Electron beam evaporation is a thin film deposition technique that operates under high vacuum conditions to minimize contamination and ensure controlled material deposition. The process involves heating a target material using a focused electron beam, which causes the material to evaporate and deposit onto a substrate. The pressure requirements for electron beam evaporation are critical to its success. The chamber must maintain a high vacuum environment, typically with a pressure of less than 10^-5 Torr, to reduce collisions between source atoms and background gases. Additionally, for reasonable deposition rates, the vapor pressure of the material being evaporated should be around 10 mTorr. This method is particularly effective for evaporating refractory metals that require high temperatures beyond the capabilities of thermal evaporation. The vacuum environment also helps achieve cleaner and more uniform thin films, which are essential for high-quality coatings.
Key Points Explained:
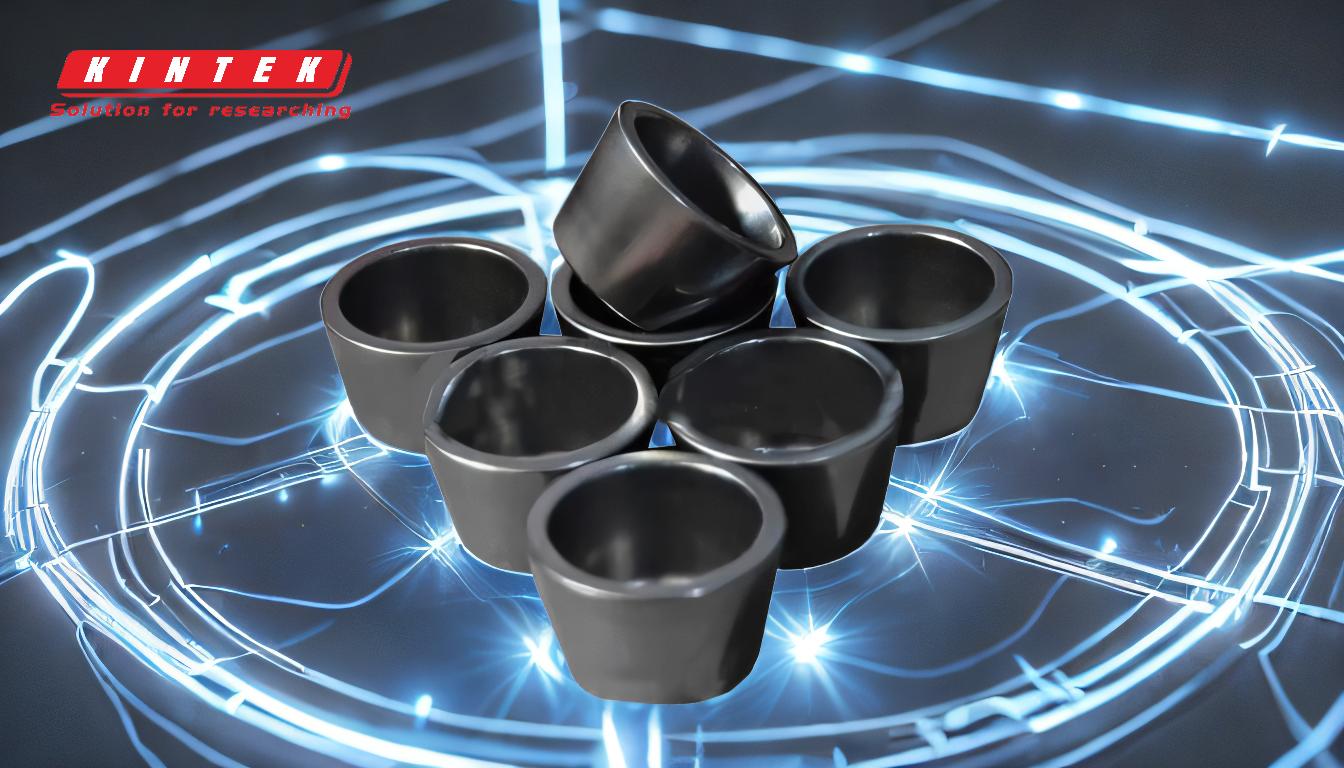
-
High Vacuum Environment:
- Electron beam evaporation requires a high vacuum chamber with a pressure of less than 10^-5 Torr. This low pressure minimizes collisions between the source atoms and background gases, ensuring a cleaner deposition process.
