The catalytic pyrolysis process is a thermochemical decomposition method used to convert materials like plastic waste or biomass into valuable products such as liquid oil, gases, and solid residues. This process involves pre-treating the feedstock to remove impurities, grinding it to the required size, and loading it into a pyrolysis reactor with a catalyst. The material is heated to temperatures between 200-900°C in the absence of oxygen, causing it to break down into smaller molecules. The vapors produced are condensed into liquid oil, which is further refined for use as fuel. The process is energy-intensive and requires precise control of temperature and pressure to optimize product yield and quality.
Key Points Explained:
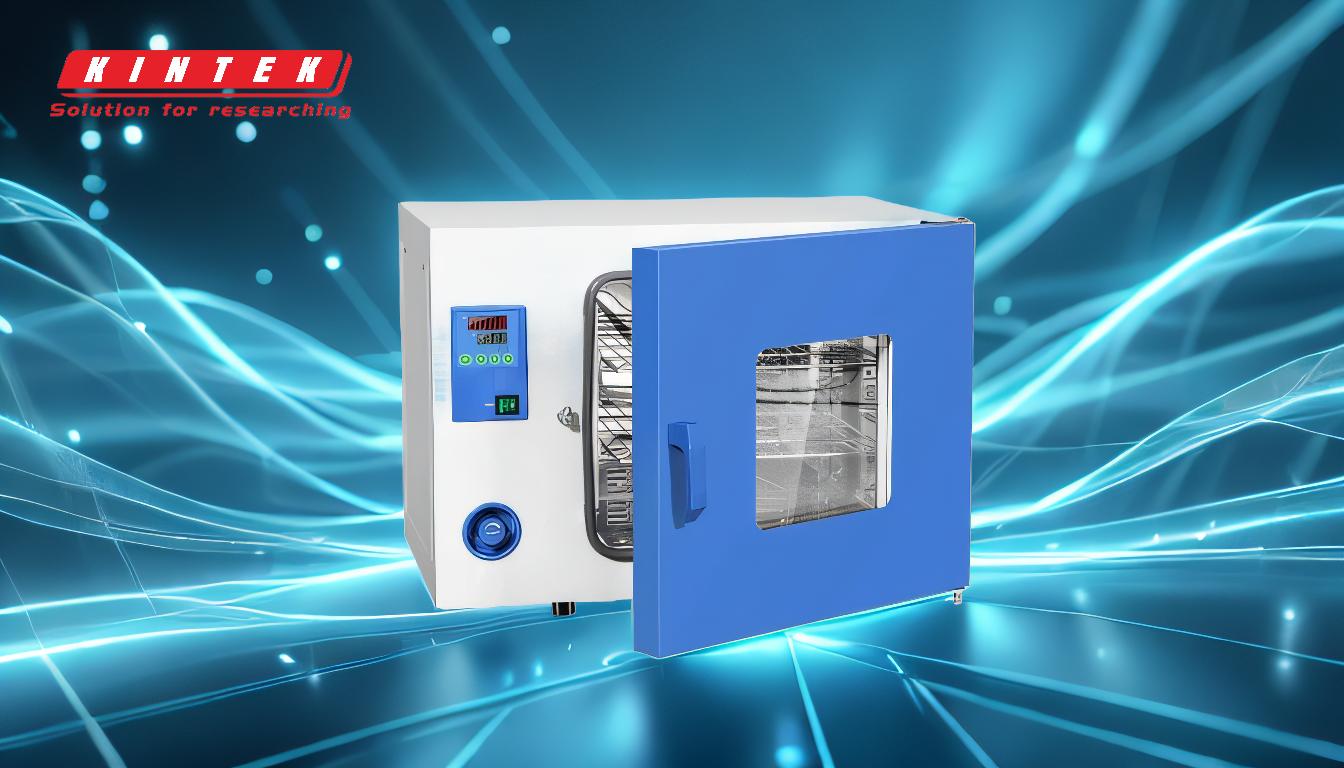
-
Feedstock Preparation:
- Pre-treatment: The feedstock, such as plastic waste or biomass, is first cleaned to remove impurities like dirt, metals, or non-plastic materials. This ensures the quality of the final products and prevents damage to the equipment.
- Grinding/Shredding: The material is ground or shredded into smaller particles to increase the surface area, which enhances the efficiency of the pyrolysis process.
-
Loading into the Pyrolysis Reactor:
- The prepared feedstock is loaded into a pyrolysis reactor along with a catalyst. The catalyst plays a crucial role in lowering the activation energy required for the decomposition of the material, improving the efficiency of the process and the quality of the products.
-
Heating and Decomposition:
- The reactor is heated to a temperature range of 200-900°C in the absence of oxygen. This thermochemical decomposition breaks down the large molecules in the feedstock into smaller molecules, producing gases, liquids, and solid residues.
- The absence of oxygen prevents combustion, ensuring that the material decomposes rather than burns.
-
Vapor Condensation:
- The vapors produced during the decomposition process are condensed into liquid oil, also known as pyrolysis oil or bio-oil. This oil can be further refined and used as fuel or as a feedstock for other chemical processes.
-
Product Separation:
- The solid residue, known as biochar, settles at the bottom of the reactor and is collected for further use or disposal.
- Non-condensable gases, such as syngas, are often recycled back into the combustion chamber to provide heat for the process, improving energy efficiency.
-
Refining and Storage:
- The liquid oil undergoes further distillation and purification to remove any remaining impurities and improve its quality.
- The final products, including the refined oil, biochar, and gases, are stored or dispatched for use in various applications.
-
Catalyst Role:
- The catalyst used in the process can vary depending on the feedstock and desired products. Common catalysts include zeolites, metal oxides, and other materials that enhance the breakdown of the feedstock and improve the yield of valuable products.
-
Energy and Environmental Considerations:
- Catalytic pyrolysis is an energy-intensive process that requires precise control of temperature and pressure to optimize product yield and quality.
- The process helps reduce waste by converting non-recyclable materials into useful products, contributing to a circular economy and reducing environmental impact.
-
Applications of Products:
- Pyrolysis Oil: Can be used as a fuel or further refined into chemicals.
- Biochar: Used in agriculture as a soil amendment or in industrial applications.
- Syngas: Can be used as a fuel or converted into other chemicals.
-
Challenges and Optimization:
- The process requires careful optimization of parameters such as temperature, heating rate, and catalyst type to maximize product yield and quality.
- Challenges include managing the energy requirements, ensuring consistent feedstock quality, and minimizing environmental emissions.
By following these steps, catalytic pyrolysis provides an effective method for converting waste materials into valuable resources, contributing to waste reduction and sustainable resource management.
Summary Table:
Step | Description |
---|---|
Feedstock Preparation | Clean and grind feedstock to remove impurities and increase surface area. |
Loading into Reactor | Load feedstock with a catalyst into the pyrolysis reactor. |
Heating & Decomposition | Heat to 200-900°C without oxygen to break down materials into smaller molecules. |
Vapor Condensation | Condense vapors into liquid oil (pyrolysis oil). |
Product Separation | Collect biochar and recycle non-condensable gases for energy efficiency. |
Refining & Storage | Refine liquid oil and store final products for various applications. |
Catalyst Role | Use catalysts like zeolites or metal oxides to enhance decomposition efficiency. |
Applications | Pyrolysis oil as fuel, biochar for agriculture, and syngas for energy. |
Discover how catalytic pyrolysis can revolutionize waste management—contact us today to learn more!