Magnetron sputtering is a highly efficient physical vapor deposition (PVD) technique used to create thin films on substrates. The process involves creating a high vacuum environment, introducing an inert gas (typically argon), and applying a high voltage to generate plasma. A magnetic field confines electrons near the target surface, increasing plasma density and deposition rates. Positively charged argon ions collide with the negatively charged target, ejecting atoms that then travel to and adhere to the substrate, forming a thin film. This method is widely used in industries such as semiconductors, optics, and coatings due to its precision, uniformity, and ability to deposit a wide range of materials.
Key Points Explained:
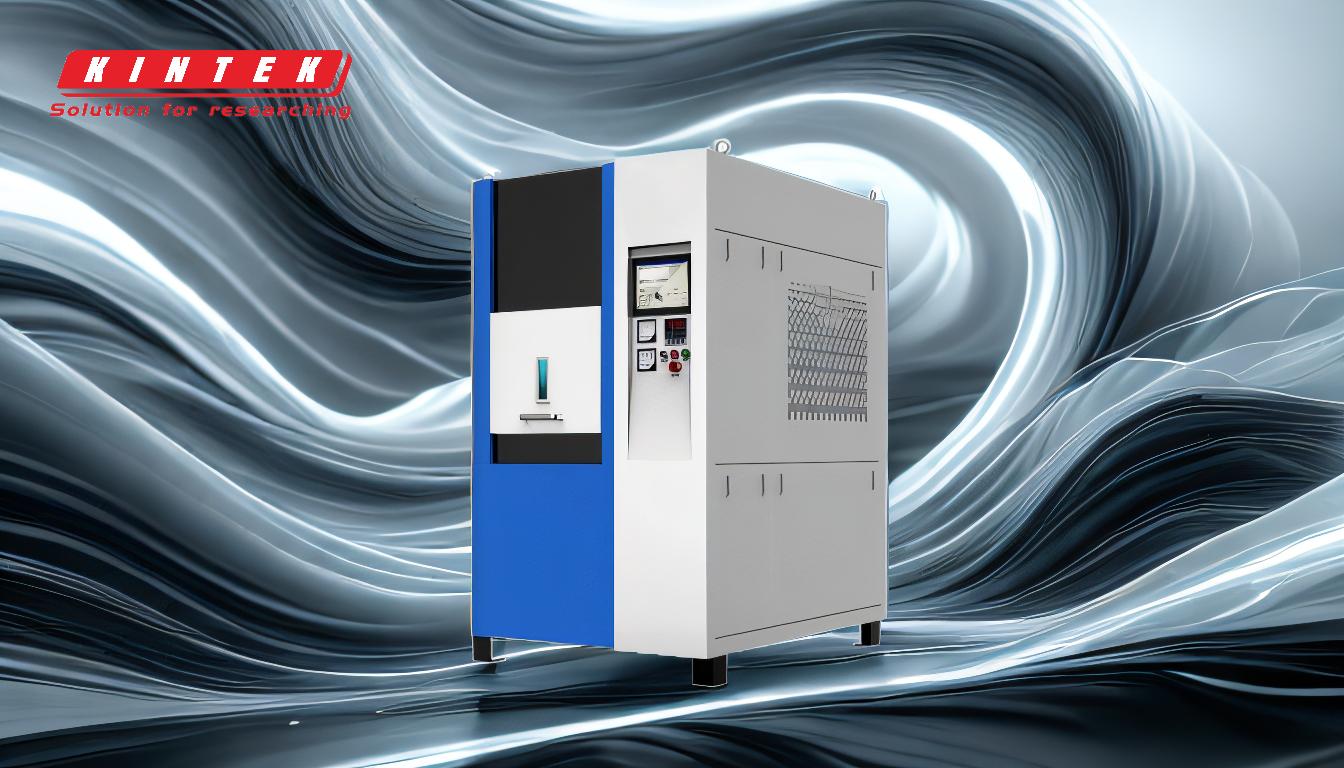
-
Vacuum Chamber Preparation:
- The process begins by evacuating the chamber to create a high vacuum environment. This step is crucial to minimize contaminants and ensure a clean deposition process.
- A high vacuum reduces the presence of unwanted gases and particles, which could interfere with the thin film's quality and adhesion.
-
Introduction of Sputtering Gas:
- An inert gas, typically argon, is introduced into the vacuum chamber. The gas pressure is maintained in the milli Torr range.
- Argon is chosen because it is chemically inert, reducing the risk of unwanted chemical reactions during the sputtering process.
-
Generation of Plasma:
- A high negative voltage is applied between the cathode (target) and anode, ionizing the argon gas and creating a plasma.
- The plasma consists of positively charged argon ions, free electrons, and neutral argon atoms.
-
Magnetic Field Confinement:
- A magnetic field is generated using magnet arrays near the target surface. This field confines electrons, increasing their path length and enhancing the probability of ionizing argon atoms.
- The confined electrons create a dense plasma near the target, which significantly increases the deposition rate.
-
Sputtering of Target Material:
- Positively charged argon ions from the plasma are accelerated toward the negatively charged target (cathode).
- When these high-energy ions collide with the target, they eject (sputter) atoms from the target material.
-
Deposition onto Substrate:
- The ejected target atoms travel through the vacuum chamber and deposit onto the substrate surface.
- These atoms condense and form a thin film, adhering to the substrate due to physical and sometimes chemical bonding.
-
Control of Deposition Parameters:
- The deposition rate, film thickness, and uniformity can be controlled by adjusting parameters such as gas pressure, voltage, magnetic field strength, and target-substrate distance.
- Precise control of these parameters ensures high-quality thin films with desired properties.
-
Advantages of Magnetron Sputtering:
- High Deposition Rates: The magnetic field increases plasma density, leading to faster deposition.
- Uniform Films: The process allows for the deposition of uniform thin films over large areas.
- Versatility: A wide range of materials, including metals, alloys, and ceramics, can be deposited using this method.
- Low Substrate Damage: The magnetic field helps protect the substrate from ion bombardment, reducing damage and improving film quality.
-
Applications:
- Semiconductor Industry: Used for depositing thin films in the fabrication of integrated circuits and microelectronics.
- Optical Coatings: Applied in the production of anti-reflective coatings, mirrors, and optical filters.
- Decorative Coatings: Utilized for creating durable and aesthetically pleasing coatings on various consumer products.
- Protective Coatings: Used to deposit wear-resistant and corrosion-resistant coatings on tools and components.
-
Challenges and Considerations:
- Target Erosion: The target material erodes over time, requiring periodic replacement or resurfacing.
- Heat Management: The process generates heat, which must be managed to prevent damage to the substrate and maintain film quality.
- Cost: High vacuum equipment and target materials can be expensive, making the process costlier compared to some other deposition methods.
In summary, magnetron sputtering is a sophisticated and versatile thin film deposition technique that leverages high vacuum, plasma, and magnetic fields to achieve precise and high-quality coatings. Its ability to deposit a wide range of materials with excellent control over film properties makes it indispensable in various high-tech industries.
Summary Table:
Key Aspect | Details |
---|---|
Process | High vacuum, argon gas, plasma generation, magnetic field confinement. |
Advantages | High deposition rates, uniform films, versatility, low substrate damage. |
Applications | Semiconductors, optical coatings, decorative coatings, protective coatings. |
Challenges | Target erosion, heat management, high equipment costs. |
Discover how magnetron sputtering can enhance your processes—contact us today!