Plasma Enhanced Chemical Vapor Deposition (PECVD) is a thin-film deposition technique that leverages low-temperature plasma to enhance chemical reactions, enabling the formation of solid films on substrates at lower temperatures compared to traditional Chemical Vapor Deposition (CVD). PECVD involves introducing reactant gases into a reactor, ionizing them into a plasma state using an electric field (typically RF), and allowing the reactive species to deposit on a substrate. This process is widely used in semiconductor manufacturing and other industries due to its ability to produce high-quality, uniform films with strong adhesion and dense structures at relatively low temperatures, minimizing thermal stress on the substrate.
Key Points Explained:
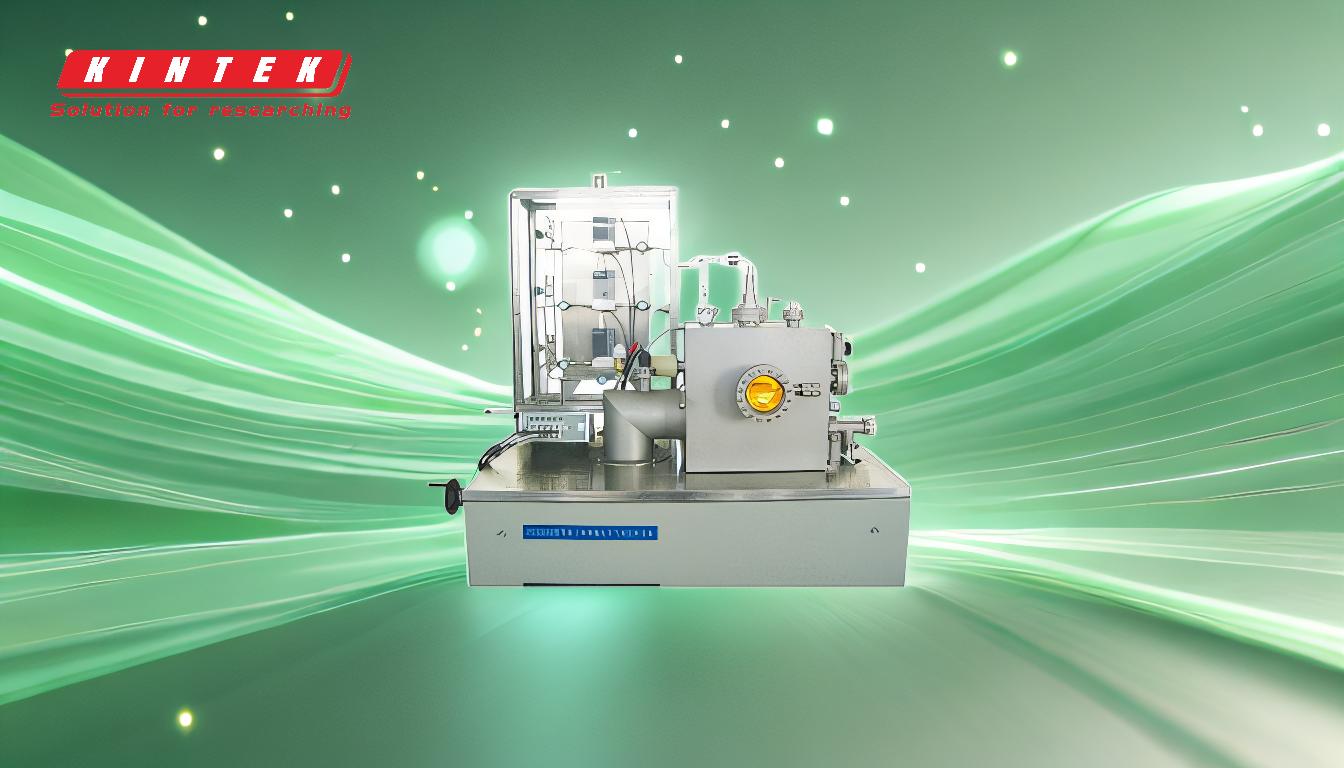
-
Plasma Generation and Ionization:
- PECVD relies on plasma, a partially ionized gas containing free electrons, ions, and neutral species, to enhance chemical reactions.
- Plasma is generated by applying a high-frequency electric field (RF) between parallel electrodes in a low-pressure environment.
- The electric field ionizes the reactant gases, creating reactive species such as radicals and ions.
-
Chemical Reactions and Deposition:
- The reactive species generated by the plasma diffuse to the substrate surface, where they adsorb and undergo chemical reactions.
- These reactions result in the formation of a solid film on the substrate.
- The process typically occurs at temperatures between 100°C and 400°C, significantly lower than traditional CVD.
-
Role of Substrate Heating:
- The substrate is often heated to a moderate temperature (e.g., 350°C) to facilitate the deposition process.
- Heating improves the mobility of reactive species on the substrate surface, leading to better film uniformity and adhesion.
-
Advantages of PECVD:
- Low Deposition Temperature: Reduces thermal stress on the substrate, making it suitable for temperature-sensitive materials.
- High-Quality Films: Produces dense, uniform films with strong adhesion and minimal defects.
- Versatility: Can deposit a wide range of materials, including silicon oxides, silicon nitride, amorphous silicon, and organic films.
- Step Coverage: Provides excellent coverage over complex geometries and high-aspect-ratio features.
-
Process Parameters:
- Pressure: Typically operates at mid-pressure (e.g., 1 Torr) to maintain plasma stability and control reaction kinetics.
- Gas Flow Rates: Precise control of reactant gas flow rates ensures consistent film composition and properties.
- RF Power: Adjusting the RF power controls the plasma density and energy, influencing film growth rate and quality.
-
Applications:
- PECVD is widely used in the semiconductor industry for depositing dielectric layers, passivation films, and conductive layers.
- It is also employed in the production of solar cells, MEMS devices, and optical coatings.
-
Comparison to Traditional CVD:
- Unlike traditional CVD, which relies solely on thermal energy to drive chemical reactions, PECVD utilizes both plasma energy and thermal energy.
- This dual-energy approach enables PECVD to achieve high-quality film deposition at lower temperatures, expanding its applicability to a broader range of substrates and materials.
By combining plasma-enhanced chemical activity with controlled thermal energy, PECVD offers a powerful and versatile method for depositing high-quality thin films at lower temperatures, making it a cornerstone technology in modern materials science and semiconductor fabrication.
Summary Table:
Key Aspect | Details |
---|---|
Plasma Generation | Ionizes reactant gases using RF electric field in a low-pressure environment. |
Deposition Temperature | 100°C to 400°C, significantly lower than traditional CVD. |
Advantages | Low thermal stress, high-quality films, versatility, excellent step coverage. |
Applications | Semiconductors, solar cells, MEMS devices, optical coatings. |
Comparison to CVD | Uses plasma energy and thermal energy for lower-temperature deposition. |
Interested in integrating PECVD into your fabrication process? Contact our experts today to learn more!