The mechanism of graphene growth in Chemical Vapor Deposition (CVD) involves a series of well-defined steps, starting from the introduction of gaseous reactants to the formation of a stable graphene layer on a substrate. The process is influenced by factors such as the type of substrate, growth conditions, and the properties of the catalyst. CVD is particularly effective for producing high-quality, monolayer graphene over large areas, making it a preferred method for industrial applications. The growth mechanism varies depending on the carbon solubility of the substrate, with metals like nickel and copper playing crucial roles due to their differing carbon absorption and surface adsorption properties.
Key Points Explained:
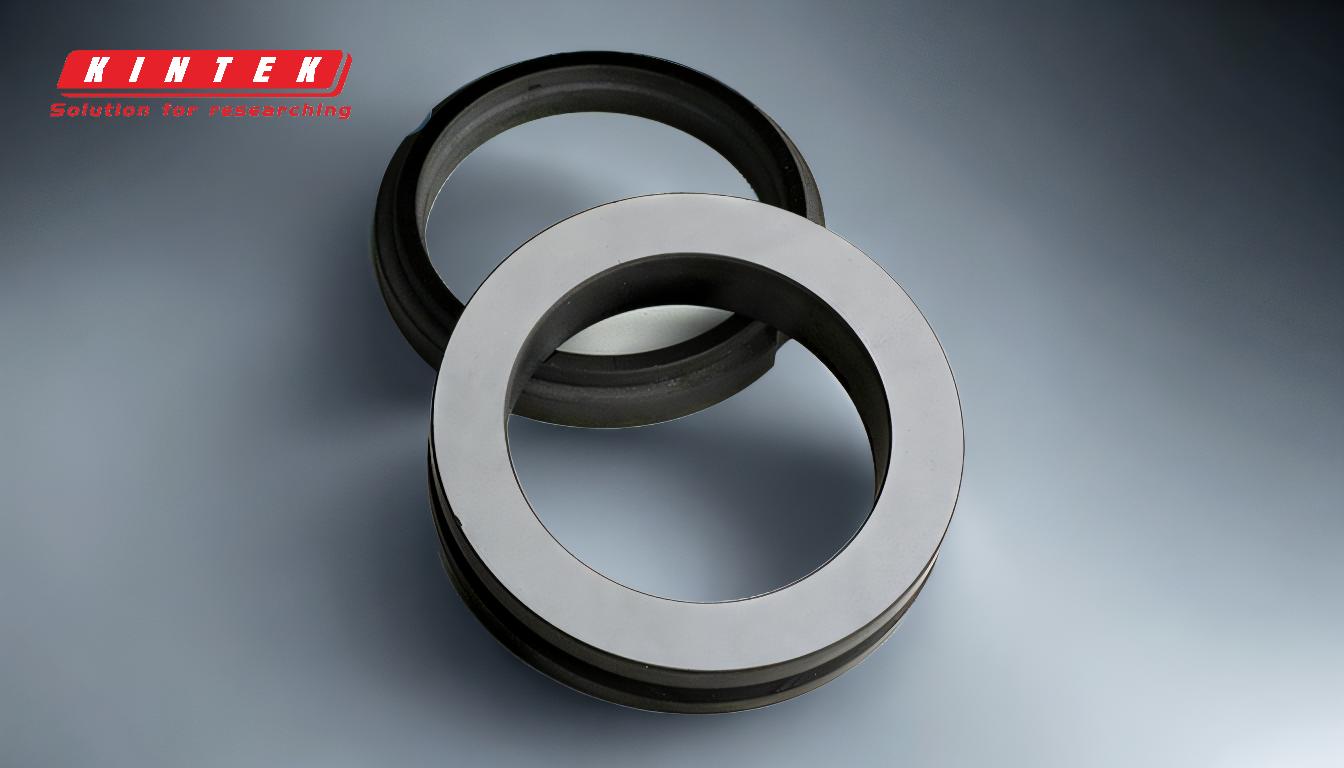
-
Introduction of Gaseous Reactants:
- In the CVD process, gaseous reactants, typically a hydrocarbon gas like methane, are introduced into the reaction chamber. These gases are transported to the substrate surface through convection or diffusion.
