Plasma generation in Plasma-Enhanced Chemical Vapor Deposition (PECVD) is a critical process that enables the deposition of thin films at lower temperatures compared to traditional Chemical Vapor Deposition (CVD). By using plasma, which consists of ionized gas containing electrons and ions, the energy required to drive chemical reactions is supplied without the need for high thermal energy. This allows for the formation of high-quality films with strong bonding on substrates that are sensitive to high temperatures. Plasma generation in PECVD is typically achieved through electrical energy at various frequencies, such as radio frequency (RF) or microwave frequency, which ionizes the gas and creates the necessary reactive species for the deposition process.
Key Points Explained:
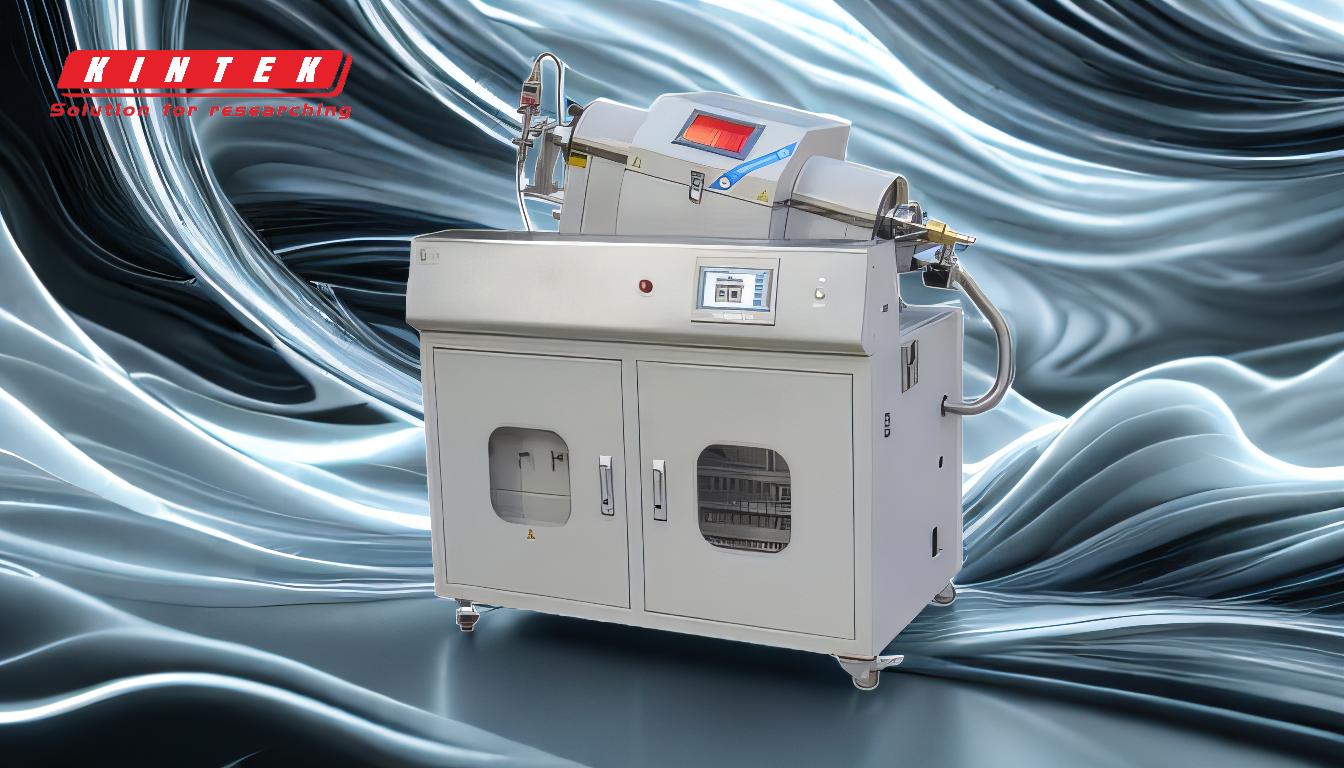
-
Role of Plasma in PECVD:
- Plasma in PECVD provides the energy required to drive chemical reactions for thin film deposition. Unlike traditional CVD, which relies on high temperatures, PECVD uses plasma to achieve the same reactions at significantly lower temperatures (200–500°C). This reduces thermal stress on the substrate and allows for the deposition of films on temperature-sensitive materials.
