Thermal evaporation is a vacuum deposition technique used to create thin films by heating a material until it evaporates in a vacuum chamber. The evaporated atoms or molecules then travel through the vacuum and deposit onto a substrate, forming a uniform coating. This process is one of the oldest and simplest forms of physical vapor deposition (PVD). It is widely used in industries such as electronics, optics, and solar energy to deposit metals like silver and aluminum for applications such as OLEDs, solar cells, and thin-film transistors. The method relies on resistive heating, where an electric current heats a boat, coil, or basket containing the target material, causing it to melt and evaporate. The resulting vapor stream coats the substrate, creating a thin film with precise control over thickness and composition.
Key Points Explained:
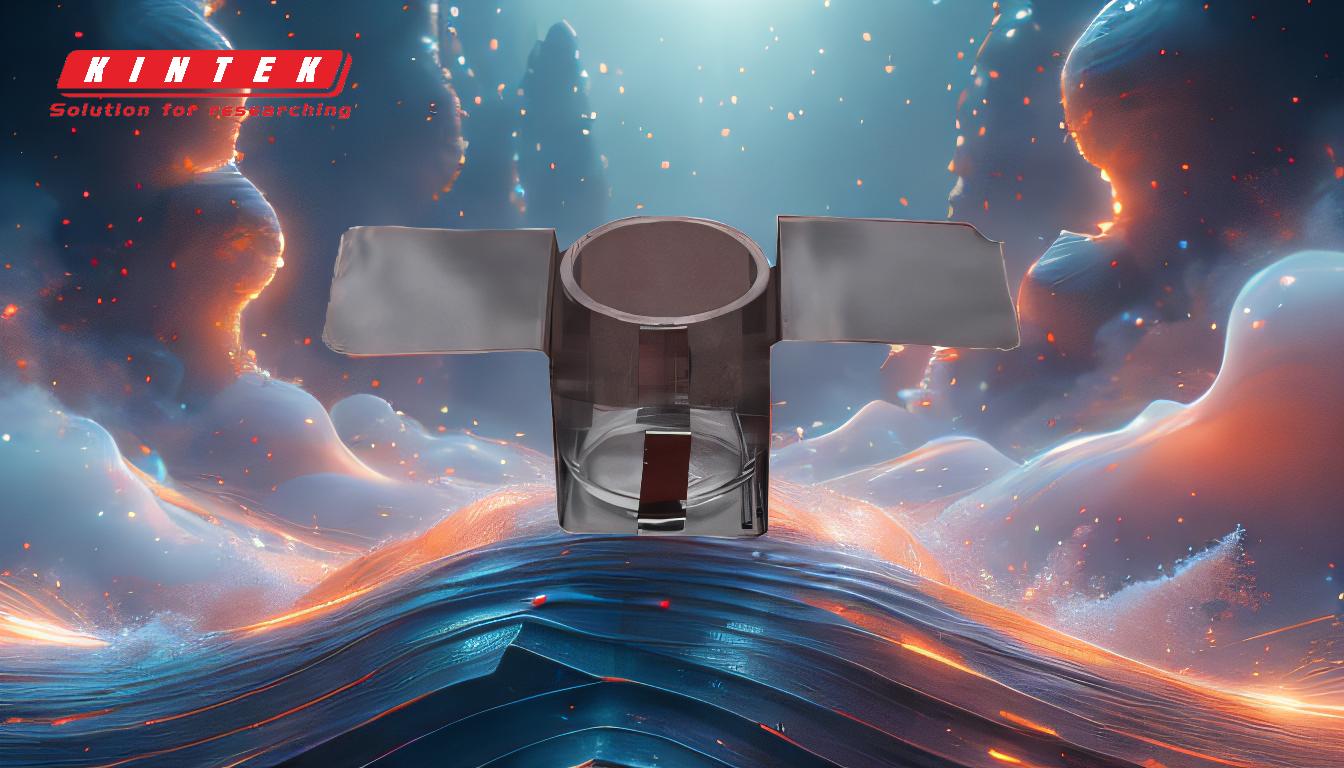
-
Definition and Basic Principle of Thermal Evaporation:
- Thermal evaporation is a physical vapor deposition (PVD) technique where a material is heated in a high-vacuum environment until it evaporates. The evaporated atoms or molecules travel through the vacuum and deposit onto a substrate, forming a thin film.
