Sputtering is a physical vapor deposition (PVD) technique used to deposit thin films onto substrates. The process involves bombarding a target material with high-energy ions, typically from an inert gas like argon, in a vacuum chamber. These ions dislodge atoms from the target, which then travel through the chamber and deposit onto a substrate, forming a thin film. The process is highly controlled and is widely used in industries such as semiconductors, optics, and coatings due to its precision and ability to produce uniform, high-quality films.
Key Points Explained:
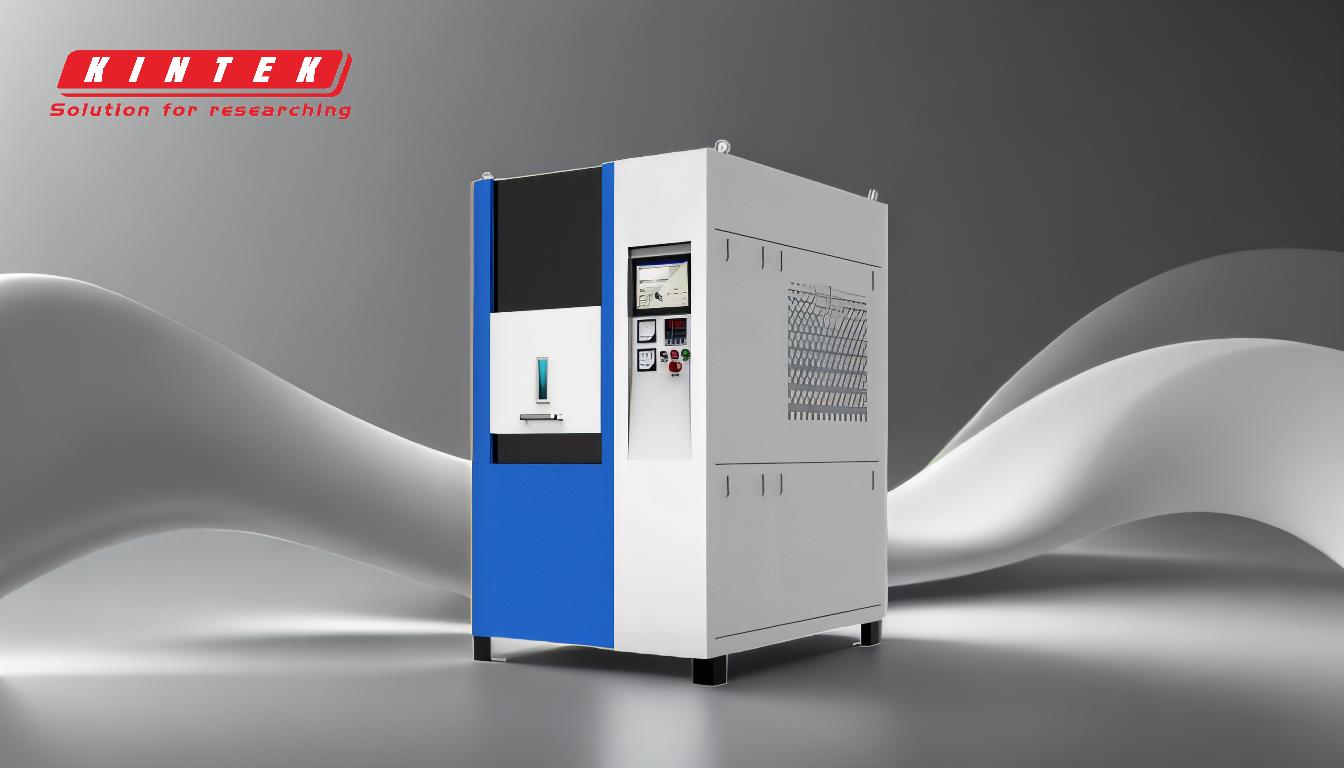
-
Basic Principle of Sputtering:
- Sputtering is a process where atoms are ejected from a solid target material due to bombardment by high-energy ions.
- The ejected atoms then travel through a vacuum chamber and deposit onto a substrate, forming a thin film.
-
Components Involved:
- Target Material: The source material from which atoms are ejected. It is typically a metal or compound that forms the desired film.
