Physical deposition techniques are methods used to create thin films or coatings on substrates by physically transferring material from a source to the substrate without involving chemical reactions. These techniques rely on mechanical, electromechanical, or thermodynamic processes and typically require a vacuum environment to ensure the material is deposited uniformly and accurately. The most common physical deposition methods include evaporation and sputtering, each with various sub-techniques such as vacuum thermal evaporation, electron beam evaporation, and cathodic arc deposition. These methods are widely used in industries like electronics, optics, and manufacturing due to their precision and ability to produce high-quality thin films.
Key Points Explained:
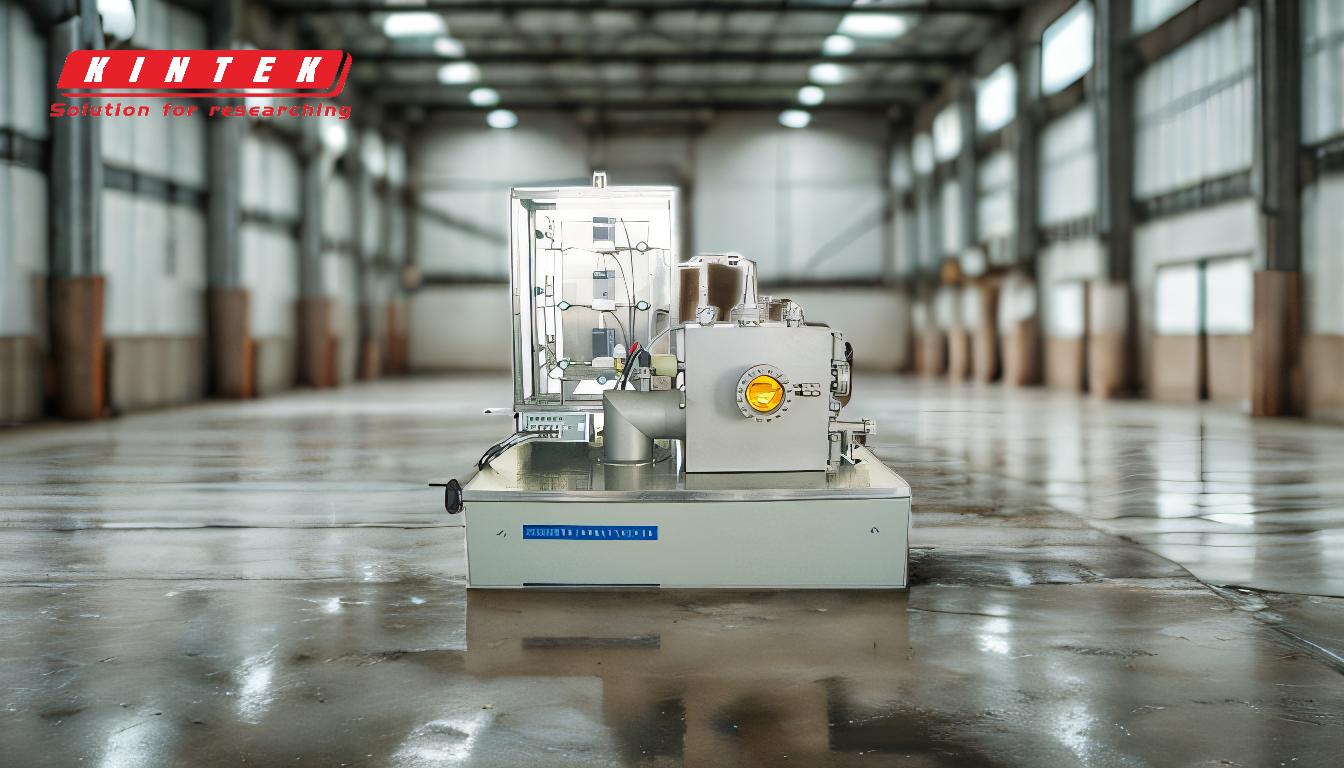
-
Definition of Physical Deposition Techniques:
- Physical deposition techniques involve the transfer of material from a source to a substrate using mechanical, electromechanical, or thermodynamic methods.
