Pyrolysis oil, derived from biomass through thermal decomposition, faces several challenges that limit its widespread adoption as a fuel. These challenges include instability over time, compositional complexity, lack of standardization, and technical hurdles in production. While it offers potential as a renewable energy source, its lower quality and economic competitiveness compared to conventional fuels hinder its commercial use. Efforts to upgrade pyrolysis oil and address these issues are ongoing, suggesting future possibilities for its broader application.
Key Points Explained:
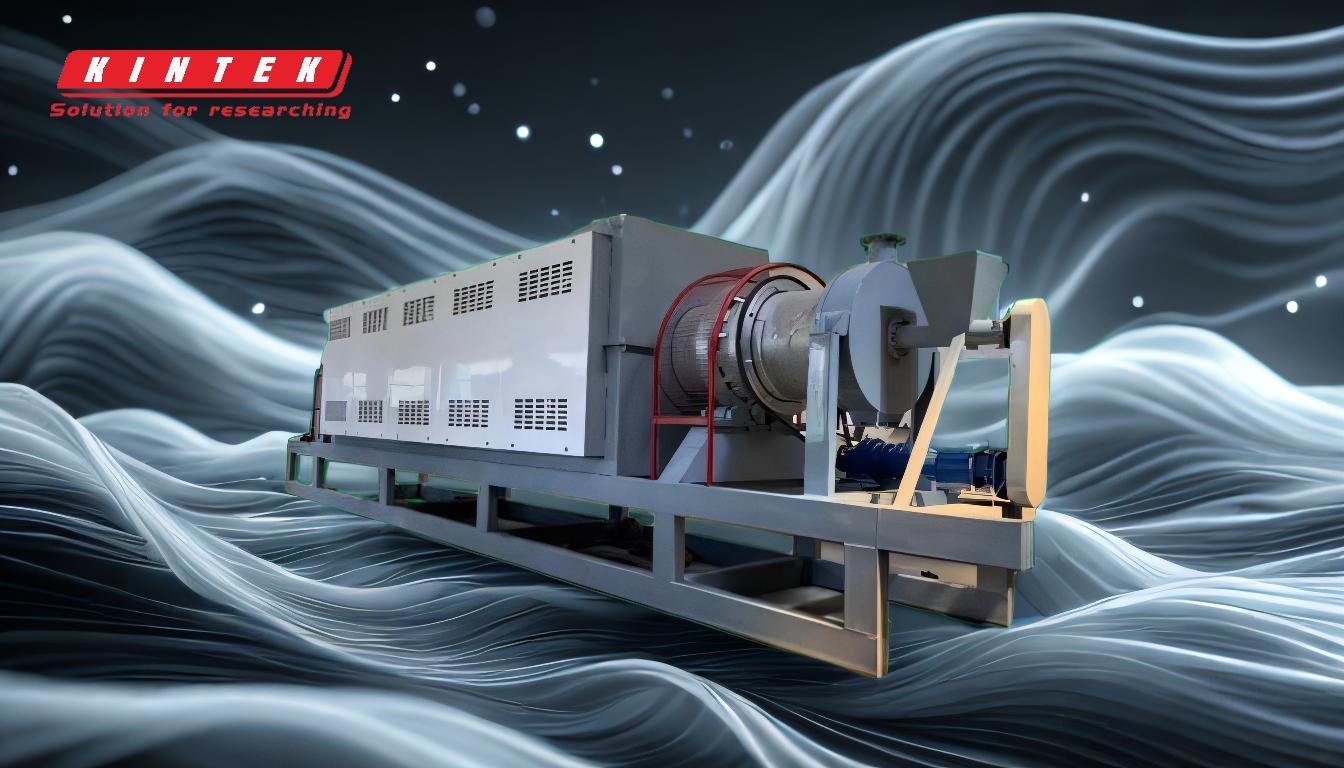
-
Instability Over Time:
- Pyrolysis oil is composed of intermediate, reactive decomposition products, making it inherently unstable.
- Over time, even when stored, pyrolysis oil undergoes gradual changes such as increased viscosity and potential phase separation due to condensation reactions.
- Heating the oil to temperatures above 100 °C accelerates these reactions, leading to the formation of solid residues and volatile organic compounds. This instability complicates storage and handling, limiting its practicality as a fuel.
-
Complex Composition:
- Pyrolysis oil is a liquid emulsion containing oxygenated organic compounds, polymers, and water, with oxygen content up to 40% by weight.
- It includes a wide range of chemicals, from low molecular weight compounds like formaldehyde and acetic acid to high molecular weight phenols and oligosaccharides.
- This complex mixture contributes to its instability and variability, making it difficult to standardize and process.
-
Lack of Standardization:
- There are few established standards for pyrolysis oil, primarily due to limited production efforts and the variability in its composition.
- ASTM provides one of the few standards, but the absence of widespread regulatory frameworks complicates its adoption and integration into existing fuel infrastructure.
-
Technical Challenges in Production:
- Pyrolysis technology faces several technical hurdles, including reducing parasitic energy losses, improving reactor designs, and enhancing feedstock logistics.
- Increasing the biomass heating rate and addressing the accumulation of metal and ash in reactor bed materials are critical to improving bio-oil yields and quality.
- These challenges increase production costs and reduce the economic viability of pyrolysis oil as a fuel.
-
Economic Competitiveness:
- Despite being easily stored and transported, pyrolysis oil has not been widely adopted for commercial use due to its lower quality compared to conventional fuels.
- Its lack of economic competitiveness stems from higher production costs, instability, and the need for further processing to upgrade its quality.
- Ongoing research and development efforts aim to improve pyrolysis oil's properties and reduce costs, potentially making it a viable alternative fuel in the future.
-
Future Potential:
- While current limitations hinder its widespread use, pyrolysis oil holds promise as a renewable energy source.
- Advances in upgrading techniques, such as catalytic upgrading and hydrotreatment, could enhance its stability, reduce oxygen content, and improve its compatibility with existing fuel systems.
- Continued innovation in pyrolysis technology and supportive policies may pave the way for its broader commercial applicability in the future.
In summary, pyrolysis oil faces significant challenges related to stability, composition, standardization, and production efficiency. However, ongoing research and technological advancements offer hope for overcoming these obstacles, potentially enabling its use as a sustainable alternative fuel.
Summary Table:
Challenge | Description |
---|---|
Instability Over Time | Reactivity and changes in viscosity or phase separation limit storage and use. |
Complex Composition | High oxygen content and diverse chemical mixture hinder standardization. |
Lack of Standardization | Few regulatory frameworks and variability in composition complicate adoption. |
Technical Challenges | High production costs and inefficiencies reduce economic viability. |
Economic Competitiveness | Lower quality and higher costs compared to conventional fuels limit adoption. |
Future Potential | Upgrading techniques and innovation may improve stability and commercial use. |
Want to learn more about pyrolysis oil and its potential as a renewable fuel? Contact us today for expert insights!