Thin film manufacturing in semiconductor production is a complex and highly controlled process that involves depositing thin layers of material onto a substrate. This process is critical for creating the intricate structures needed in semiconductor devices. The primary methods used include Physical Vapour Deposition (PVD), Chemical Vapour Deposition (CVD), and Atomic Layer Deposition (ALD). Each method has its own set of steps and considerations, but they all aim to achieve precise control over the thickness and composition of the films. The process typically involves selecting a pure material source, transporting it to a prepared substrate, depositing the material, and optionally subjecting the film to annealing or heat treatment. The properties of the film are then analyzed to ensure they meet the required specifications, and the deposition process may be modified if necessary.
Key Points Explained:
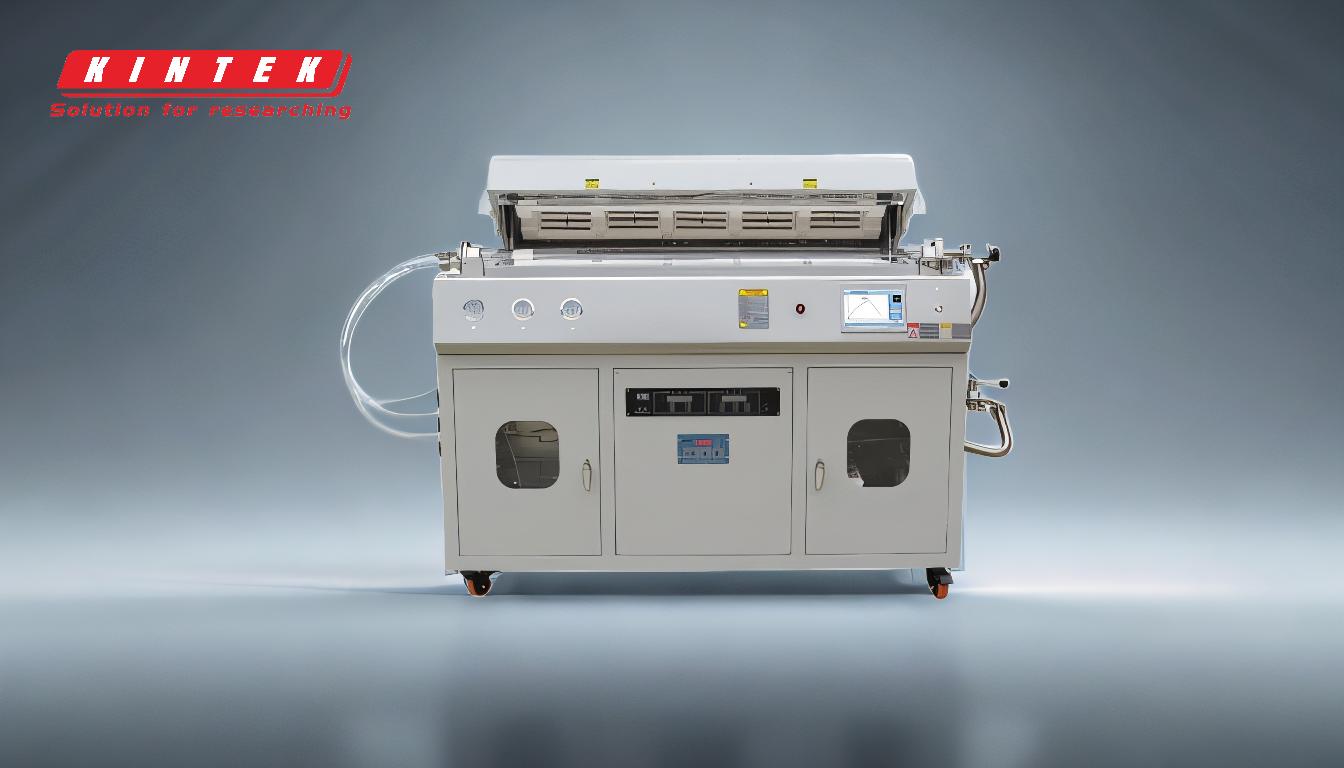
-
Selection of Deposition Method:
- Physical Vapour Deposition (PVD): This method involves evaporating or sputtering the source material, which then condenses on the substrate. Techniques like magnetron sputtering are commonly used.
- Chemical Vapour Deposition (CVD): This method uses chemical reactions to deposit a thin coating on the substrate. It is widely used for creating high-quality, uniform films.
- Atomic Layer Deposition (ALD): This technique deposits films one atomic layer at a time, allowing for extremely precise control over film thickness and composition.
- Spray Pyrolysis: This involves spraying a material solution onto the substrate and thermally degrading it to form a thin layer.
-
Preparation of Substrate:
- The substrate must be thoroughly cleaned and prepared to ensure proper adhesion of the thin film. This may involve chemical cleaning, etching, or other surface treatments.
-
Deposition Process:
- Evaporation: The source material is heated to a high temperature, causing it to evaporate and then condense on the substrate.
- Sputtering: High-energy particles bombard the source material, causing atoms to be ejected and deposited onto the substrate.
- Chemical Reactions: In CVD, precursor gases react on the substrate surface to form the desired film.
- Layer-by-Layer Deposition: In ALD, the film is built up one atomic layer at a time, ensuring precise control over thickness and uniformity.
-
Post-Deposition Treatments:
- Annealing: The film may be subjected to heat treatment to improve its properties, such as crystallinity and adhesion.
- Etching: Unwanted material is removed using chemical or physical methods to achieve the desired pattern or structure.
- Doping: Impurities are introduced into the semiconductor material to modify its electrical properties.
-
Analysis and Quality Control:
- The properties of the thin film, such as thickness, composition, and uniformity, are analyzed using various techniques like X-ray diffraction, electron microscopy, and spectroscopy.
- The results of these analyses are used to refine the deposition process and ensure the film meets the required specifications.
-
Applications and Considerations:
- Thin films are used in a wide range of applications, including flexible solar cells, organic light-emitting diodes (OLEDs), and semiconductor devices.
- The choice of deposition method and materials depends on the specific application and the desired properties of the film.
By following these steps, manufacturers can produce thin films with the precise characteristics needed for advanced semiconductor devices. The process requires careful control and optimization to ensure the final product meets the stringent requirements of modern electronics.
Summary Table:
Step | Details |
---|---|
Deposition Methods | PVD (evaporation, sputtering), CVD (chemical reactions), ALD (layer-by-layer) |
Substrate Preparation | Cleaning, etching, and surface treatments for proper adhesion |
Deposition Process | Evaporation, sputtering, chemical reactions, or layer-by-layer deposition |
Post-Deposition Treatments | Annealing, etching, and doping to enhance film properties |
Quality Control | Analysis using X-ray diffraction, electron microscopy, and spectroscopy |
Applications | Flexible solar cells, OLEDs, and semiconductor devices |
Need expert guidance on thin film manufacturing for your semiconductor production? Contact us today to optimize your process!