- The high vacuum environment is crucial for achieving high-quality thin films with minimal contamination. It also allows for better control over the deposition process, which is essential for applications requiring precise and uniform coatings.
-
Vapor Pressure for Deposition:
- For reasonable deposition rates, the vapor pressure of the material being evaporated must be approximately 10 mTorr. This ensures that the material evaporates efficiently and deposits uniformly onto the substrate.
- The vapor pressure is a key factor in determining the rate at which the material transitions from the solid or liquid phase to the vapor phase, which directly affects the deposition rate and the quality of the thin film.
-
Refractory Metals and High Temperatures:
- Electron beam evaporation is particularly useful for evaporating refractory metals, which require high temperatures beyond the operating range of thermal evaporation. The focused electron beam provides the necessary thermal energy to evaporate these materials.
- Refractory metals, such as tungsten, molybdenum, and tantalum, have high melting points and are difficult to evaporate using conventional methods. Electron beam evaporation overcomes this limitation by delivering concentrated energy to the target material.
-
Isotropic Deposition and Uniformity:
- Evaporation is an isotropic process, meaning the material disperses uniformly in all directions. However, this can lead to deposition uniformity issues, especially on non-planar substrates.
- To address this, spherical wafer holders or other techniques are often used to ensure even deposition across the substrate. This is particularly important for applications requiring uniform coatings, such as in semiconductor manufacturing or optical coatings.
-
Role of Reactive Gases:
- In some cases, reactive gases like oxygen or nitrogen can be introduced into the vacuum chamber to deposit non-metallic films. This allows for the creation of oxide or nitride coatings, which are useful in various applications, including protective coatings and optical films.
- The introduction of reactive gases adds another layer of control over the deposition process, enabling the creation of complex material compositions and tailored film properties.
-
Energy Conversion and Thermal Efficiency:
- The electron beam transfers kinetic energy to the target material, which is then converted into thermal energy upon impact. This thermal energy heats the material to the point of evaporation or sublimation.
- The efficiency of this energy conversion is critical to the process. The heat produced must exceed the heat lost to the environment to ensure continuous evaporation and deposition.
-
Magnetic Field Focusing:
- A magnetic field is used to focus the electron beam onto the target material in the crucible. This focusing ensures that the energy is concentrated on a small area, allowing for precise control over the evaporation process.
- The magnetic field also helps maintain the stability and directionality of the electron beam, which is essential for consistent and repeatable deposition.
-
Water-Cooled Crucible:
- The crucible containing the target material is water-cooled to prevent it from melting or degrading due to the high temperatures generated by the electron beam. This cooling mechanism is essential for maintaining the integrity of the crucible and ensuring a stable evaporation process.
- The water-cooled crucible also helps manage the thermal load within the chamber, preventing overheating and maintaining the high vacuum conditions required for the process.
In summary, electron beam evaporation operates under strict pressure conditions to ensure a clean and controlled deposition environment. The high vacuum (less than 10^-5 Torr) minimizes contamination, while the vapor pressure of around 10 mTorr ensures efficient evaporation and deposition. The method is particularly effective for refractory metals and can be enhanced with reactive gases for non-metallic films. Uniformity is maintained through techniques like spherical wafer holders, and the process relies on precise energy conversion and thermal management to achieve high-quality thin films.
Summary Table:
Key Aspect | Details |
---|---|
High Vacuum Environment | Pressure <10^-5 Torr to minimize contamination and ensure clean deposition. |
Vapor Pressure | ~10 mTorr for efficient evaporation and uniform deposition rates. |
Refractory Metals | Ideal for high-temperature materials like tungsten and molybdenum. |
Uniformity Techniques | Spherical wafer holders ensure even deposition on non-planar substrates. |
Reactive Gases | Oxygen or nitrogen can create oxide or nitride coatings. |
Energy Conversion | Electron beam converts kinetic energy to thermal energy for evaporation. |
Magnetic Field Focusing | Ensures precise electron beam control for stable deposition. |
Water-Cooled Crucible | Prevents crucible degradation and maintains thermal stability. |
Discover how electron beam evaporation can enhance your thin film processes—contact our experts today!