Plasma Enhanced Chemical Vapor Deposition (PECVD) is a versatile thin-film deposition technique that leverages plasma energy to enable chemical reactions at lower temperatures compared to traditional CVD methods. This process is particularly advantageous for depositing high-quality films like silicon nitride, silicon dioxide, and silicon oxynitride on various substrates. PECVD operates by generating a plasma through an RF electric field, which ionizes gas molecules and creates reactive species that deposit on a heated substrate. The process involves several microscopic steps, including gas molecule activation, diffusion, and surface reactions, resulting in dense, uniform films with strong adhesion. PECVD is widely used in industries for applications such as shallow bath isolation filling, sidewall isolation, and metal-linked media isolation, offering benefits like low deposition temperatures, energy efficiency, and cost savings.
Key Points Explained:
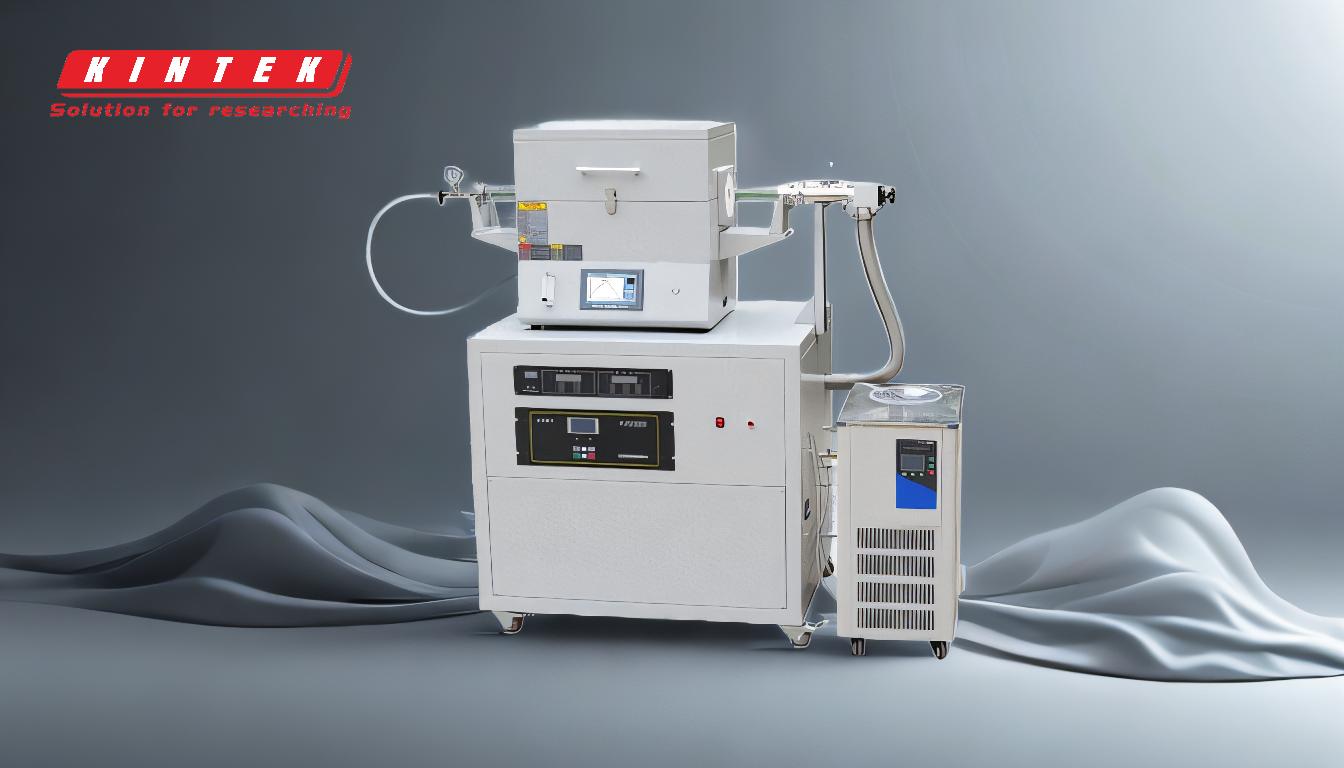
-
Introduction to PECVD:
- PECVD is a thin-film deposition technique that uses plasma to enable chemical reactions at lower temperatures than traditional CVD.
- It is widely used in industries for depositing films such as silicon nitride, silicon dioxide, and silicon oxynitride.
-
Plasma Generation:
- Plasma is generated by applying a high RF electric field near the substrate, typically at frequencies ranging from 100 kHz to 40 MHz.
- The plasma consists of ionized gas species, electrons, and neutral species in both ground and excited states, creating highly reactive species without significantly raising the gas temperature.
-
Process Conditions:
- PECVD operates in a reduced gas pressure environment, typically between 50 mtorr and 5 torr.
- The electron and positive ion densities range from 10^9 to 10^11/cm^3, with average electron energies ranging from 1 to 10 eV.
-
Microscopic Processes:
- Gas molecules collide with electrons in the plasma to produce active groups and ions.
- Active groups diffuse directly to the substrate or interact with other gas molecules to form chemical groups required for deposition.
- Chemical groups diffuse to the substrate surface, where they undergo deposition reactions and release reaction products.
-
Advantages of PECVD:
- Low Deposition Temperature: PECVD can be performed at temperatures as low as 100°C to 400°C, minimizing thermal stress on the substrate.
- High Film Quality: The films produced are dense, with few pinholes, and exhibit strong adhesion to the substrate.
- Uniformity: PECVD provides excellent thickness and composition uniformity across the substrate.
- Versatility: It can be used to deposit a wide range of materials, including silicon nitride, silicon dioxide, and amorphous silicon.
-
Applications of PECVD:
- Semiconductor Industry: Used for shallow bath isolation filling, sidewall isolation, and metal-linked media isolation.
- Optoelectronics: Depositing films for optical coatings and waveguides.
- MEMS and Sensors: Creating thin films for microelectromechanical systems and sensors.
-
Comparison with Traditional CVD:
- Unlike traditional CVD, which relies solely on thermal energy, PECVD utilizes both plasma energy and thermal energy to achieve the necessary chemical reactions.
- This allows PECVD to operate at significantly lower temperatures, making it suitable for temperature-sensitive substrates.
-
Process Steps in Silicon Nitride PECVD:
- The target wafer is placed on an electrode within the PECVD chamber.
- Reactive gases, such as silane (SiH4) and ammonia (NH3), are introduced into the chamber.
- Plasma is generated between the electrodes by applying an RF voltage, which dissociates the reactive gases into reactive species.
- These reactive species deposit on the wafer surface, forming a silicon nitride film.
By leveraging the unique capabilities of PECVD, manufacturers can achieve high-quality thin films with excellent uniformity and adhesion, all while operating at lower temperatures and reducing energy consumption. This makes PECVD an essential technique in modern semiconductor and optoelectronic manufacturing processes.
Summary Table:
Aspect | Details |
---|---|
Process | Plasma-enhanced chemical vapor deposition (PECVD) |
Key Gases | Silane (SiH4), Ammonia (NH3) |
Plasma Generation | RF electric field (100 kHz to 40 MHz) |
Pressure Range | 50 mtorr to 5 torr |
Temperature Range | 100°C to 400°C |
Advantages | Low deposition temperature, high film quality, uniformity, versatility |
Applications | Semiconductor isolation, optoelectronics, MEMS, and sensors |
Discover how PECVD can revolutionize your thin-film processes—contact our experts today!