- The process relies on the principle of vapor pressure: when a material is heated to its evaporation point, it produces a vapor stream that condenses on the substrate.
-
Components of the Thermal Evaporation System:
- Vacuum Chamber: A sealed environment with low pressure to minimize contamination and allow the vaporized material to travel unimpeded.
- Evaporation Source: Typically a resistance boat, coil, or basket made of materials like tungsten or molybdenum. The source holds the target material and is heated by passing an electric current through it.
- Substrate: The surface onto which the evaporated material is deposited. It is positioned above the evaporation source to ensure uniform coating.
- Power Supply: Provides the electric current needed to heat the evaporation source.
-
Process Steps:
- Material Loading: The target material (e.g., metal pellets) is placed in the evaporation source.
- Vacuum Creation: The chamber is evacuated to achieve a high vacuum, reducing the presence of air molecules that could interfere with the vapor stream.
- Heating: An electric current is passed through the evaporation source, heating it to the point where the target material melts and evaporates.
- Deposition: The vaporized material travels through the vacuum and deposits onto the substrate, forming a thin film.
- Cooling: After deposition, the system is allowed to cool, and the substrate is removed.
-
Applications of Thermal Evaporation:
- Electronics: Used to deposit metals like silver and aluminum for OLEDs, thin-film transistors, and other electronic components.
- Optics: Applied in the production of reflective coatings, anti-reflective coatings, and optical filters.
- Solar Energy: Utilized to create thin-film solar cells and other photovoltaic devices.
- Decorative Coatings: Used to apply metallic finishes on consumer products.
-
Advantages of Thermal Evaporation:
- Simplicity: It is one of the simplest and most cost-effective PVD methods.
- High Purity: The vacuum environment minimizes contamination, resulting in high-purity films.
- Precision: Allows for precise control over film thickness and composition.
- Versatility: Can deposit a wide range of materials, including metals, alloys, and some compounds.
-
Limitations of Thermal Evaporation:
- Material Restrictions: Some materials, such as those with very high melting points, are difficult to evaporate using this method.
- Uniformity Challenges: Achieving uniform coatings on complex or large substrates can be difficult.
- Thermal Stress: The high temperatures involved can cause thermal stress in the substrate or evaporation source.
-
Comparison with Other PVD Techniques:
- Sputtering: Unlike thermal evaporation, sputtering uses energetic ions to dislodge atoms from a target material. Sputtering can deposit a wider range of materials, including insulators, but is more complex and expensive.
- Electron Beam Evaporation: This method uses an electron beam to heat the target material, allowing for higher evaporation temperatures and better control over the deposition process. However, it is more expensive and complex than thermal evaporation.
-
Key Considerations for Equipment and Consumable Purchasers:
- Material Compatibility: Ensure the evaporation source and chamber materials are compatible with the target material.
- Vacuum System Quality: A high-quality vacuum system is critical for achieving low contamination and consistent results.
- Heating Source Design: The design of the boat, coil, or basket should match the target material's properties and the desired deposition rate.
- Substrate Handling: Consider the size, shape, and thermal sensitivity of the substrate when selecting equipment.
By understanding these key points, purchasers of thermal evaporation equipment and consumables can make informed decisions that align with their specific application needs.
Summary Table:
Aspect | Details |
---|---|
Definition | A PVD technique where materials are heated in a vacuum to form thin films. |
Key Components | Vacuum chamber, evaporation source, substrate, power supply. |
Process Steps | Material loading, vacuum creation, heating, deposition, cooling. |
Applications | Electronics (OLEDs, thin-film transistors), optics, solar energy, coatings. |
Advantages | Simplicity, high purity, precision, versatility. |
Limitations | Material restrictions, uniformity challenges, thermal stress. |
Comparison with PVD | Simpler and more cost-effective than sputtering or electron beam methods. |
Purchasing Tips | Consider material compatibility, vacuum quality, and substrate handling. |
Ready to enhance your thin-film deposition process? Contact us today for expert guidance and equipment solutions!