Reactive sputtering is a specialized form of magnetron sputtering where a reactive gas is introduced into the sputtering process to chemically react with the sputtered material, forming a compound film on the substrate. This technique is widely used to deposit thin films of oxides, nitrides, and other compounds. The principle involves the interaction between the sputtered target material and the reactive gas, which forms a compound layer on the substrate. The process is highly controllable, allowing precise tuning of film composition and properties.
Key Points Explained:
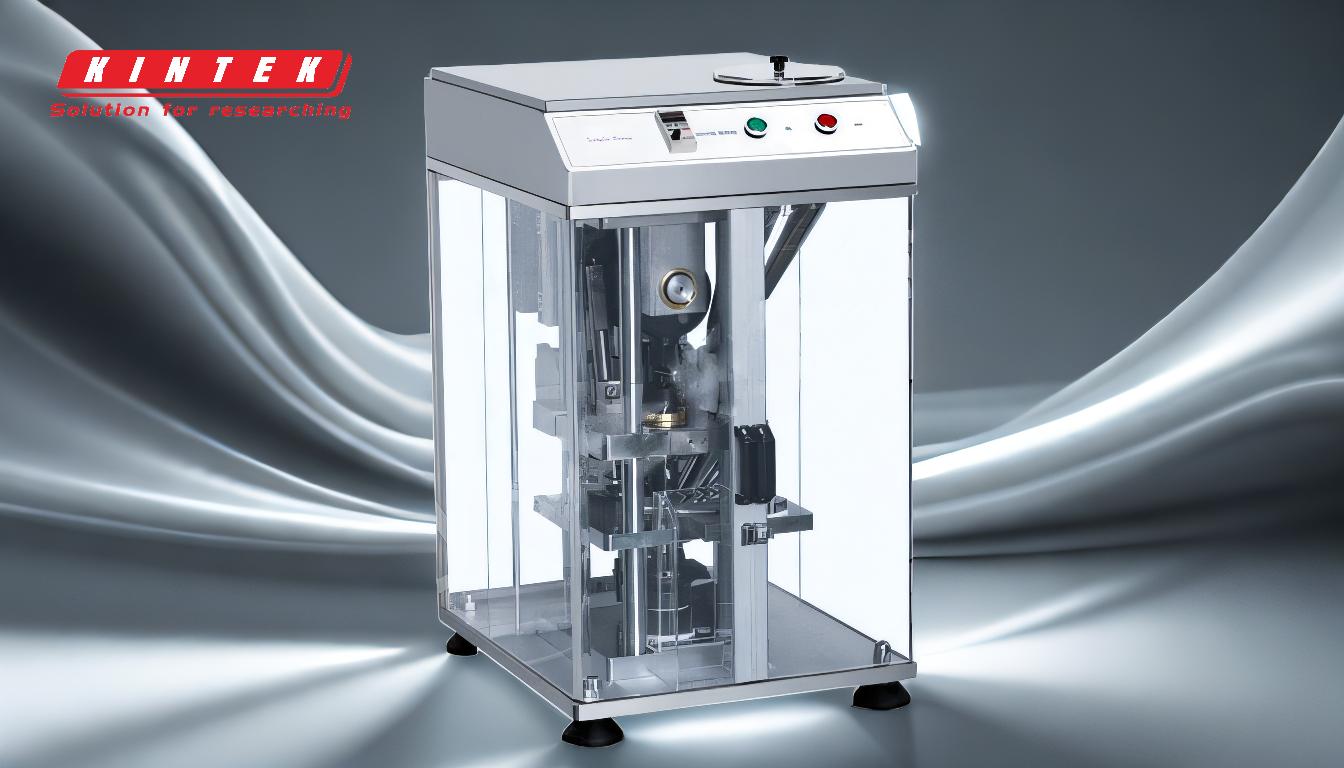
-
Basic Principle of Magnetron Sputtering:
- Magnetron sputtering involves creating a plasma of high-energy ions that bombard a target material, causing atoms to be ejected and deposited onto a substrate.
- The process uses magnetic fields to confine the plasma, increasing its density and enhancing the sputtering rate.
- This method does not require the target material to melt or evaporate, making it suitable for a wide range of materials.
-
Introduction of Reactive Gases:
- In reactive sputtering, a reactive gas (such as oxygen, nitrogen, or a hydrocarbon) is introduced into the sputtering chamber.
- The reactive gas chemically reacts with the sputtered atoms from the target material, forming a compound (e.g., oxides, nitrides) on the substrate.
- This reaction occurs either on the substrate surface or in the gas phase, depending on the process conditions.
-
Control of Reactive Sputtering Process:
- The composition and properties of the deposited film can be precisely controlled by adjusting the flow rate of the reactive gas and the sputtering power.
- The process can operate in two modes: metal mode (where the target is mostly metallic) and compound mode (where the target surface is fully reacted).
- Transition between these modes can lead to hysteresis effects, requiring careful control to maintain stable deposition conditions.
-
Advantages of Reactive Sputtering:
- Enables the deposition of a wide variety of compound films with tailored properties, such as hardness, optical transparency, or electrical conductivity.
- Suitable for large-scale industrial applications due to its high deposition rates and uniformity.
- Allows for the use of metallic targets, which are often easier to fabricate and handle than compound targets.
-
Challenges and Considerations:
- The introduction of reactive gases can lead to target poisoning, where the target surface becomes fully reacted, reducing sputtering efficiency.
- Maintaining a stable process requires careful balancing of gas flow rates, sputtering power, and chamber pressure.
- The process may require additional equipment, such as gas flow controllers and monitoring systems, to ensure consistent film quality.
By understanding these key points, one can appreciate the versatility and precision of reactive sputtering in thin film deposition, making it a valuable technique in industries ranging from electronics to optics.
Summary Table:
Aspect | Details |
---|---|
Basic Principle | High-energy ions bombard a target, ejecting atoms to form a thin film. |
Reactive Gas Role | Introduces gases like oxygen or nitrogen to chemically form compound films. |
Process Control | Adjust gas flow and sputtering power for precise film properties. |
Advantages | Tailored film properties, high deposition rates, and uniformity. |
Challenges | Target poisoning, hysteresis effects, and process stability. |
Discover how reactive sputtering can enhance your thin film applications—contact our experts today!