A grinding machine operates by using abrasive particles or grinding media to remove material from a workpiece through abrasion. The process involves rotating abrasive wheels or grinding media that come into contact with the workpiece, causing surface deformation and fragmentation. This mechanism allows for shaping, smoothing, or finishing the workpiece. The grinding process is highly versatile and can be adapted for various materials and applications, depending on the type of grinding media and machine configuration used. The key to its effectiveness lies in the interaction between the abrasive surface and the workpiece, which ensures precise material removal and surface refinement.
Key Points Explained:
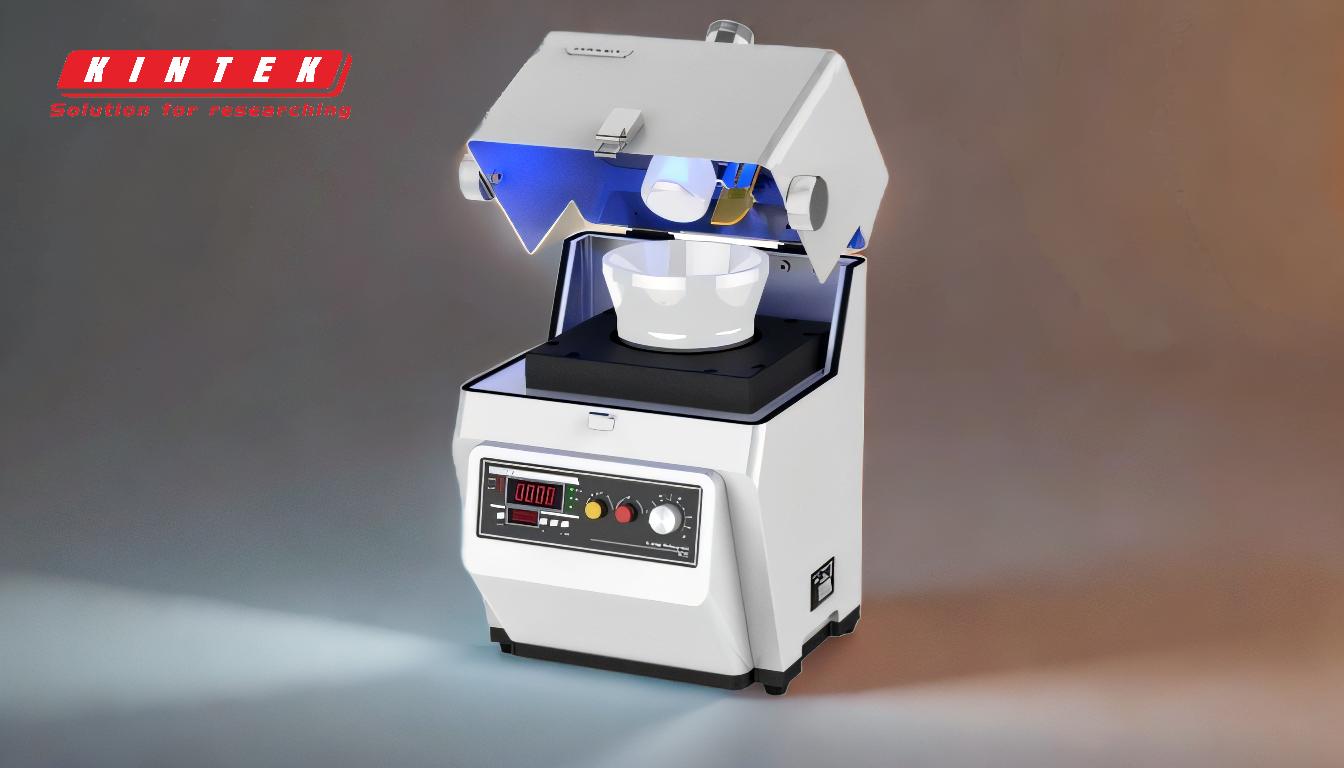
-
Material Removal via Abrasion:
- Grinding machines remove material from a workpiece through abrasion, which involves the use of abrasive particles or grinding media. This process is distinct from other machining methods like cutting or drilling, as it relies on the friction and shear forces generated by the abrasive surface.
