X-ray fluorescence (XRF) thickness measurement is based on the principle of X-ray fluorescence, where a sample is irradiated with X-rays, causing the atoms in the sample to emit secondary X-rays with specific energy characteristics. These secondary X-rays are detected and analyzed to determine the elemental composition and thickness of the sample. The intensity of the emitted X-rays is proportional to the thickness of the coating or layer, allowing for precise measurement.
Key Points Explained:
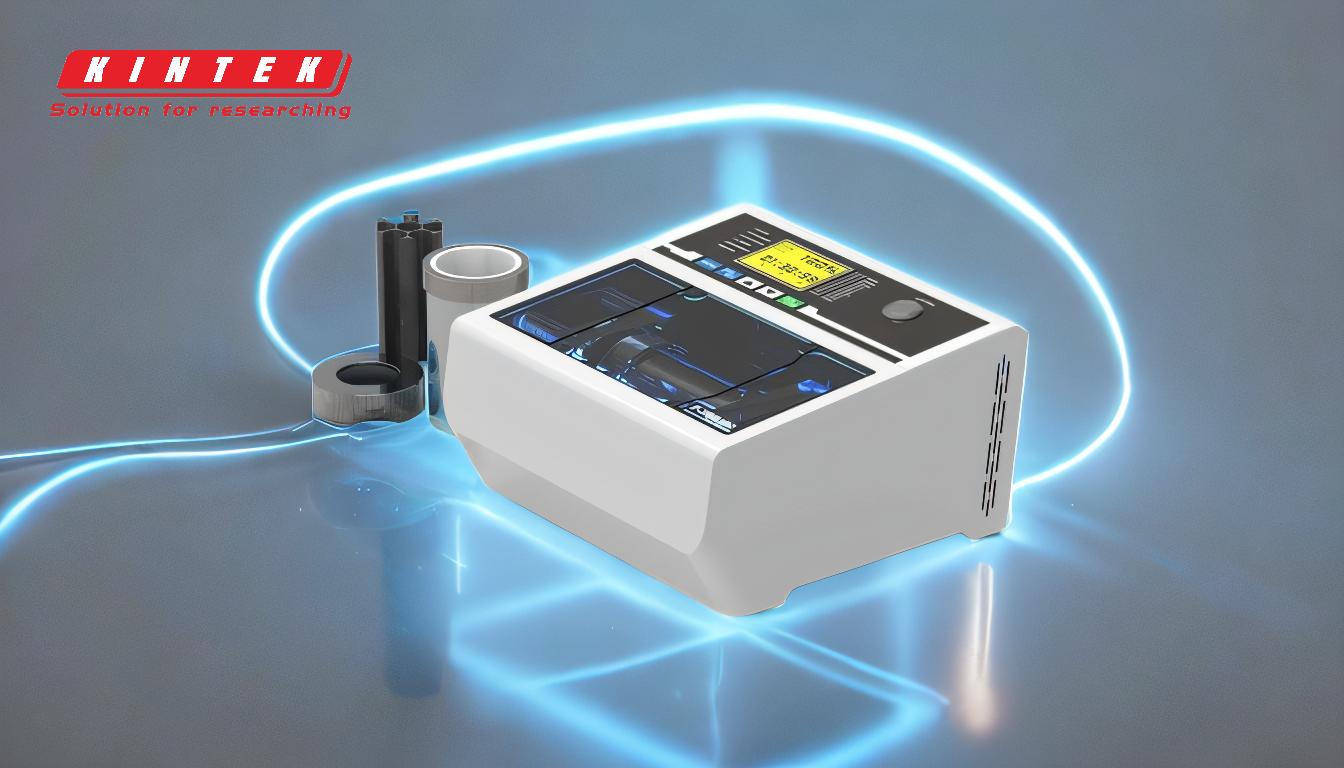
-
Excitation of Atoms:
- When a sample is exposed to primary X-rays generated by an X-ray tube, the energy from these X-rays is sufficient to eject inner-shell electrons (e.g., from the K or L shells) from the atoms in the sample.
- This creates electron vacancies in the inner shells, which are then filled by electrons from higher energy shells. During this transition, energy is released in the form of secondary X-rays, known as X-ray fluorescence.
-
Element-Specific X-ray Emission:
- The energy of the emitted secondary X-rays is characteristic of the specific element from which they originate. Each element has a unique set of energy levels, resulting in a unique X-ray fluorescence spectrum.
- By detecting the energy of these secondary X-rays, the XRF instrument can identify the elements present in the sample.
-
Intensity and Thickness Relationship:
- The intensity of the emitted X-ray fluorescence is directly related to the amount of the element present in the sample. For thickness measurement, this intensity is proportional to the thickness of the coating or layer.
- As the thickness of the coating increases, the intensity of the emitted X-rays increases up to a certain point, after which it may plateau due to saturation effects.
-
Detection and Analysis:
- The XRF instrument detects the energy and intensity of the secondary X-rays using a detector, such as a silicon drift detector (SDD) or a proportional counter.
- The detected signals are then processed by the instrument's software, which calculates the elemental composition and thickness based on the known relationship between X-ray intensity and thickness.
-
Calibration and Accuracy:
- To ensure accurate thickness measurements, the XRF instrument must be calibrated using standards with known thicknesses and compositions.
- Calibration curves are created by measuring the X-ray fluorescence intensity from these standards, allowing the instrument to correlate intensity with thickness for unknown samples.
-
Applications of XRF Thickness Measurement:
- XRF thickness measurement is widely used in industries such as electronics, automotive, and aerospace for quality control and assurance.
- It is particularly useful for measuring the thickness of coatings, such as gold, silver, or nickel, on various substrates, ensuring that the coatings meet specified standards.
By understanding these principles, one can appreciate how XRF technology provides a non-destructive, accurate, and efficient method for measuring the thickness of coatings and layers in various materials.
Summary Table:
Key Aspect | Description |
---|---|
Excitation of Atoms | Primary X-rays eject inner-shell electrons, creating vacancies filled by higher-energy electrons, emitting secondary X-rays. |
Element-Specific Emission | Emitted X-rays have unique energy levels, identifying elements in the sample. |
Intensity & Thickness | X-ray intensity is proportional to coating thickness, enabling precise measurement. |
Detection & Analysis | Detectors (e.g., SDD) measure X-ray energy and intensity, processed by software. |
Calibration & Accuracy | Calibration with known standards ensures accurate thickness measurements. |
Applications | Used in electronics, automotive, and aerospace for quality control of coatings. |
Discover how XRF thickness measurement can improve your quality control—contact our experts today!