Chemical vapor deposition (CVD) is a widely used process in semiconductor manufacturing to create thin films of materials on substrates. The process involves introducing gaseous precursors into a reaction chamber, activating them through thermal energy, plasma, or catalysts, and allowing them to react on the substrate surface to form a solid film. Byproducts are then removed to ensure a clean deposition. The process is highly controlled, with precise temperature, pressure, and gas flow conditions to achieve uniform and high-quality films. CVD is essential for creating semiconductor devices, as it allows for the deposition of materials with specific electrical, thermal, and mechanical properties.
Key Points Explained:
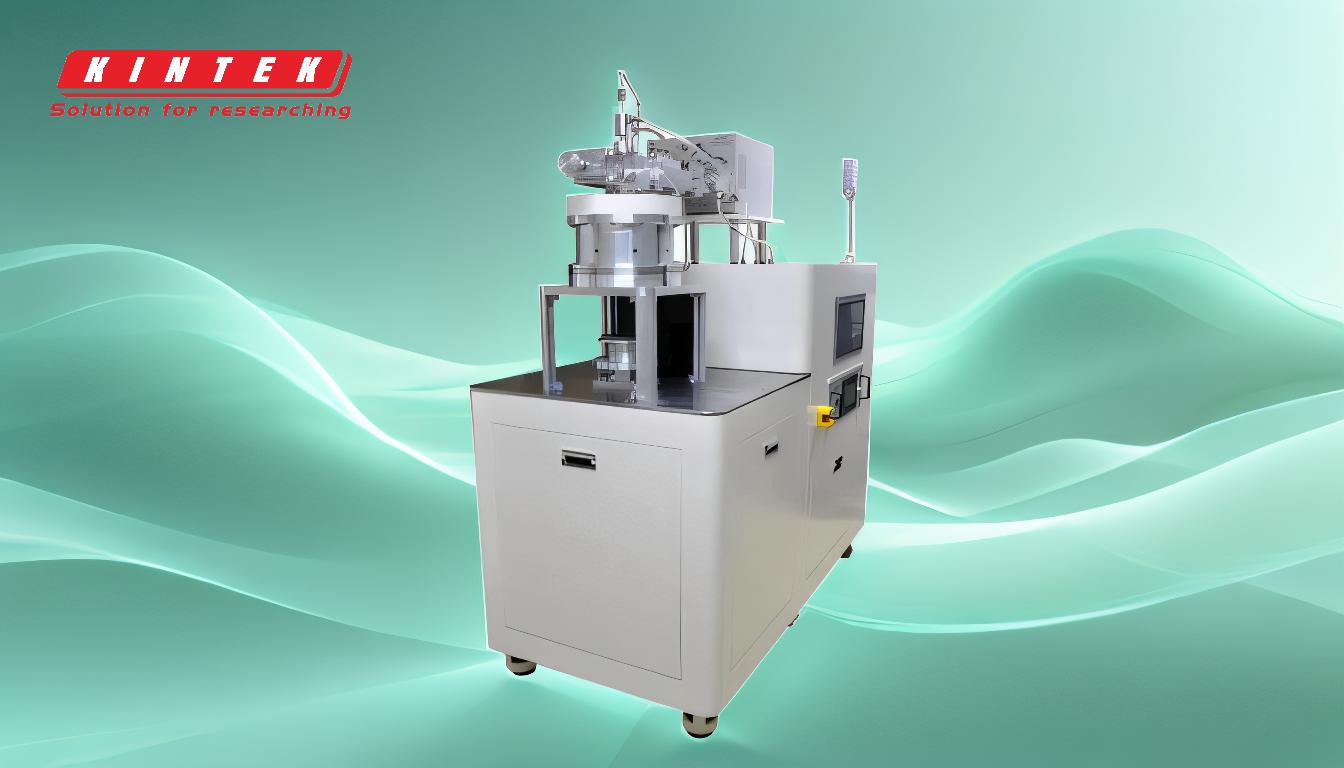
-
Introduction of Reactants:
- Gaseous precursors are introduced into a reaction chamber containing the substrate. These precursors are typically volatile compounds that can be vaporized and transported to the substrate surface. The choice of precursors depends on the desired material to be deposited, such as silicon dioxide, silicon nitride, or metals like tungsten.
