Chemical vapor deposition (CVD) is a versatile and widely used technique for depositing thin films and coatings on substrates through chemical reactions in the vapor phase. The process involves the introduction of precursor gases into a reaction chamber, where they undergo chemical reactions to form a solid material on the substrate surface. CVD is highly controllable and can produce ultra-thin, high-quality layers of materials, making it ideal for applications in electronics, optics, and advanced materials. The process relies on precise control of temperature, pressure, and gas flow rates to achieve the desired chemical reactions and film properties. Different types of CVD, such as hot filament, plasma-enhanced, and aerosol-assisted CVD, offer unique advantages depending on the application.
Key Points Explained:
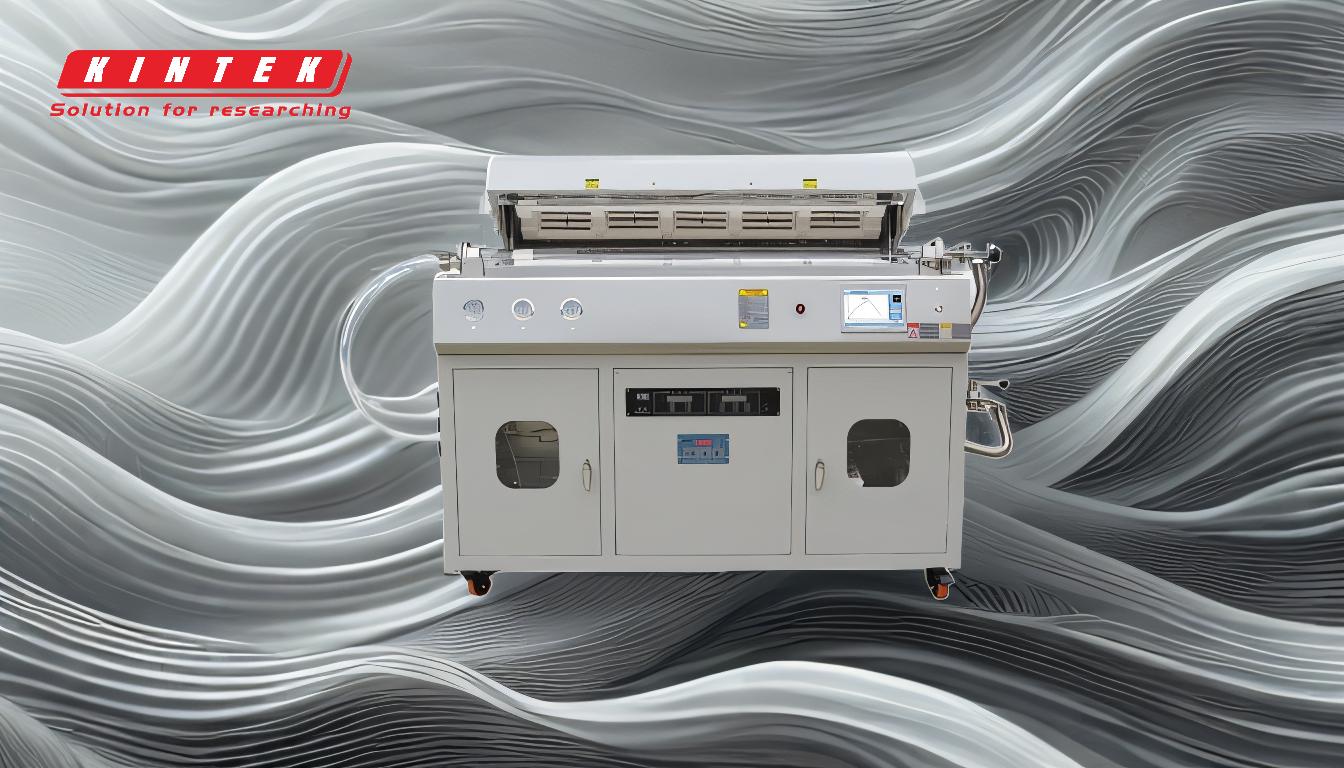
-
Fundamental Steps of CVD:
- The CVD process involves several key steps:
- Transport of Reactants: Precursor gases are introduced into the reaction chamber and transported to the substrate surface via convection or diffusion.
- Gas Phase Reactions: Chemical reactions occur in the gas phase, producing reactive species and by-products.
- Surface Reactions: Reactive species diffuse through the boundary layer and adsorb onto the substrate surface, where they undergo heterogeneous surface reactions to form a solid film.
- Desorption and Removal: Volatile by-products desorb from the surface and are removed from the chamber via diffusion and convection.
- The CVD process involves several key steps:
-
Types of CVD:
- Hot Filament CVD: Uses high-temperature filaments (e.g., tungsten or tantalum) to cleave and excite precursor gases, such as CH4-H2 mixtures, to produce reactive particles for diamond film synthesis.
- Plasma-Enhanced CVD (PECVD): Utilizes plasma to generate reactive species at lower temperatures, enabling the deposition of materials like silicon nitride and amorphous silicon.
- Aerosol-Assisted CVD: Employs aerosolized precursors for deposition, often used for complex materials or coatings.
- Direct Liquid Injection CVD: Involves injecting liquid precursors into a heated chamber, suitable for depositing materials like metal oxides.
-
Advantages of CVD:
- High Versatility: CVD can deposit a wide range of materials, including metals, ceramics, and polymers, by adjusting precursor gases and reaction conditions.
- Precision and Control: The process allows precise control over film thickness, composition, and microstructure.
- Ultra-Thin Films: CVD is capable of producing ultra-thin, uniform layers, essential for applications in microelectronics and nanotechnology.
- Scalability: CVD can be scaled for industrial production, making it suitable for large-area coatings and high-throughput manufacturing.
-
Applications of CVD:
- Microelectronics: CVD is used to deposit dielectric layers, conductive films, and semiconductor materials in integrated circuits and transistors.
- Optics: Thin films for anti-reflective coatings, mirrors, and optical filters are produced using CVD.
- Advanced Materials: CVD is employed to create diamond films, graphene, and other high-performance materials for cutting tools, sensors, and energy storage devices.
-
Key Factors in CVD:
- Temperature: The reaction temperature influences the rate of chemical reactions and the quality of the deposited film.
- Pressure: Operating pressure affects gas-phase reactions and the uniformity of the film.
- Gas Flow Rates: Precursor and carrier gas flow rates determine the concentration of reactive species and the deposition rate.
By understanding the principles and variations of CVD, manufacturers and researchers can optimize the process for specific applications, ensuring high-quality, functional coatings and films.
Summary Table:
Aspect | Details |
---|---|
Fundamental Steps | 1. Transport of Reactants 2. Gas Phase Reactions 3. Surface Reactions 4. Desorption and Removal |
Types of CVD | Hot Filament CVD, Plasma-Enhanced CVD, Aerosol-Assisted CVD, Direct Liquid Injection CVD |
Advantages | High Versatility, Precision and Control, Ultra-Thin Films, Scalability |
Applications | Microelectronics, Optics, Advanced Materials |
Key Factors | Temperature, Pressure, Gas Flow Rates |
Optimize your thin film processes with CVD—contact our experts today for tailored solutions!