The principle of a sieving machine revolves around the separation of particles based on their size using a wire-mesh sieve. The material to be separated is subjected to either vertical or horizontal motion, creating relative movement between the sieve and the particles. Smaller particles pass through the mesh, while larger particles are retained on the surface. This process is optimized by using sieves with different mesh sizes, depending on the material being processed. Additionally, some sieving machines incorporate tapping mechanisms that combine horizontal circular motion with vertical tapping impulses to enhance separation efficiency.
Key Points Explained:
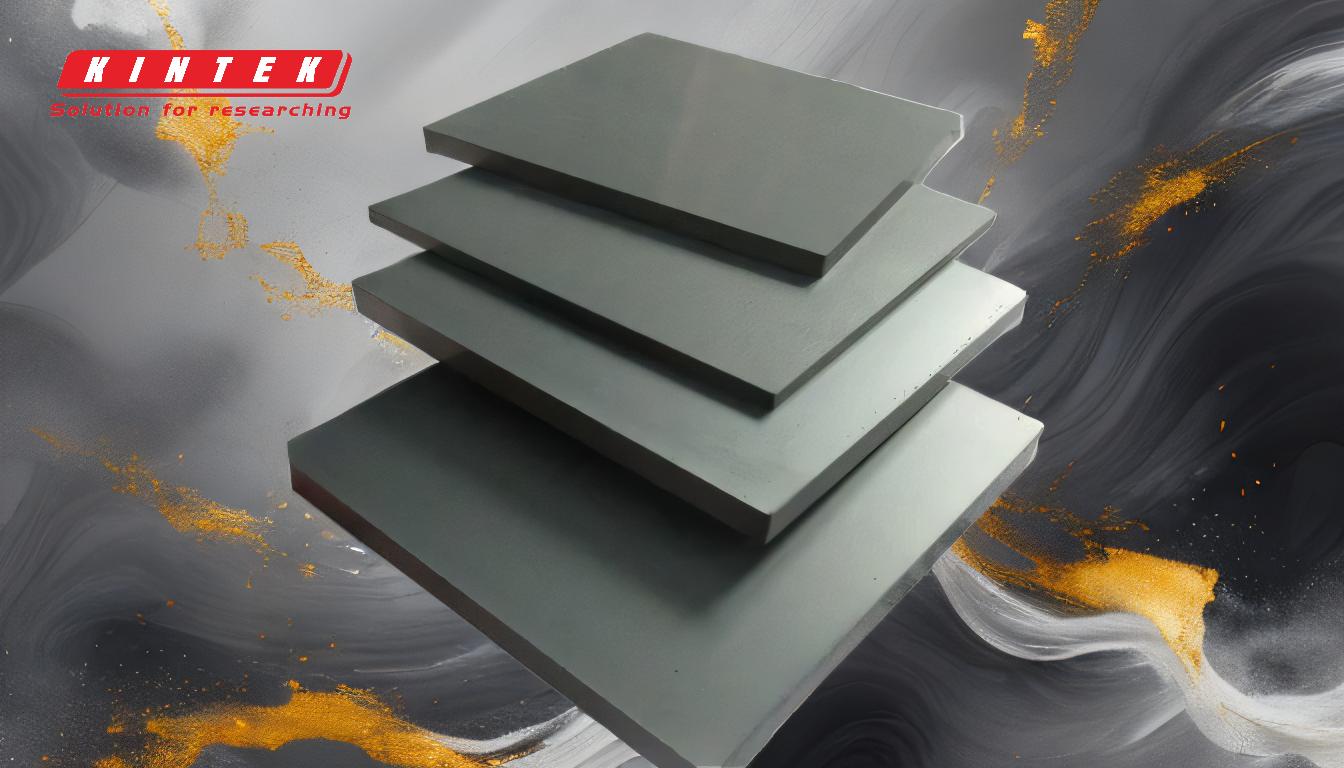
-
Separation Based on Particle Size:
- The core principle of a sieving machine is to separate particles according to their size. This is achieved using a wire-mesh sieve with specific aperture sizes.
- Smaller particles pass through the mesh, while larger particles are retained on the sieve surface. This ensures a clear distinction between different particle sizes.
-
Motion Mechanism:
- Sieving machines employ either vertical or horizontal motion to facilitate the separation process. This motion creates relative movement between the sieve and the particles, allowing for effective separation.
- The motion ensures that particles are constantly moving and interacting with the sieve mesh, increasing the likelihood of smaller particles passing through.
-
Role of Sieve Mesh:
- The sieve mesh is a critical component that determines the separation efficiency. The mesh size is selected based on the material being processed and the desired particle size distribution.
- Different mesh sizes can be used to optimize the separation process for various materials, ensuring accurate and consistent results.
-
Tapping Mechanism:
- Some sieving machines incorporate a tapping mechanism that overlays horizontal circular motion with slight vertical motions. This tapping impulse, triggered from underneath the sieve, enhances the separation process.
- The vertical motion helps to dislodge particles that may be stuck in the mesh, ensuring that all particles have an opportunity to pass through if they are small enough.
-
Optimization for Different Materials:
- The sieving process can be optimized for different materials by adjusting the motion type, sieve mesh size, and tapping frequency. This flexibility allows sieving machines to handle a wide range of materials with varying particle sizes.
- Analyzing sieves with different mesh sizes is a common practice to achieve the desired separation for specific applications.
-
Applications and Importance:
- Sieving machines are widely used in industries such as pharmaceuticals, food processing, construction, and mining. They are essential for quality control, ensuring that materials meet specific size specifications.
- The ability to separate particles accurately and efficiently makes sieving machines a vital tool in many industrial processes.
In summary, the principle of a sieving machine is based on the separation of particles by size using a wire-mesh sieve, facilitated by motion mechanisms and, in some cases, tapping impulses. The process is optimized by selecting appropriate sieve mesh sizes and motion types, making sieving machines versatile and essential in various industries.
Summary Table:
Key Aspect | Description |
---|---|
Separation by Particle Size | Uses a wire-mesh sieve to separate smaller particles from larger ones. |
Motion Mechanism | Vertical or horizontal motion ensures particles interact with the sieve mesh. |
Sieve Mesh Role | Mesh size is selected based on material and desired particle size distribution. |
Tapping Mechanism | Combines horizontal and vertical motions to enhance separation efficiency. |
Optimization | Adjust motion type, mesh size, and tapping frequency for different materials. |
Applications | Used in pharmaceuticals, food processing, construction, and mining industries. |
Discover how a sieving machine can optimize your material separation process—contact our experts today!