-
Activation of Reactants:
- The precursors are activated through methods such as thermal energy, plasma, or catalysts. Thermal activation involves heating the substrate to high temperatures (often 500-1200°C) to break chemical bonds in the precursors. Plasma-enhanced CVD (PECVD) uses plasma to provide energy for activation, allowing deposition at lower temperatures. Catalysts can also be used to lower the activation energy required for the reaction.
-
Surface Reaction and Deposition:
- Once activated, the precursors react at the substrate surface to form the desired material. This involves several sub-steps:
- Adsorption: The activated species adsorb onto the substrate surface.
- Surface Diffusion: The adsorbed species diffuse to growth sites on the substrate.
- Nucleation and Growth: The species form nuclei, which grow into a continuous film.
- Chemisorption: Chemical bonds form between the deposited material and the substrate, ensuring strong adhesion.
- Once activated, the precursors react at the substrate surface to form the desired material. This involves several sub-steps:
-
Removal of Byproducts:
- Volatile or non-volatile byproducts are generated during the reaction. These byproducts must be removed from the reaction chamber to prevent contamination and ensure the purity of the deposited film. This is typically done through vacuum pumping or purging with inert gases.
-
Process Control:
- The CVD process requires precise control of several parameters:
- Temperature: The substrate temperature must be carefully controlled to ensure proper activation and deposition.
- Pressure: The pressure in the reaction chamber affects the rate of deposition and the quality of the film.
- Gas Flow: The flow rate of the precursors and carrier gases must be optimized to achieve uniform deposition.
- Time: The duration of the deposition process affects the thickness and quality of the film.
- The CVD process requires precise control of several parameters:
-
Applications in Semiconductor Manufacturing:
- CVD is used to deposit a wide range of materials in semiconductor devices, including:
- Dielectric Layers: Silicon dioxide and silicon nitride are commonly deposited using CVD to create insulating layers.
- Conductive Layers: Metals like tungsten and copper are deposited using CVD for interconnects.
- Semiconductor Layers: Silicon and other semiconductor materials are deposited to form active regions in transistors and other devices.
- CVD is used to deposit a wide range of materials in semiconductor devices, including:
-
Advantages of CVD:
- High Purity: CVD can produce films with very high purity, which is essential for semiconductor applications.
- Uniformity: The process can deposit films with excellent uniformity over large areas.
- Conformality: CVD can deposit films on complex geometries with good step coverage, making it suitable for 3D structures in modern semiconductor devices.
-
Challenges and Considerations:
- High Temperatures: Some CVD processes require very high temperatures, which can limit the choice of substrate materials.
- Cost: The equipment and precursors used in CVD can be expensive, making the process costly for some applications.
- Safety: The use of toxic or flammable gases in CVD requires careful handling and safety precautions.
In summary, the CVD process is a critical technology in semiconductor manufacturing, enabling the deposition of high-quality thin films with precise control over material properties. The process involves multiple steps, from the introduction and activation of reactants to the removal of byproducts, and requires careful control of process parameters to achieve the desired results.
Summary Table:
Step | Description |
---|---|
Introduction of Reactants | Gaseous precursors are introduced into the reaction chamber. |
Activation of Reactants | Precursors are activated via thermal energy, plasma, or catalysts. |
Surface Reaction | Activated precursors react on the substrate to form a solid film. |
Byproduct Removal | Byproducts are removed to ensure a clean deposition. |
Process Control | Precise control of temperature, pressure, gas flow, and time is maintained. |
Applications | Used for dielectric, conductive, and semiconductor layers in devices. |
Advantages | High purity, uniformity, and conformality of deposited films. |
Challenges | High temperatures, cost, and safety considerations. |
Discover how CVD can enhance your semiconductor manufacturing process—contact our experts today!