Pyrolysis is a thermal decomposition process that converts waste materials into energy and valuable byproducts in the absence of oxygen. The process involves several stages, including waste preparation, heating in a reactor, and the separation and refinement of output products such as syngas, bio-oil, and biochar. These products can be used for fuel, power generation, and other applications. The process is energy-efficient, as uncondensable gases are often recycled to heat the reactor. Pyrolysis is widely applied to various waste streams, including plastics, tires, and biomass, making it a sustainable solution for waste management and energy recovery.
Key Points Explained:
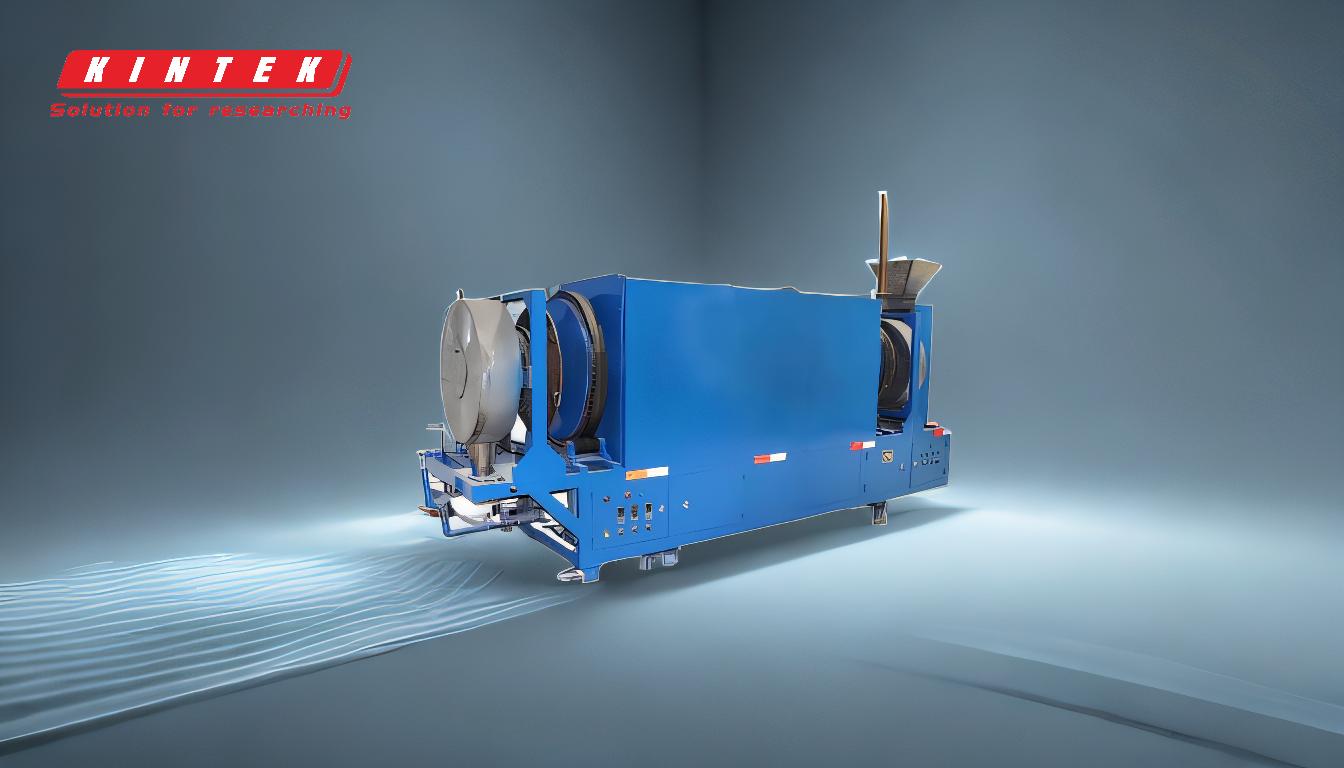
-
Waste Preparation and Pre-Treatment
- Mechanical Separation: Before pyrolysis, waste materials such as municipal solid waste, plastics, tires, or biomass undergo mechanical preparation. This step involves separating non-organic materials like glass, metals, and inert substances to ensure the feedstock is suitable for pyrolysis.
