The particle size range of a ball mill depends on several factors, including the type of material being ground, the size and type of grinding media (balls), the speed of the mill, and the duration of the grinding process. Ball mills are versatile and can produce particles ranging from coarse to fine sizes. For coarse grinding, particles can be in the range of millimeters (1-10 mm), while for fine grinding, particles can be reduced to micrometers (1-100 µm). In the case of nanoparticles, ball mills can achieve particle sizes between 1 nanometer and 100 nanometers. The efficiency and final particle size are influenced by the operational parameters of the ball mill, such as speed and grinding time.
Key Points Explained:
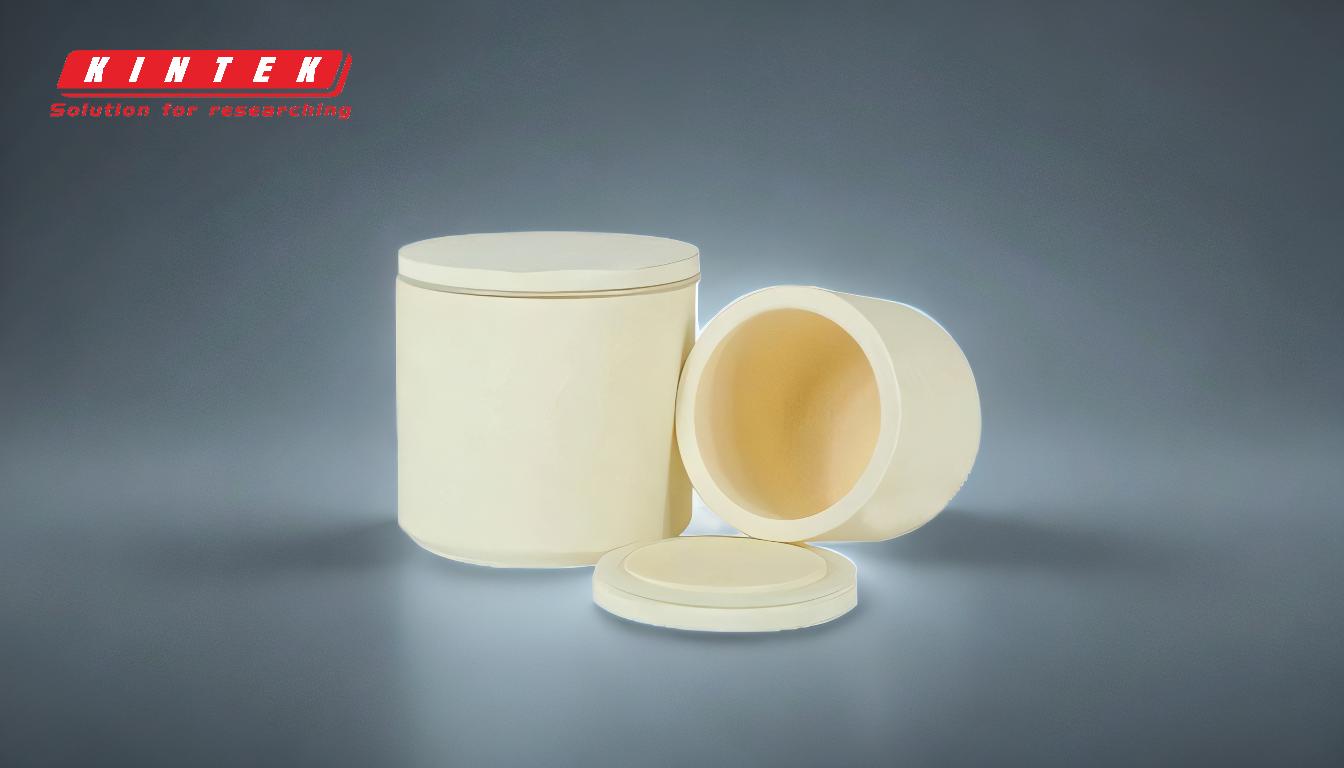
-
Particle Size Range of Ball Mills:
- Ball mills can produce particles across a wide range of sizes, from coarse to fine.
- Coarse grinding typically results in particles ranging from 1 to 10 millimeters.
- Fine grinding can reduce particles to the micrometer range, typically 1 to 100 micrometers.
- For nanoparticles, ball mills can achieve sizes between 1 nanometer and 100 nanometers.
-
Factors Influencing Particle Size:
- Material Properties: The hardness, brittleness, and initial size of the material being ground affect the final particle size.
- Grinding Media: The size, density, and material of the grinding balls (e.g., steel, ceramic) play a crucial role in determining the grinding efficiency and final particle size.
- Mill Speed: The speed of the ball mill significantly impacts the grinding process. At optimal speeds, the balls cascade and impact the material effectively, leading to efficient size reduction.
- Grinding Time: Longer grinding times generally result in finer particles, but there is a practical limit beyond which further grinding may not significantly reduce particle size.
-
Operational Parameters:
- Low Speed: At low speeds, the balls slide or roll over each other, resulting in minimal size reduction.
- High Speed: At high speeds, centrifugal force causes the balls to be thrown against the cylinder wall, preventing effective grinding.
- Optimal Speed: At normal or optimal speeds, the balls are carried to the top of the mill and then fall in a cascade, achieving maximum size reduction.
-
Applications and Limitations:
- Ball mills are widely used in industries such as mining, ceramics, pharmaceuticals, and materials science for grinding and blending materials.
- While ball mills are effective for producing fine and ultrafine particles, achieving nanoparticles requires precise control over operational parameters and may involve additional steps such as wet grinding or the use of surfactants.
-
Practical Considerations for Equipment Purchasers:
- Material Compatibility: Ensure the ball mill is compatible with the materials you intend to grind, considering factors like abrasiveness and chemical reactivity.
- Scale of Operation: Choose a ball mill size that matches your production needs, whether for laboratory-scale research or industrial-scale production.
- Energy Efficiency: Consider the energy consumption of the ball mill, especially for continuous or large-scale operations.
- Maintenance and Durability: Evaluate the ease of maintenance and the durability of the mill, particularly if it will be used for abrasive materials.
In summary, the particle size range of a ball mill is highly variable, depending on the operational parameters and the nature of the material being ground. Understanding these factors is crucial for selecting the right ball mill and optimizing the grinding process to achieve the desired particle size.
Summary Table:
Particle Size Range | Grinding Type | Typical Size |
---|---|---|
Coarse Grinding | Millimeters | 1-10 mm |
Fine Grinding | Micrometers | 1-100 µm |
Nanoparticles | Nanometers | 1-100 nm |
Key Factors | Impact on Particle Size |
---|---|
Material Properties | Hardness, brittleness, initial size |
Grinding Media | Size, density, material of balls |
Mill Speed | Optimal speed maximizes efficiency |
Grinding Time | Longer times yield finer particles |
Optimize your grinding process with the right ball mill—contact our experts today for tailored solutions!