A ball mill operates on the principles of impact and attrition, which are the primary mechanisms for grinding materials into fine particles. The machine consists of a horizontally or vertically mounted rotating cylinder filled with grinding media, typically steel balls or rods. As the cylinder rotates, the balls are lifted and then cascade down, striking the material and breaking it down through impact forces. Simultaneously, the rolling and sliding motion of the balls against the material and each other causes attrition, further reducing the particle size. The efficiency of the grinding process depends on achieving the critical speed, where the balls rotate along the inner walls of the cylinder, ensuring optimal impact and friction. Additionally, Coriolis forces and the interplay between frictional and impact forces contribute to the high dynamic energy required for effective grinding.
Key Points Explained:
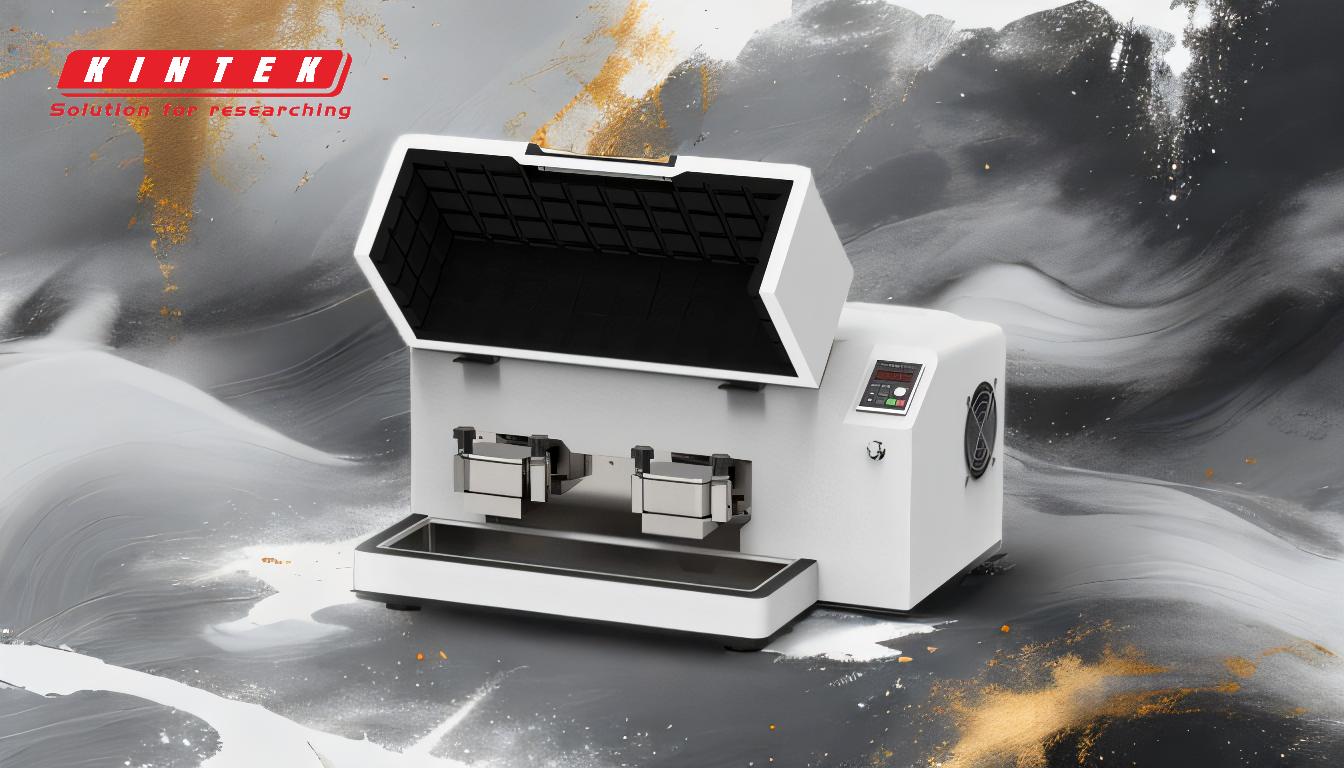
-
Principle of Operation:
- The ball mill operates on two primary mechanisms: impact and attrition.
