The process of Low-Pressure Chemical Vapor Deposition (LPCVD) for silicon nitride involves depositing a thin film of silicon nitride onto a substrate under reduced pressure conditions, typically below 133 Pa. This method is advantageous due to its ability to produce highly uniform, pure, and reproducible films. The process operates at elevated temperatures, usually above 600°C, which facilitates the chemical reactions necessary for film formation. LPCVD is widely used in semiconductor manufacturing for depositing silicon nitride due to its excellent film properties and trench-filling capabilities.
Key Points Explained:
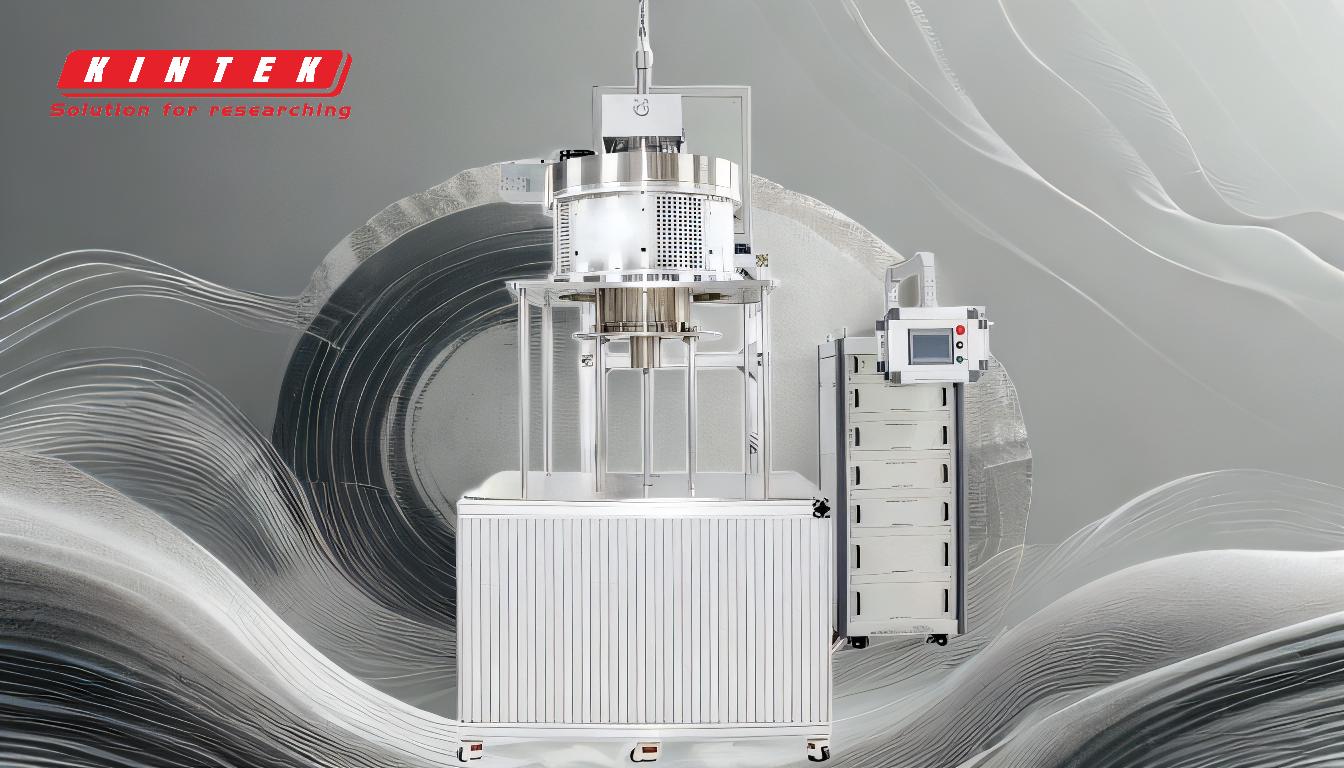
-
Operating Pressure in LPCVD:
- LPCVD operates at reduced pressures, typically between 0.1 to 10 Torr (approximately 133 Pa or less). This low-pressure environment increases the mean free path of gas molecules and enhances the diffusion coefficient, which accelerates the mass transfer rate of reactants and by-products. This results in faster reaction rates and improved film quality.
-
Deposition Temperature:
- LPCVD requires high temperatures, often exceeding 600°C. The elevated temperature is crucial for activating the chemical reactions that form the silicon nitride film. High temperatures also contribute to the uniformity and purity of the deposited film, making LPCVD suitable for applications requiring high-quality thin films.
-
Film Uniformity and Quality:
- The low-pressure environment and high temperatures in LPCVD lead to highly uniform films with excellent resistivity uniformity and trench coverage. This uniformity is essential for applications in semiconductor devices, where consistent film properties are critical for device performance.
-
Applications of LPCVD Silicon Nitride:
- Silicon nitride films deposited via LPCVD are used in various applications, including as dielectric layers, passivation layers, and masking layers in semiconductor devices. The films are also used in MEMS (Micro-Electro-Mechanical Systems) and optoelectronic devices due to their excellent mechanical and optical properties.
-
Advantages of LPCVD:
- High Purity: The low-pressure environment minimizes contamination, resulting in high-purity films.
- Reproducibility: LPCVD provides consistent film properties across different batches, which is crucial for mass production.
- Trench Filling: The process is capable of filling high-aspect-ratio trenches, which is important for advanced semiconductor devices.
-
Comparison with Other CVD Methods:
- LPCVD differs from other CVD methods, such as Atmospheric Pressure CVD (APCVD) and Plasma-Enhanced CVD (PECVD), primarily in terms of operating pressure and temperature. LPCVD's higher temperatures and lower pressures result in films with better uniformity and purity compared to these other methods.
In summary, the LPCVD process for silicon nitride is a highly controlled method that leverages low pressure and high temperature to produce uniform, high-quality films. These films are essential for various advanced applications in the semiconductor and MEMS industries.
Summary Table:
Key Aspect | Details |
---|---|
Operating Pressure | 0.1 to 10 Torr (≤133 Pa) |
Deposition Temperature | Above 600°C |
Film Uniformity | Highly uniform with excellent resistivity and trench coverage |
Applications | Dielectric layers, passivation layers, MEMS, optoelectronics |
Advantages | High purity, reproducibility, trench-filling capability |
Interested in leveraging LPCVD silicon nitride for your applications? Contact our experts today to learn more!