-
Plasma Composition and Function:
- Plasma consists of ionized gas containing electrons, ions, and radicals. These charged particles have sufficient energy to break chemical bonds in the precursor gases, creating reactive species such as radicals. These radicals then participate in the chemical reactions that form the thin film on the substrate surface.
-
Mechanisms of Plasma-Assisted Reactions:
- Electron-Molecule Collisions: Electrons in the plasma collide with gas molecules, breaking their bonds and creating reactive radicals in the gas phase.
- Ion Bombardment: Ions in the plasma bombard the surface of the growing film, activating the surface by creating dangling bonds. This enhances the adhesion and densification of the film.
- Etching Weakly Bonded Groups: Ions also help remove weakly bonded terminating groups from the surface, leading to a denser and more uniform film.
-
Advantages of Plasma in PECVD:
- Lower Temperature Processing: Plasma enables deposition at lower temperatures, making it suitable for substrates that cannot withstand high temperatures, such as polymers or certain metals.
- Improved Film Quality: The energetic ions and radicals in the plasma promote strong bonding between the film and the substrate, resulting in high-quality, durable films.
- Enhanced Control: Plasma allows for precise control over the deposition process, enabling the formation of nano-scale films with specific properties.
-
Methods of Plasma Generation:
- Electrical Energy: Plasma is typically generated using electrical energy at various frequencies, such as audio frequency (AF), radio frequency (RF), or microwave frequency. These frequencies ionize the gas and create the plasma.
- Heating Gas: While heating the gas can also produce plasma, this method is less practical due to the extremely high temperatures required for ionization.
-
Applications of PECVD:
- Semiconductor Industry: PECVD is widely used in the semiconductor industry for depositing thin films on silicon wafers and other substrates.
- Protective Coatings: The process is used to apply nano-scale polymer protective films on electronic products, ensuring strong adhesion and durability.
- Optical and Mechanical Coatings: PECVD is also employed in the production of optical coatings, anti-reflective layers, and mechanical protective layers.
-
Process Parameters:
- Gas Composition: The choice of precursor gases determines the type of film deposited. Common gases include silane (SiH₄), ammonia (NH₃), and methane (CH₄).
- Pressure and Flow Rate: The pressure and flow rate of the gases influence the uniformity and quality of the deposited film.
- Plasma Power and Frequency: The power and frequency of the plasma source affect the density and energy of the ions and radicals, which in turn impact the film properties.
In summary, plasma generation in PECVD is a fundamental aspect of the process, enabling low-temperature deposition of high-quality thin films. By leveraging the energetic ions and radicals in the plasma, PECVD achieves precise control over film properties, making it a versatile and essential technique in modern manufacturing and semiconductor fabrication.
Summary Table:
Key Aspect | Details |
---|---|
Role of Plasma | Provides energy for chemical reactions at lower temperatures (200–500°C). |
Plasma Composition | Ionized gas with electrons, ions, and radicals for reactive species creation. |
Mechanisms | Electron-molecule collisions, ion bombardment, and etching weakly bonded groups. |
Advantages | Lower temperature processing, improved film quality, and enhanced control. |
Methods of Generation | Electrical energy (RF, microwave) ionizes gas to create plasma. |
Applications | Semiconductor fabrication, protective coatings, and optical/mechanical layers. |
Process Parameters | Gas composition, pressure, flow rate, plasma power, and frequency. |
Discover how PECVD can revolutionize your thin film processes—contact our experts today!