- Unlike chemical deposition, physical deposition does not rely on chemical reactions to form the thin film.
- These techniques are typically performed in a vacuum environment to ensure the material is deposited uniformly and without contamination.
-
Key Components of Physical Deposition:
- Vacuum Chamber: Essential for creating a low-pressure environment that allows material particles to move freely and deposit uniformly on the substrate.
- Source Material: The material to be deposited, which is often in a solid or liquid state initially.
- Substrate: The surface on which the thin film is deposited, which is usually cooler than the source material to facilitate deposition.
-
Common Physical Deposition Methods:
-
Evaporation:
- Involves heating the source material until it evaporates or sublimates into a gaseous state.
- The gaseous material then condenses on the cooler substrate, forming a thin film.
- Sub-techniques include:
- Vacuum Thermal Evaporation: Uses heat to evaporate the material in a vacuum.
- Electron Beam Evaporation: Uses an electron beam to heat and evaporate the material.
- Laser Beam Evaporation: Uses a laser to ablate and evaporate the material.
- Arc Evaporation: Uses an electric arc to vaporize the material.
- Molecular Beam Epitaxy (MBE): A highly controlled form of evaporation used to grow crystalline layers.
- Ion Plating Evaporation: Combines evaporation with ion bombardment to enhance film adhesion and density.
-
Sputtering:
- Involves bombarding the source material (target) with high-energy ions or plasma, causing atoms to be ejected from the target.
- These ejected atoms then deposit onto the substrate, forming a thin film.
- Sputtering is widely used in the production of semiconductors and optical coatings.
-
Evaporation:
-
Advantages of Physical Deposition Techniques:
- High Precision: Allows for the deposition of very thin and uniform films, often at the nanometer scale.
- Material Versatility: Can be used with a wide range of materials, including metals, ceramics, and semiconductors.
- Controlled Environment: The vacuum environment minimizes contamination and allows for precise control over deposition parameters.
- Adhesion and Density: Techniques like ion plating and sputtering can produce films with excellent adhesion and density.
-
Applications of Physical Deposition Techniques:
- Electronics: Used to deposit thin films in the production of semiconductors, integrated circuits, and microelectromechanical systems (MEMS).
- Optics: Used to create anti-reflective coatings, mirrors, and optical filters.
- Manufacturing: Applied in the production of hard coatings for tools, decorative coatings, and corrosion-resistant layers.
-
Comparison with Chemical Deposition Techniques:
- Physical Deposition (PVD): Relies on physical processes and does not involve chemical reactions. It is typically performed in a vacuum and is suitable for a wide range of materials.
- Chemical Deposition (CVD): Involves chemical reactions to form the thin film. It can be performed at atmospheric pressure or in a vacuum and is often used for depositing complex materials like oxides and nitrides.
-
Examples of Physical Deposition Techniques:
- Arc-PVD (Cathodic Arc Deposition): Uses an electric arc to vaporize material from a cathode, which then deposits onto the substrate.
- Pulsed Laser Deposition (PLD): Uses a high-power laser to ablate material from a target, which then deposits onto the substrate.
- Sputtering: Includes techniques like magnetron sputtering, which uses a magnetic field to enhance the efficiency of the sputtering process.
- Thermal Evaporation: One of the simplest and most widely used physical deposition methods, particularly for metals and simple compounds.
In summary, physical deposition techniques are essential for creating high-quality thin films in a variety of industries. They offer precise control over the deposition process and are capable of producing films with excellent properties, making them a preferred choice for many applications.
Summary Table:
Aspect | Details |
---|---|
Definition | Techniques transferring material physically without chemical reactions. |
Key Components | Vacuum chamber, source material, and substrate. |
Common Methods | Evaporation (thermal, electron beam, laser) and sputtering. |
Advantages | High precision, material versatility, controlled environment, strong adhesion. |
Applications | Electronics (semiconductors), optics (mirrors), manufacturing (coatings). |
Comparison with CVD | PVD: No chemical reactions, vacuum-based. CVD: Chemical reactions, atmospheric or vacuum. |
Interested in high-quality thin films for your applications? Contact our experts today to learn more!