-
Activation and Chemical Reactions:
- The energy required for the chemical reactions is supplied by heat, light, or electric discharge. This energy activates the gaseous reactants, leading to the formation of reactive species and by-products in the gas phase.
-
Transport to Substrate Surface:
- The reactive species diffuse through a boundary layer and reach the substrate surface. This step is crucial as it determines the availability of reactants for the subsequent surface reactions.
-
Adsorption on Substrate:
- Once the reactants reach the substrate, they undergo chemical and physical adsorption. The nature of adsorption depends on the substrate's properties, such as its crystallinity, surface roughness, and carbon solubility.
-
Surface-Catalyzed Reactions:
- The adsorbed species participate in heterogeneous surface reactions, facilitated by the catalyst (often a transition metal like nickel or copper). These reactions lead to the formation of carbon atoms, which are the building blocks of graphene.
-
Nucleation and Growth:
- The carbon atoms diffuse on the substrate surface and aggregate at growth sites, leading to the nucleation of graphene. The growth of graphene layers is influenced by factors such as temperature, pressure, precursor flux, and the properties of the catalyst.
-
Desorption and Removal of By-products:
- Volatile by-products formed during the reactions desorb from the substrate surface and are transported away from the reaction zone through diffusion and convection. This step ensures the purity and quality of the graphene film.
-
Role of Substrate Carbon Solubility:
- The mechanism of graphene growth varies with the carbon solubility of the substrate. In metals with high carbon solubility (e.g., nickel), carbon atoms diffuse into the substrate and segregate upon cooling, forming graphene. In contrast, in metals with low carbon solubility (e.g., copper), graphene growth occurs primarily through surface adsorption.
-
Influence of Synthesis Conditions:
- The number of graphene layers, their quality, and the growth rate are highly dependent on synthesis conditions such as growth time, temperature, cooling rate, and the thickness of the substrate film. Optimal conditions are essential for producing high-quality monolayer graphene.
-
Catalyst Properties:
- The choice of catalyst significantly impacts the graphene growth process. Transition metals are commonly used due to their cost-effectiveness and favorable catalytic properties. The crystallinity, composition, and surface roughness of the catalyst influence the nucleation and growth of graphene.
By understanding these key points, one can appreciate the complexity and precision required in the CVD process for graphene synthesis. Each step must be carefully controlled to achieve the desired quality and properties of the graphene film.
Summary Table:
Step | Description |
---|---|
1. Introduction of Gaseous Reactants | Hydrocarbon gases like methane are introduced into the reaction chamber. |
2. Activation and Chemical Reactions | Energy activates reactants, forming reactive species and by-products in the gas phase. |
3. Transport to Substrate Surface | Reactive species diffuse through a boundary layer to reach the substrate surface. |
4. Adsorption on Substrate | Reactants undergo chemical and physical adsorption, influenced by substrate properties. |
5. Surface-Catalyzed Reactions | Adsorbed species react on the catalyst surface, forming carbon atoms for graphene growth. |
6. Nucleation and Growth | Carbon atoms aggregate at growth sites, forming graphene layers under controlled conditions. |
7. Desorption and By-product Removal | Volatile by-products desorb and are removed, ensuring graphene purity. |
8. Role of Substrate Carbon Solubility | Growth mechanism varies with substrate carbon solubility (e.g., nickel vs. copper). |
9. Influence of Synthesis Conditions | Growth rate, quality, and layers depend on temperature, pressure, and precursor flux. |
10. Catalyst Properties | Catalyst choice (e.g., nickel, copper) impacts nucleation, growth, and graphene quality. |
Unlock the potential of high-quality graphene for your applications—contact our experts today to learn more!