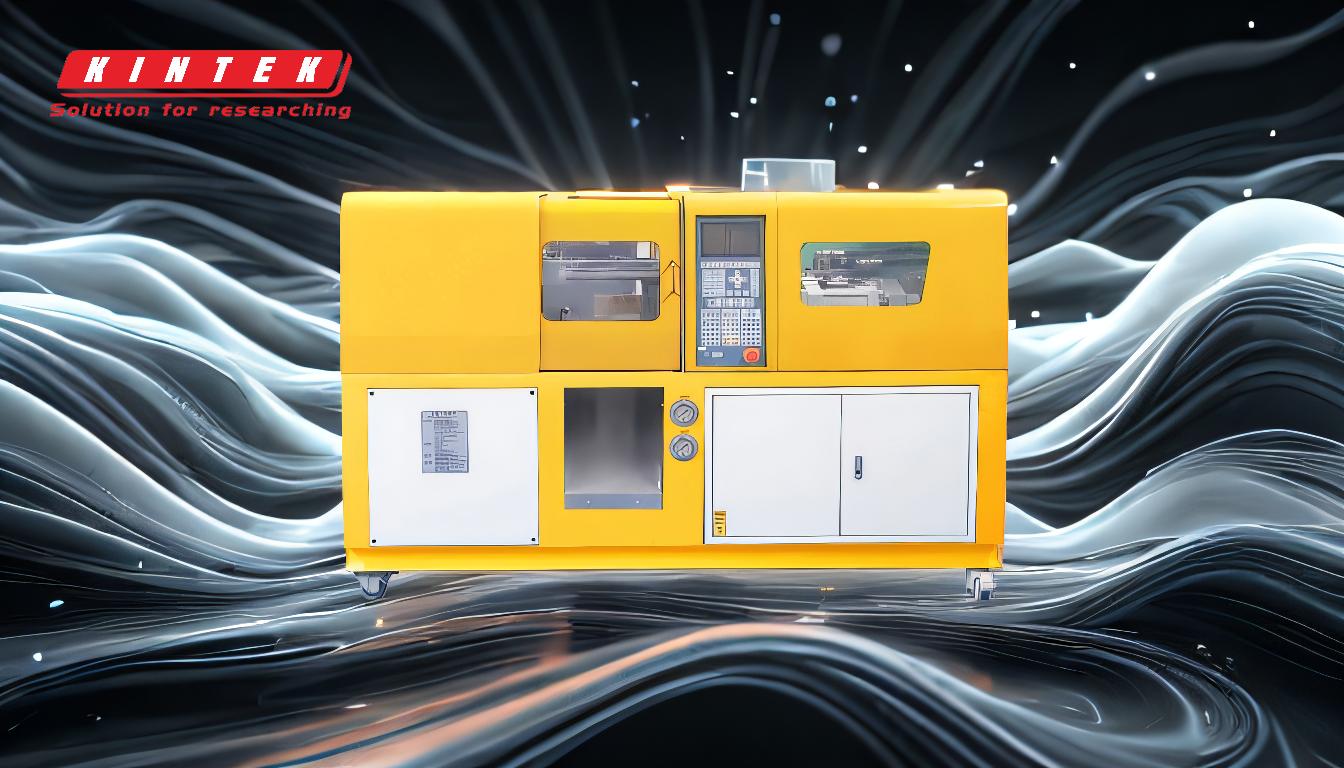
-
Ability to Produce Complex Parts
- Injection molding machines excel at creating parts with intricate geometries, thin walls, and fine details.
- This capability is vital for industries like electronics and medical devices, where components often have complex shapes and tight tolerances.
- The process allows for the integration of multiple features into a single part, reducing the need for assembly and secondary operations.
-
Uniformity and Consistency
- Injection molding ensures that every part produced is virtually identical, which is critical for maintaining quality and functionality in mass production.
- This uniformity is achieved through precise control of temperature, pressure, and cooling rates during the molding process.
- Consistency is particularly important in industries like automotive and aerospace, where even minor deviations can lead to significant performance issues.
-
High-Volume Production
- Injection molding is ideal for producing large quantities of parts quickly and efficiently.
- The process is highly automated, reducing labor costs and minimizing human error.
- High-volume production capabilities make it cost-effective for industries requiring millions of parts, such as consumer goods and packaging.
-
Material Versatility
- Injection molding machines can process a wide range of materials, including thermoplastics, thermosets, and elastomers.
- This versatility allows manufacturers to choose materials that meet specific performance requirements, such as strength, flexibility, or heat resistance.
- Advanced materials, such as biodegradable plastics and composites, can also be used, supporting sustainability and innovation.
-
Cost Efficiency
- While the initial tooling costs for injection molding can be high, the per-unit cost decreases significantly with large production volumes.
- The process minimizes material waste, as excess plastic can often be recycled and reused.
- Automation and reduced labor requirements further contribute to cost savings over time.
-
Design Optimization and Precision
- Key design elements, such as wall thickness, gate placement, and draft angles, can be optimized to enhance part quality and reduce defects.
- Advanced software and simulation tools allow manufacturers to predict and address potential issues before production begins.
- Precision in design and manufacturing ensures that parts meet stringent quality standards and perform reliably in their intended applications.
-
Applications Across Industries
- Injection molding is widely used in industries such as automotive, electronics, medical devices, consumer goods, and packaging.
- In the automotive industry, it is used to produce components like dashboards, bumpers, and interior trim.
- In electronics, it is used for housings, connectors, and other precision parts.
- Medical devices benefit from the ability to produce sterile, biocompatible components with high precision.
-
Sustainability and Innovation
- Injection molding supports sustainability by enabling the use of recycled and biodegradable materials.
- The process itself is energy-efficient, especially when compared to traditional manufacturing methods.
- Innovations in materials and molding techniques continue to expand the possibilities for creating lightweight, durable, and eco-friendly products.
By leveraging the capabilities of injection molding machines, manufacturers can achieve high-quality, cost-effective production while meeting the demands of modern industries. The importance of these machines lies in their ability to combine precision, efficiency, and versatility, making them a cornerstone of advanced manufacturing.
Summary Table:
Key Benefits | Details |
---|---|
Complex Parts Production | Creates intricate geometries, thin walls, and fine details. |
Uniformity and Consistency | Produces identical parts with precise control of temperature and pressure. |
High-Volume Production | Ideal for large-scale, automated production with minimal labor costs. |
Material Versatility | Handles thermoplastics, thermosets, elastomers, and advanced materials. |
Cost Efficiency | Low per-unit cost for large runs, minimizes waste, and supports recycling. |
Design Optimization | Enhances part quality through advanced software and precision engineering. |
Applications | Widely used in automotive, electronics, medical devices, and consumer goods. |
Sustainability | Supports eco-friendly materials and energy-efficient processes. |
Ready to optimize your production with injection molding? Contact us today to learn more!