- The abrasive particles are typically embedded in a rotating wheel or grinding media, which is brought into contact with the workpiece. As the wheel rotates, the abrasive particles grind away the surface of the workpiece, resulting in precise material removal.
-
Role of Rotating Abrasive Wheels:
- The rotating abrasive wheel is a critical component of the grinding machine. It is made up of abrasive grains bonded together to form a solid, durable surface. The wheel's rotation generates the necessary force to remove material from the workpiece.
- The speed and direction of the wheel's rotation can be adjusted to control the rate of material removal and the surface finish. Higher speeds generally result in faster material removal but may require more precise control to avoid overheating or damaging the workpiece.
-
Interaction Between Grinding Media and Workpiece:
- The grinding media, such as ball milling media or sanding media, plays a crucial role in the grinding process. When the workpiece comes into contact with the grinding media, the surface of the material deforms and fragments, leading to the desired grinding and mixing effects.
- The size, shape, and hardness of the grinding media can be tailored to the specific requirements of the workpiece and the desired outcome. For example, finer grinding media may be used for achieving a smooth surface finish, while coarser media may be used for more aggressive material removal.
-
Surface Deformation and Fragmentation:
- As the grinding media interacts with the workpiece, the surface of the material undergoes deformation and fragmentation. This process is essential for achieving the desired shape, smoothness, or finish on the workpiece.
- The deformation and fragmentation occur at a microscopic level, with the abrasive particles creating tiny chips or fragments of material that are removed from the workpiece. This process is highly controlled, allowing for precise material removal and surface refinement.
-
Versatility and Applications:
- Grinding machines are highly versatile and can be used for a wide range of applications, including shaping, smoothing, and finishing workpieces made from various materials such as metal, wood, ceramics, and plastics.
- The ability to adjust the grinding parameters, such as the speed of the abrasive wheel, the type of grinding media, and the pressure applied, makes grinding machines suitable for both rough grinding and fine finishing tasks.
-
Precision and Control:
- One of the key advantages of grinding machines is their ability to achieve high levels of precision and control. The grinding process can be finely tuned to remove very small amounts of material, allowing for the creation of highly accurate and detailed workpieces.
- This precision is particularly important in industries such as aerospace, automotive, and medical device manufacturing, where even minor deviations from the desired specifications can have significant consequences.
-
Heat Generation and Management:
- The grinding process generates heat due to the friction between the abrasive particles and the workpiece. Excessive heat can lead to thermal damage, such as warping or cracking, especially in heat-sensitive materials.
- To manage heat generation, grinding machines often incorporate cooling systems, such as coolant fluids or air jets, to dissipate heat and prevent damage to the workpiece. Proper heat management is essential for maintaining the quality and integrity of the finished product.
-
Types of Grinding Machines:
- There are several types of grinding machines, each designed for specific applications. Common types include surface grinders, cylindrical grinders, centerless grinders, and tool and cutter grinders.
- Surface grinders are used for flat surfaces, cylindrical grinders for cylindrical or conical surfaces, centerless grinders for high-volume production of cylindrical components, and tool and cutter grinders for sharpening and shaping cutting tools.
In summary, the mechanism of a grinding machine involves the use of rotating abrasive wheels or grinding media to remove material from a workpiece through abrasion. The process is highly versatile, allowing for precise material removal and surface refinement, and can be adapted for a wide range of applications. Key factors such as the type of grinding media, the speed of the abrasive wheel, and heat management play a crucial role in determining the effectiveness and quality of the grinding process.
Summary Table:
Key Aspect | Description |
---|---|
Material Removal | Abrasive particles grind away material through friction and shear forces. |
Rotating Abrasive Wheels | Critical for generating force; speed and direction control material removal. |
Grinding Media Interaction | Tailored media size, shape, and hardness ensure desired surface finish. |
Surface Deformation | Microscopic fragmentation achieves precise shaping and smoothing. |
Versatility | Suitable for metals, wood, ceramics, and plastics across various applications. |
Precision & Control | High accuracy for industries like aerospace, automotive, and medical devices. |
Heat Management | Cooling systems prevent thermal damage during grinding. |
Types of Machines | Includes surface, cylindrical, centerless, and tool and cutter grinders. |
Discover the right grinding machine for your needs—contact our experts today!