- Impact: This occurs when fast-moving grinding balls strike the material, applying pressure and breaking it into smaller particles.
- Attrition: This involves the gradual reduction of particle size as the material is ground by the rolling and sliding motion of the balls against each other and the material.
- The ball mill operates on two primary mechanisms: impact and attrition.
-
Structure of a Ball Mill:
- The ball mill consists of a rotating cylinder, which can be mounted either horizontally or vertically.
- The cylinder contains grinding media, such as steel balls or rods, which are responsible for the grinding action.
- The rotation of the cylinder causes the balls to be lifted and then cascade down, creating the necessary forces for grinding.
-
Critical Speed:
- The efficiency of a ball mill depends on achieving the critical speed, which is the rotational speed at which the balls begin to rotate along the inner walls of the cylinder.
- At critical speed, the balls are lifted to the highest point before cascading down, ensuring maximum impact and friction for effective grinding.
-
Grinding Media:
- The grinding media (balls or rods) play a crucial role in the grinding process.
- Larger balls are effective for breaking down coarse materials, while smaller balls reduce void spaces and produce finer particles.
-
Coriolis Forces and Dynamic Energy:
- The grinding balls are subjected to Coriolis forces, which result from the superimposed rotational movements of the balls and the grinding jar.
- The difference in speeds between the balls and the grinding jar creates an interaction between frictional and impact forces, releasing high dynamic energies that enhance the grinding process.
-
Types of Ball Mills:
- Horizontal Ball Mills: These are the most common type, with the cylinder rotating on a horizontal axis. The grinding balls are tossed around the cylinder, smashing into the material to be ground.
- Vertical Ball Mills: These operate on a vertical axis and are less common. They function similarly to horizontal mills but are typically used for specific applications.
- Vibrating Ball Mills: These use mechanical vibrations to drive the grinding balls, providing additional kinetic energy for grinding.
-
Applications of Ball Mills:
- Ball mills are widely used in industries such as mining, ceramics, pharmaceuticals, and materials science for grinding and blending materials.
- They are capable of producing fine and ultra-fine powders, making them essential for processes requiring precise particle size reduction.
-
Advantages of Ball Mills:
- Versatility: Ball mills can grind a wide range of materials, from soft to hard substances.
- Efficiency: The combination of impact and attrition ensures efficient grinding, even for tough materials.
- Scalability: Ball mills are available in various sizes, making them suitable for both laboratory and industrial applications.
-
Limitations of Ball Mills:
- Energy Consumption: Ball mills can be energy-intensive, especially when operating at high speeds.
- Wear and Tear: The grinding media and the mill lining are subject to wear, requiring regular maintenance and replacement.
- Noise and Vibration: The operation of ball mills can generate significant noise and vibration, which may require additional mitigation measures.
-
Future Developments:
- Advances in materials science are leading to the development of more durable grinding media and mill linings, reducing wear and extending the lifespan of ball mills.
- Innovations in design and automation are improving the efficiency and control of ball mills, making them more suitable for modern industrial processes.
In summary, the ball mill is a highly effective grinding machine that relies on the principles of impact and attrition to reduce materials to fine particles. Its operation is influenced by factors such as critical speed, grinding media, and the interplay of forces within the mill. While it has some limitations, ongoing advancements are enhancing its efficiency and applicability in various industries.
Summary Table:
Key Aspect | Details |
---|---|
Principle of Operation | Impact and attrition break down materials into fine particles. |
Structure | Rotating cylinder with grinding media (steel balls or rods). |
Critical Speed | Optimal speed for maximum grinding efficiency. |
Grinding Media | Larger balls for coarse materials, smaller balls for finer particles. |
Types | Horizontal, vertical, and vibrating ball mills. |
Applications | Mining, ceramics, pharmaceuticals, and materials science. |
Advantages | Versatile, efficient, and scalable for various industries. |
Limitations | Energy-intensive, wear and tear, noise, and vibration. |
Future Developments | Durable materials and automation improving efficiency and lifespan. |
Discover how a ball mill can optimize your grinding process—contact our experts today!