- Pre-Treatment: Depending on the waste type, additional pre-treatment steps may include drying, crushing, or grinding to achieve the required size and moisture content. For example, biomass is often dried and crushed, while plastics may be shredded to facilitate uniform heating.
-
Loading into the Pyrolysis Reactor
- Reactor Types: The prepared waste is loaded into a pyrolysis reactor, which can be a rotary kiln, rotary hearth furnace, fluidized bed furnace, or other specialized designs. The choice of reactor depends on the type of waste and the desired output.
- Catalyst Addition (Optional): In some cases, catalysts are added to enhance the pyrolysis reaction, particularly for plastic waste, to improve the yield and quality of liquid oil.
-
Heating and Thermal Decomposition
- Temperature Range: The waste is heated to temperatures between 200°C and 900°C in the absence of oxygen. The specific temperature depends on the waste material and the desired end products.
- Decomposition Process: At these high temperatures, the organic materials undergo thermal decomposition, breaking down into smaller molecules. This process produces a mixture of gases, liquids, and solids.
-
Product Formation and Separation
- Syngas: The gaseous output, known as syngas, contains combustible gases like hydrogen, methane, and carbon monoxide. This gas can be used directly as a fuel or further refined.
- Bio-Oil: The vapors produced during pyrolysis are condensed into liquid bio-oil, which can be refined into transportation fuels or used as a feedstock for chemical production.
- Biochar: The solid residue, or biochar, is a carbon-rich material that can be used as a soil amendment, activated carbon, or solid fuel.
-
Energy Efficiency and Recycling
- Gas Recycling: Uncondensable gases from the pyrolysis process are often recycled back to the reactor burner to provide heat, making the process energy-efficient and reducing external energy requirements.
- Flue Gas Treatment: The exhaust gases are treated using purification systems to remove harmful substances before being discharged, ensuring environmental compliance.
-
Applications of Pyrolysis Products
- Energy Generation: Syngas and bio-oil can be used for power generation or as alternative fuels in industrial processes.
- Soil Amendment: Biochar improves soil fertility and carbon sequestration, making it valuable for agricultural applications.
- Chemical Feedstock: Bio-oil can serve as a precursor for producing chemicals and other industrial products.
-
Advantages of Pyrolysis
- Waste Reduction: Pyrolysis significantly reduces the volume of waste, diverting it from landfills and reducing environmental pollution.
- Resource Recovery: The process recovers valuable resources from waste, contributing to a circular economy.
- Versatility: Pyrolysis can handle a wide range of waste materials, including plastics, tires, and biomass, making it a flexible solution for waste management.
By following this structured process, pyrolysis effectively transforms waste into energy and valuable products, offering a sustainable and efficient approach to waste management and resource recovery.
Summary Table:
Stage | Key Details |
---|---|
Waste Preparation | Mechanical separation, drying, crushing, or grinding for uniform heating. |
Loading into Reactor | Reactor types: rotary kiln, fluidized bed, etc. Optional catalyst addition. |
Heating & Decomposition | 200°C–900°C in oxygen-free environment; thermal breakdown into gases, liquids, solids. |
Product Formation | Syngas (combustible gases), bio-oil (liquid fuel), biochar (solid residue). |
Energy Efficiency | Uncondensable gases recycled to heat reactor; flue gas treatment for compliance. |
Applications | Power generation, soil amendment, chemical feedstock. |
Advantages | Waste reduction, resource recovery, versatility for plastics, tires, biomass. |
Ready to explore pyrolysis solutions for your waste management needs? Contact us today to learn more!