- Substrate: The surface onto which the ejected atoms are deposited. This can be a wafer, glass, or any other material requiring a thin film coating.
- Vacuum Chamber: The environment where the sputtering process occurs, ensuring minimal contamination and controlled conditions.
- Inert Gas (e.g., Argon): Introduced into the chamber and ionized to create a plasma, which generates the high-energy ions needed for sputtering.
-
Ionization and Plasma Generation:
- A voltage is applied between the target (cathode) and the substrate (anode), creating an electric field.
- The inert gas atoms lose electrons in the plasma, becoming positively charged ions.
- These ions are accelerated towards the target due to the electric field.
-
Bombardment and Ejection:
- The high-energy ions collide with the target material, transferring their kinetic energy to the target atoms.
- When the kinetic energy exceeds the binding energy of the target atoms, they are ejected from the surface.
- This process is known as a collision cascade, where the energy transfer causes a chain reaction of atomic displacements.
-
Deposition of Thin Film:
- The ejected atoms travel through the vacuum chamber in a vapor stream.
- They condense onto the substrate, forming a thin film with high uniformity and adherence.
- The film's properties, such as thickness and composition, can be precisely controlled by adjusting parameters like gas pressure, voltage, and target material.
-
Advantages of Sputtering:
- Precision: Sputtering allows for the deposition of very thin, uniform films with precise control over thickness and composition.
- Versatility: It can be used with a wide range of materials, including metals, alloys, and compounds.
- High-Quality Films: The films produced are typically of high quality, with excellent adhesion and minimal defects.
- Scalability: The process is scalable and can be used for both small-scale research and large-scale industrial production.
-
Applications:
- Semiconductors: Used to deposit thin films of conductive, insulating, or semiconducting materials on silicon wafers.
- Optics: Used to create anti-reflective coatings, mirrors, and other optical components.
- Coatings: Used to apply protective or decorative coatings on various materials, including glass, metals, and plastics.
- Magnetic Storage: Used in the production of magnetic films for hard drives and other data storage devices.
-
Types of Sputtering:
- DC Sputtering: Uses a direct current (DC) power supply to generate the plasma. Suitable for conductive materials.
- RF Sputtering: Uses radio frequency (RF) power to ionize the gas, allowing for the sputtering of insulating materials.
- Magnetron Sputtering: Incorporates magnets to confine the plasma near the target, increasing the sputtering rate and efficiency.
- Reactive Sputtering: Involves the introduction of a reactive gas (e.g., oxygen or nitrogen) to form compound films (e.g., oxides or nitrides) during deposition.
-
Challenges and Considerations:
- Contamination: The vacuum environment must be carefully controlled to prevent contamination of the film.
- Target Erosion: The target material erodes over time, requiring periodic replacement.
- Uniformity: Achieving uniform film thickness across large substrates can be challenging and may require advanced techniques like substrate rotation or multiple targets.
-
Future Developments:
- High-Power Impulse Magnetron Sputtering (HiPIMS): A technique that uses short, high-power pulses to increase the ionization of the sputtered material, resulting in denser and more adherent films.
- Atomic Layer Deposition (ALD) Integration: Combining sputtering with ALD to achieve atomic-level control over film thickness and composition.
- Green Sputtering: Developing more environmentally friendly sputtering processes by reducing energy consumption and using less hazardous materials.
In summary, sputtering is a versatile and precise technique for depositing thin films, with applications across various industries. By understanding the principles and components involved, as well as the advantages and challenges, one can effectively utilize sputtering for a wide range of material deposition needs.
Summary Table:
Aspect | Details |
---|---|
Process | Bombarding a target material with high-energy ions in a vacuum chamber. |
Key Components | Target material, substrate, vacuum chamber, inert gas (e.g., argon). |
Advantages | Precision, versatility, high-quality films, scalability. |
Applications | Semiconductors, optics, coatings, magnetic storage. |
Types of Sputtering | DC, RF, Magnetron, Reactive Sputtering. |
Challenges | Contamination, target erosion, uniformity. |
Future Developments | HiPIMS, ALD integration, green sputtering. |
Discover how sputtering can enhance your material deposition process—contact our experts today!